Nuovo metodo CAE in due passaggi per materiali in fogli nello stampaggio a compressione
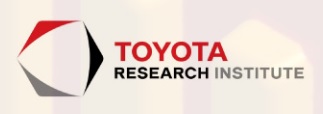
Il Toyota Research Institute, Nord America (TRINA), fondato nel 2008. TRINA opera come unità di ricerca e sviluppo a 360°, dalle vernici di ispirazione biologica alla tecnologia di raffreddamento, dall’elettronica per veicoli ibridi alla batterie di nuova generazione a base di magnesio dalle auto che si guidano da sole ai nuovi materiali. Le innovazioni introdotte da TRINA mostrano che questa realtà di ricerca avanzatissima, non sta solo tenendo il passo nell’evoluzione del veicolo, ma aiuta a stabilire il ritmo del futuro.
Sintesi
Poiché non esiste un software commerciale pratico disponibile per gestire lo stampaggio a compressione dei materiali in fogli (Sheet Molding Compression), il team di Toyota Research Institute of North America (TRINA) mirava a sviluppare un nuovo metodo di progettazione per l'analisi del riempimento degli stampi e per l'analisi della deformazione del composito CFRP a base di fibre lunghe discontinue in formato foglio/tessuto.
In questo progetto, è stato sviluppato un nuovo metodo CAE in due fasi per simulare lo stampaggio a compressione di materiali in fogli. Il metodo in due fasi ha combinato l'uso di LS-DYNA e Moldex3D per soddisfare la necessità di catturare il comportamento strutturale elastico-plastico durante il drappeggio e il comportamento del flusso della resina nel fondersi durante la compressione, consentendo a TRINA di prevedere al meglio l'orientamento e l'ordito delle fibre.
Le sfide
•Non esisteva un pratico software commerciale in grado di gestire lo stampaggio a compressione dei materiali in fogli realizzati con fibre non tessute
•Nessuno dei software di stampaggio meccanico o di compressione strutturale standard era in grado di gestire il drappeggio del foglio
Soluzioni
La simulazione dello stampaggio a compressione è stata effettuata utilizzando l'approccio proposto in due fasi. Innanzitutto, i materiali in fogli sono stati simulati come un processo di drappeggio usando LS-DYNA. Successivamente, la forma drappeggiata è stata utilizzata nella simulazione dello stampaggio a compressione con Moldex3D.
Benefici
•Consentire ai produttori di simulare drappeggi e stampaggio a compressione di materiali in fogli con un metodo CAE in due fasi, che in precedenza non era disponibile
•Ottenere un'accurata previsione dell'orientamento della fibra delle parti in CFRP
•Ottenere uno sviluppo del prodotto accelerato e una riduzione consistente dei costi
Argomento di studio
In questo caso, il ricercatore del Toyota Research Institute of North America (TRINA) era interessato ai materiali termoplastici con fibra di carbonio sotto forma di composto per stampaggio di fogli (SMC) per fabbricare una parte.
La carica del foglio era costituita da fibra lunga discontinua in formato foglio. Il ricercatore di TRINA ha preferito caricare i fogli sulla base di una migliore possibilità di mantenere una struttura iniziale a fibra lunga dopo il completamento del processo di stampaggio a compressione. Questo processo è seguito da quattro passaggi, come mostrato nella Figura 1:
Passaggio 1: il pannello PA6 con il 35% della carica di fibra di carbonio del foglio è stato riscaldato fino alla temperatura di fusione.
Passaggio 2: il materiale in foglio riscaldato è stato coperto nella cavità con una bassa pressione, fase chiamata di drappeggio.
Passaggio 3: comprimere il foglio nella cavità e “bucare” ad alta pressione fino alla solidificazione.
Passaggio 4: la parte solidificata è stata espulsa dallo stampo e raffreddata a cielo aperto.
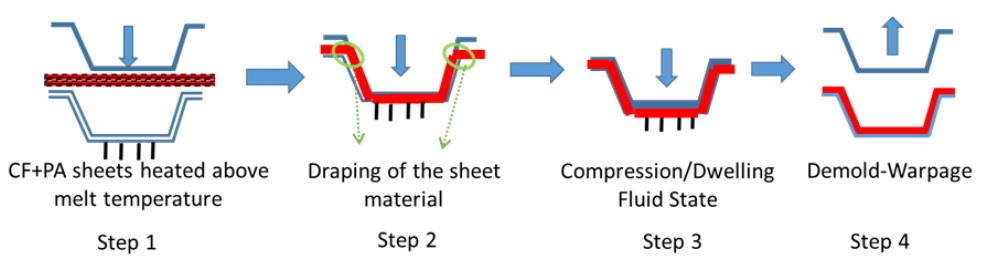
Fig. 1 Processo di stampaggio a compressione mediante carica del foglio
Il processo di stampaggio a compressione del materiale in fogli di solito prevede il processo di drappeggio e compressione. Il drappeggio subisce comportamenti strutturali elastico-plastici e il processo di compressione risente dei comportamenti di flusso.
Integrare i due comportamenti nella simulazione può essere una grande sfida.
Moldex3D consente agli utenti la libertà di integrarsi con altri software di simulazione strutturale per simulare in modo completo i due comportamenti (FEA Interface).
La simulazione dello stampaggio a compressione del materiale in fogli comprende due passaggi, come mostrato nella Figura 2. Nel primo passaggio, l'analisi del drappeggio viene eseguita utilizzando l'analisi esplicita agli elementi finiti (LS-DYNA). Nella seconda fase, l'analisi del riempimento e della deformazione viene eseguita utilizzando il modulo di stampaggio a compressione Moldex3D.
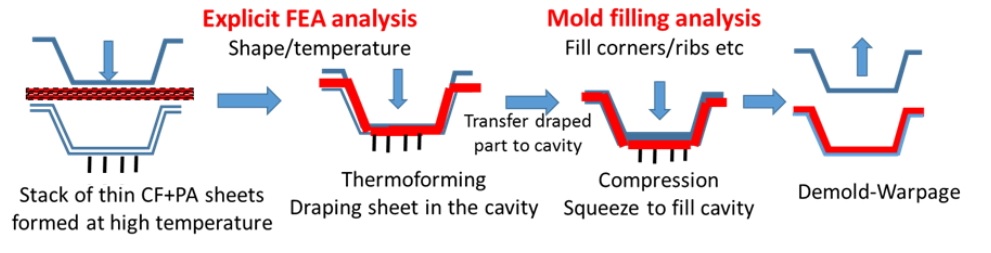
Fig. 2 L'approccio di simulazione utilizzato per il materiale in foglio nello stampaggio a compressione (SMC).
Sulla base delle esigenze di componenti leggeri per l'industria automobilistica, i ricercatori di TRINA hanno progettato la parte a tre cavità (Fig. 3). Le proprietà del materiale misurato importate in Moldex3D sono mostrate in Fig. 4.
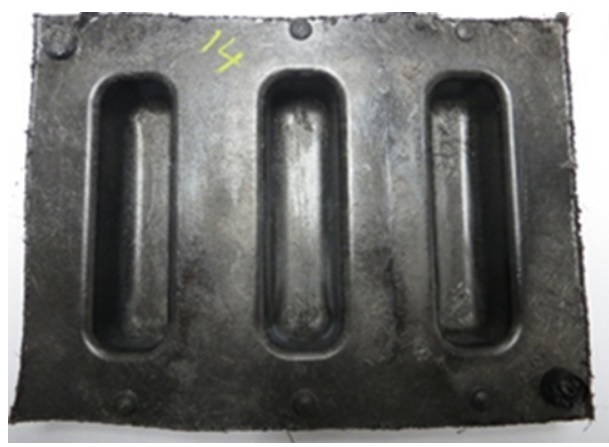
Fig. 3 Il pezzo prodotto
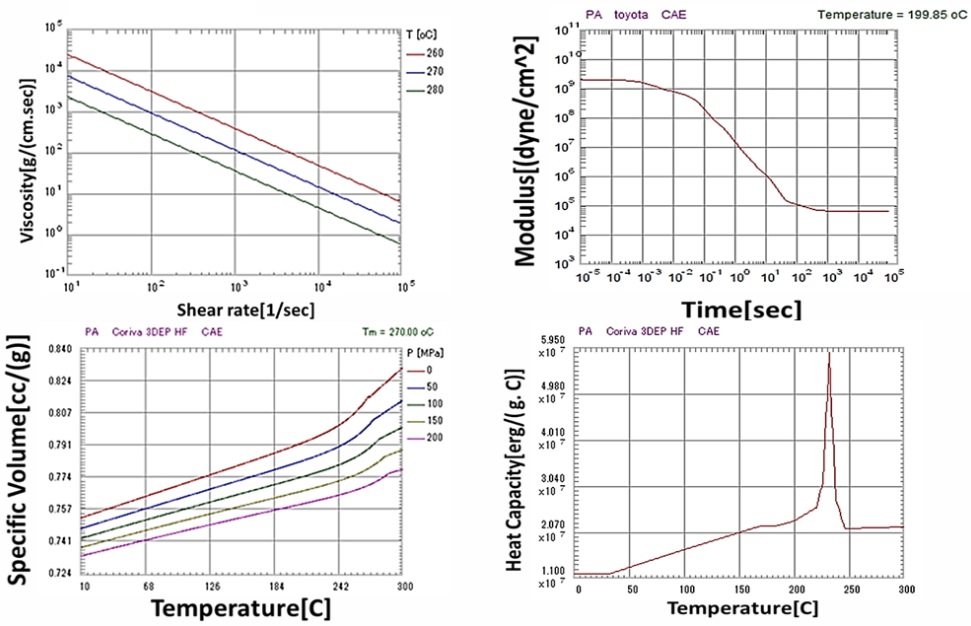
Fig. 4 Le proprietà del materiale misurato importate nel formato Moldex3D.
I ricercatori di TRINA hanno condotto gli esperimenti per convalidare i risultati della simulazione dell’integrazione di deformazione e orientamento delle fibre.
In LS-DYNA, la distanza di drappeggio si ferma al 60%, 80% e 100% della zona di compressione, e queste condizioni al contorno sono state usate come prepreg per Moldex3D.
I risultati della simulazione mostrano che quando la distanza di drappeggio si ferma all'80%, si ottengono buoni risultati confrontati con i dati sperimentali (Fig. 5), quindi la successiva analisi verrà condotta secondo questa metodologia.
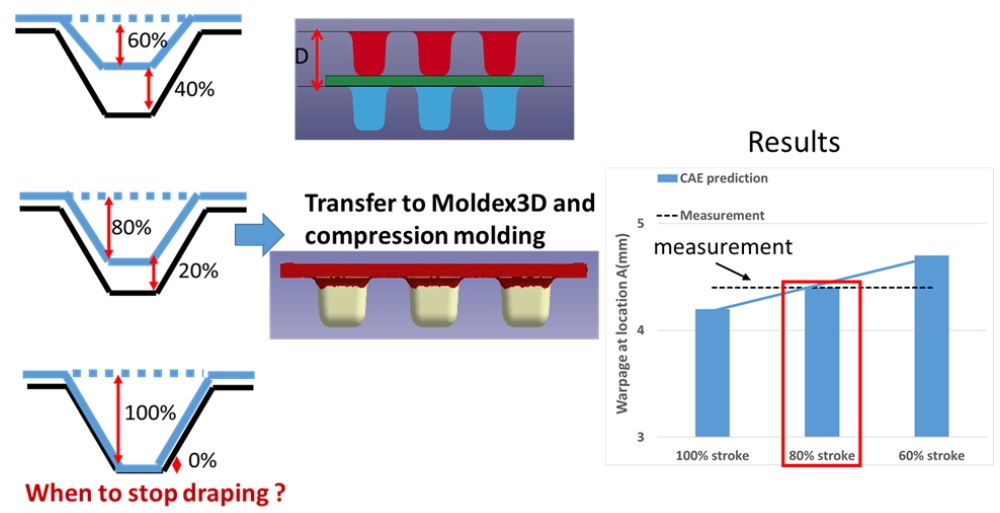
Fig. 5 Convalida degli effetti della distanza della corsa.
Il confronto dei risultati della deformazione è mostrato in Fig. 6. La deformazione è misurata nella posizione (A) nel modello di simulazione e nell'esperimento. La deformazione basata su diverse temperature dello stampo è prevista inferiore ad un 8% dell'errore. Inoltre, l'aumento della temperatura dello stampo porta all'aumento della deformazione osservata sia dall'esperimento fisico sia da Moldex3D.
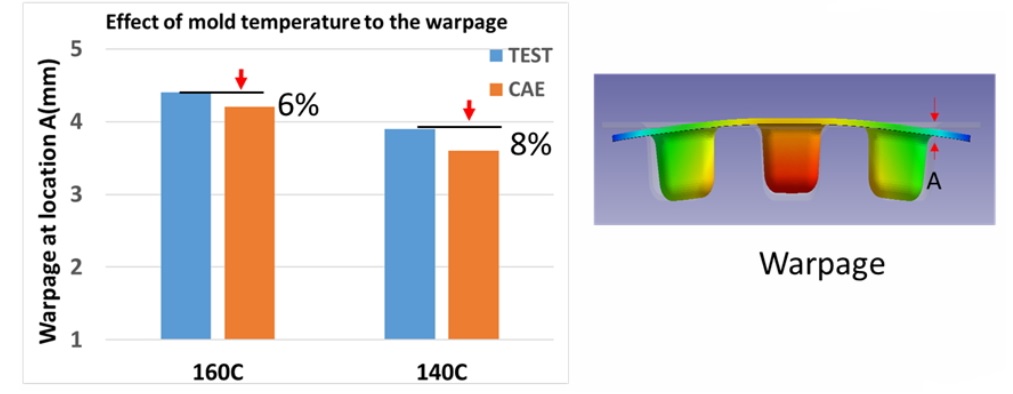
Fig. 6 Convalida dei risultati della deformazione
Per convalidare l'effetto dovuto all’orientamento della fibra sia in fase di esperimento e sia dalla simulazione, il team di TRINA ha scelto le posizioni di A, B e C per l’attività di validazione, come mostrato nella Figura 7 (a). L'orientamento sperimentale delle fibre nelle posizioni sopra misurate attraverso la tomografia computerizzata e il metodo di analisi della grafica del volume.
I risultati del confronto per CAE e misurati da esperimenti nello spessore normalizzato mostrato in Fig. 7 (b), (c), (d). Complessivamente, i dati previsti da Moldex3D erano entro il 15% del criterio di precisione.
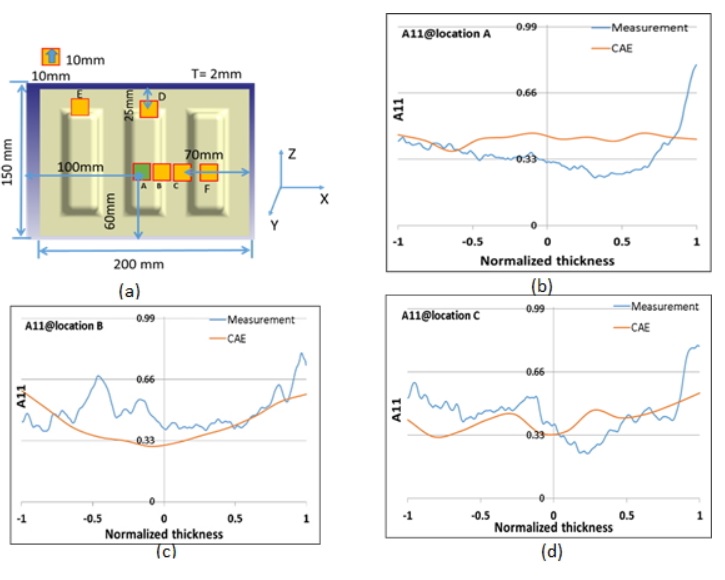
Fig. 7 Convalida degli orientamenti delle fibre.
Risultati
Attraverso le capacità di integrazione di Moldex3D con altri software strutturali, TRINA è stata in grado di utilizzare questa nuova metodologia in due fasi per simulare il processo di stampaggio a compressione di fogli discontinui a fibra lunga.
TRINA è stata in grado anche ottenere il risultato di previsione concordato con una piccola discrepanza di errore che rientrava nei parametri di progettp. TRINA ora può raggiungere / aumentare la produzione di compositi leggeri con prodotti ad alta resistenza per l'industria automobilistica.
Moldex3D Italia – Giorgio Nava – prt_2020_070