L'evoluzione della tecnologia di simulazione di stampaggio materie plastiche è iniziata dalla simulazione di riempimento, e poi esteso a Runners e Gates e poi simulazione del sistema di raffreddamento. Successivamente, si sono aggiunti gli effetti degli inserti presenti nello stampo e, quindi, allo stampo nella sua completezza dei componenti; infatti la simulazione comprende oggi tutto l’ambiente stampo.
Nell'odierno mercato altamente competitivo, la richiesta della simulazione completa dello stampo è sempre più frequente, poiché la qualità del progetto stampo può altamente interessare il livello qualitativo del prodotto finale. Pensiamo, ad es., la disposizione e l’efficienza del sistema di raffreddamento.
Se la distribuzione della temperatura in una piastra dello stampo non è uniforme, i conseguenti contributi alla deformazione dello stesso stampo potrebbero creare inconvenienti gravi nel processo reale.
Così, il livello qualitativo del prodotto finale ne risentirà.
Lo stesso vale per una corretta individuazione delle linee di giunzione del materiale fuso e delle trappole d’aria potenziali che verrebbero a crearsi.
Il progetto dello stampo compreso le linee di separazione, le superfici di separazione, gli espulsori e carrelli messi progettati e posizionati al meglio, anche per tener conto della presenza di eventuali aree di venting, permetto di evitare anche sgradevoli incidenti come ad es. punti di bruciatura in una zona estetica della parte stampata.
Gli utenti avanzati hanno bisogno di risultati di analisi molto dettagliati, è quindi avere disponibili il massimo dell’informazione. Tuttavia, più il modello è complesso e più è il tempo e l’attenzione che deve essere posta nella creazione della mesh d’assieme, per garantire la continuità nelle funzioni di trasferimento di calore tra i vari componenti.
Nel processo di analisi e di simulazione, la fase di pre-processamento diMoldex3D consente agli utenti di importare il modello di geometria di uno stampo nella sua interezza, e costruire dettagliati elementi mesh per ogni componente dello stampo.
Con Moldex3D R 14.0, quindi ben due anni fa, s’inizia a supportare la simulazione continua della NMM Non Matching Mesh tra la parte e l'inserto della parte. Ciò consente agli utenti di risparmiare tempo e sforzi nell'abbinamento dei vari elementi costituenti la mesh nella superficie di contatto tra gli elementi. Moldex3D R 15.0 estende la capacità di simulazione NMM alla generazione di mesh solide tra la parte, l'inserto nella cavità e base stampo.
Nella versione più recente, Moldex3D R16, simulazione NMM comprende ulteriormente l'inserto stampo, così come i nuovi attributi piastra stampo, comprese piastre fisse e mobili stampo.
Attraverso la tecnologia NMM, la mesh solida d’assieme di un sistema stampo completo può essere generata automaticamente.
Un caso dell'utilizzazione della NMM nella simulazione del sistema completo dello stampo è indicato di seguito.
1. semplificare il modello completo dello stampo: i disegni dello stampo includono solitamente componenti molto piccoli, che hanno effetto insignificante nell'analisi e nella simulazione del comportamento generale dello stampo. Così, per ridurre gli elementi mesh e il tempo di analisi, gli utenti possono semplificare il modello rimuovendo le viti o riempiendo prima i fori delle viti nei modelli CAD.
2. importare il modello semplificato in Moldex3D BLM Designer Advanced o STUDIO Advanced e impostare gli attributi: Cavità, Runners e Gates, canali di raffreddamento e gli inserti in cavità o dello stampo, il blocco stampo stesso, e utilizzare i nuovi attributi piastra stampo per impostare piastre fisse e mobili. Il sistema permette di mostrare o nascondere gli elementi con gli attributi impostati (fig. 1) per facilitare la visione d’assieme.
Fig. 1 le regolazioni degli attributi completi delle piaste componenti lo stampo e dello stampo nel suo insieme
3. I nodi della mesh: impostare i nodi dalla cavità, e poi inserire lo stampo. La nuova funzionalità di può portare automaticamente i dati del nodo della cavità o dell'inserto di stampo sui bordi adiacenti dell'inserto dello stampo e della piastra stampo. Questa funzione migliora l'efficienza di creazione dei nodi nello stampo completo con più componenti e riduce i gap di dimensione della densità dei nodi tra i componenti adiacenti (fig. 2).

4. I dati di creazione dei nodi saranno portati all'analisi dell'ordine successivo
costruire mesh solide: fare clic sul pulsante per la generazione di mesh solide, e la mesh solida del modello di stampo completo verrà generato automaticamente.
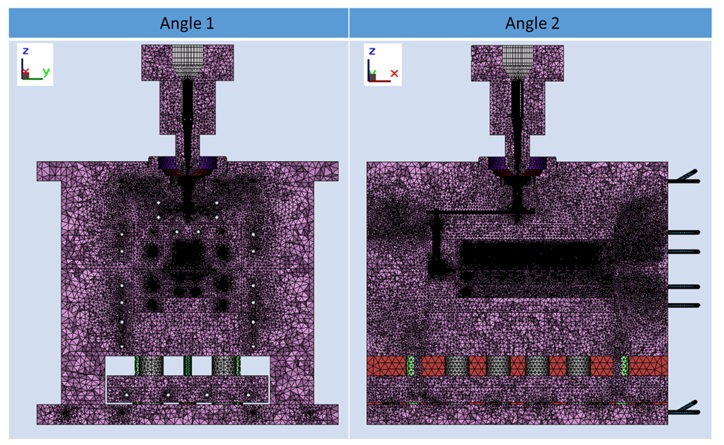
Fig. 3 la sezione a maglie solide del modello di stampo completo
5. esportare il file MFE: il software controllerà automaticamente il modello di mesh prima di salvarlo nel file. Quando il valore all'intersezione è troppo grande, si può agire manualmente per evitare problemi di analisi (fig. 4).
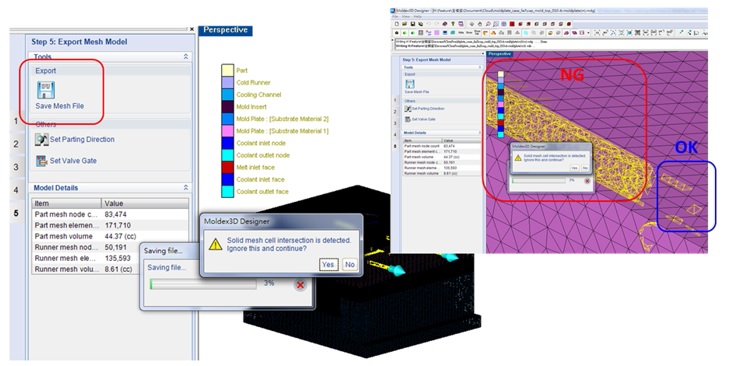
Fig. 4 controllo di intersezione delle celle prima dell'esportazione della mesh
6. analisi di riempimento dello stampo: il materiale della parte in questo caso è Policarbonato ed il materiale della piastra dello stampo è M315 supplementare. La temperatura predefinita del fuso e la temperatura dello stampo sono rispettivamente 290 ° c e 105 ° c. Osservando la temperatura dello stampo, delle piastre fisse e mobili possiamo trovare la buona continuità di temperatura del modello NMM della maglia. Il calore può essere erogato con continuità tra diverse piastre di stampo (fig. 5).
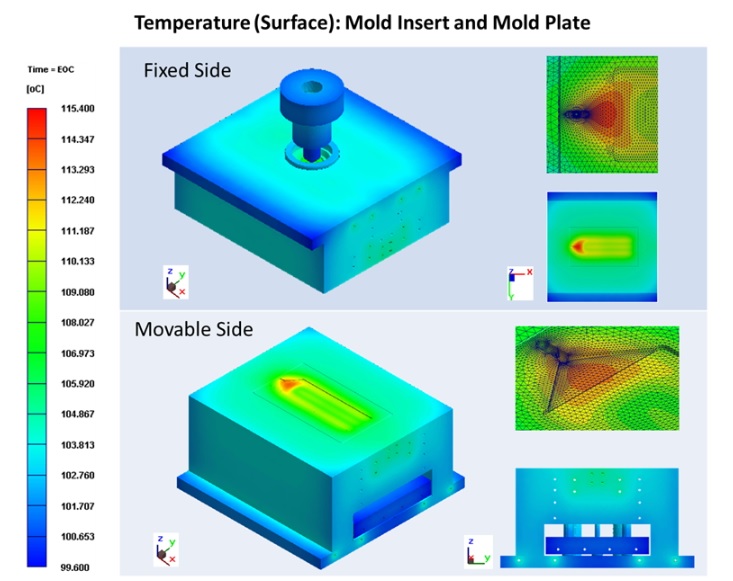
Fig. 5 la distribuzione della temperatura degli inserti e delle piastre stampo
L'analisi completa dello stampo in Moldex3D R16, per mezzo della nuova funzione “Attribute Plate” dello stampo consente agli utenti di impostare gli attributi di piastre fisse e mobili, e la tecnologia avanzata NMM facilita una rapida generazione solida mesh del sistema stampo nella sua completezza.
I risultati dell'analisi dello stampo forniscono ai clienti i dati di simulazione più importanti e significativi per una corretta progettazione dello stampo. In questo modo, l’operatore è in grado di ridurre i tempi di prova stampo, e, in modo efficiente, accelerare lo sviluppo dello stampo stesso, e migliorare la qualità del prodotto finale.
MDXITA – prt2018_029- Giorgio Nava