Risultati di simulazione accurati sulla tecnologia MuCell® consentono l'adozione della soluzione Moldex3D
- • Cliente: Proplast
- • Paese: Italia
- • Industria: ricerca e istruzione
- • Soluzione: Moldex3D BLM Advanced
Proplast è stata fondata ad Alessandria (Italia) nel 1998 con l'obiettivo di supportare le imprese nel settore delle materie plastiche con particolare attenzione alla ricerca applicata, all'innovazione tecnologica, al reclutamento di talenti dell'industria e alla formazione delle risorse umane.
Nel maggio 2008, Proplast ha aperto i suoi nuovi locali di 3500 mq che hanno triplicato la quantità di spazio dedicato ai servizi tecnici per le imprese del settore delle materie plastiche.
Proplast ha iniziato le sue attività con il supporto di quattro membri fondatori (Bayer, Basell, Guala e Mossi & Ghisolfi), ed è cresciuta enormemente con il supporto significativo di altre società, associazioni e universiti coinvolti nel corso dell'intera catena della plastica nel corso degli anni.
Moldex3D ITALIA è partner di Proplast (www.proplast.it)
Questo progetto è stato sviluppato da Proplast in collaborazione con Moldex3D ITALIA, Engel Italia, Trexel e Onni-stamp.
Sintesi
L'obiettivo di Proplast in questo progetto era quello di supportare i propri clienti in ogni fase dell'implementazione della tecnologia MuCell®.
Il supporto è andato dalla progettazione delle parti e dalla progettazione degli stampi alle prove di stampaggio e alla sperimentazione di stampi con processo MuCell®.
Essendo questo un processo complesso da affrontare, Proplast ha fatto ricorso all'aiuto della soluzione Moldex3D per la tecnologia MuCell® per aiutare gli ingegneri a navigare attraverso l'intero processo, ottimizzare la progettazione di parti e stampi e completare con successo il progetto ottenendo risultati positivi alla fine.
Le sfide
La più grande sfida in questo caso di studio è stata quella di prevedere con precisione l’effetto MuCell® e ottimizzare di conseguenza.
In questo caso, sono state identificate quattro aree particolari per studiare ulteriormente gli effetti della tecnologia MuCell®:
- • Risucchi (sinkmarks)
- • Deformazione
- • Predizione e convalida delle dimensioni delle celle
- • Predizione e convalida della densità delle cellule
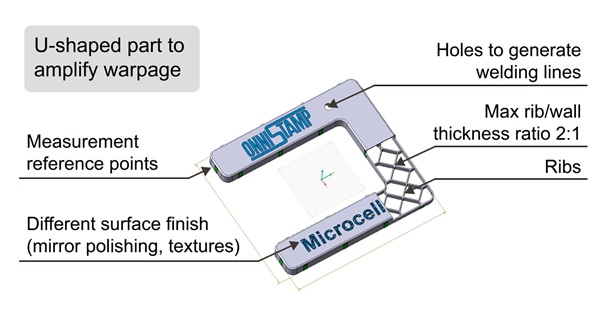
Ogni fase del processo è stata supportata utilizzando il software di simulazione Moldex3D.
Funzioni specifiche sono state aggiunte alla progettazione della parte per aiutare ulteriormente a valutare, misurare e confrontare i risultati.
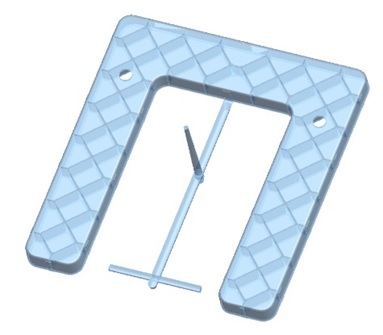
Il modello utilizzato
Soluzioni
Le funzionalità di simulazione Moldex3D offrono l'opportunità di simulare sia lo stampaggio convenzionale sia lo stampaggio a iniezione MuCell®.
Basandosi sulle simulazioni software, Proplast è stato in grado di confrontare i risultati di ciascun processo e comprendere meglio le differenze operative tra i due.
Inoltre, l'obiettivo di Proplast di condurre un'analisi approfondita sul processo di stampaggio MuCell®, inclusa la dimensione cellulare, la distanza e densità cellulare e la distribuzione cellulare, è stato soddisfatto attraverso l'uso della tecnologia di simulazione Moldex3D.
Benefici
Moldex3D ha fornito un'analisi completa di simulazione su ogni aspetto del processo MuCell®. Con i dati della simulazione Moldex3D, Proplast è stata in grado di acquisire informazioni sul processo MuCell®, ottimizzare la progettazione di parti e stampi e, soprattutto, offrire raccomandazioni costruttive per guidare i loro clienti in tutta l'implementazione MuCell®.
La simulazione MuCell® di Moldex3D include analisi su:
- • Impostazioni di processo
- • Tempo di ciclo
- • Pressione
- • Forza di serraggio
- • Espansione / riduzione del peso • Contrassegni volumetrici di ritiro / affondamento
- • Warpage / distribuzione residua dello stress
- • Dimensione della cella locale
- • Distribuzione e densità cellulare
Argomento di studio
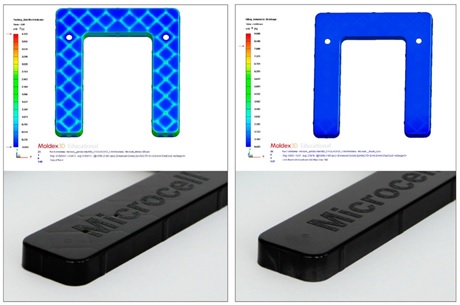
La simulazione di stampaggio a iniezione Virtual MuCell® è di grande aiuto nell'intero processo per prevedere la tecnologia MuCell® al fine di comprendere i reali benefici che la tecnologia MuCell® può offrire.
La simulazione Moldex3D ha consentito l'accesso ad una serie di aspetti importanti della tecnologia MuCell®:
1. Segni di risucchio:
Nello stampaggio ad iniezione standard (a sinistra) i segni nella zona di dissipazione sono molto visibili rispetto a MuCell® (a destra) dove non si rilevano segni di risucchio
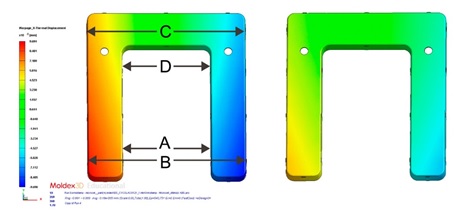
I risultati sperimentali dello stampo hanno confermato quello che la simulazione mostrava con una grande accuratezza della predizione dei segni di risucchio, sia sul processo compatto che su MuCell®. Inoltre, da questo esempio, si dimostra chiaramente che la tecnologia MuCell® è molto efficace.
2. Deformazione:
Nello stampaggio ad iniezione standard (a sinistra) la deformazione è più consistente rispetto aal processo MuCell® (a destra).
Moldex3D ha previsto con successo l'effetto d'angolo sia per la parte standard compatta che per la parte MuCell® e allo stesso tempo ha aiutato a visualizzare il miglioramento della deformazione usando MuCell®.
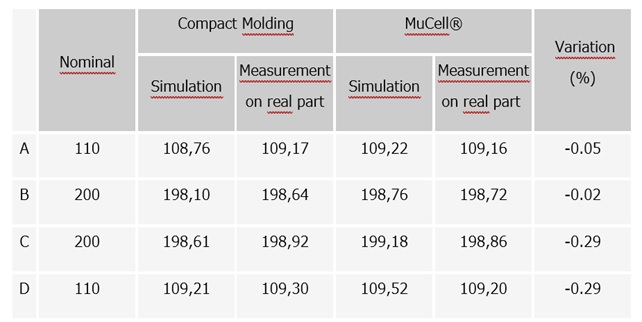
Sia i risultati della simulazione che le misurazioni delle parti reali hanno mostrato un notevole miglioramento sulla deformazione utilizzando MuCell®
3. Predizione e convalida delle dimensioni delle celle:
La predizione della dimensione cellulare è fondamentale per il processo MuCell®, poiché la qualità della parte e la resistenza meccanica dipendono dalla distribuzione uniforme delle cellule e dalle dimensioni adeguate delle cellule.
La loro corretta previsione lungo la parte è essenziale per correggere il disegno prima della produzione.
In questo caso di studio, la validadiza si è concentrata su tre posizioni (come mostrato nelle seguenti figure):
1. Regione di gating,
2. Regione di flusso medio,
3. Regione di fine flusso,
per osservare la crescita cellulare insieme alla lunghezza di percorso del flusso e per convalidare l'affidabilità del software sulla previsione della dimensione della cella.
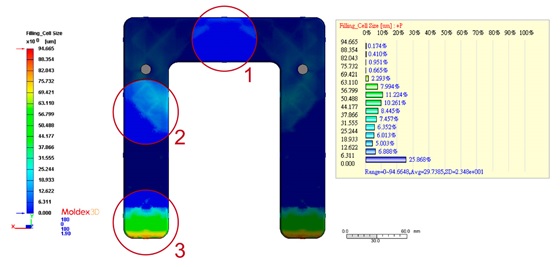
Posizione 1- Regione di gating: le celle rimangono di piccole dimensioni a causa dell'alta pressione vicino alla posizione del gate. Il risultato della simulazione ha fornito una buona previsione della dimensione della cella, convalidata dal SEM.
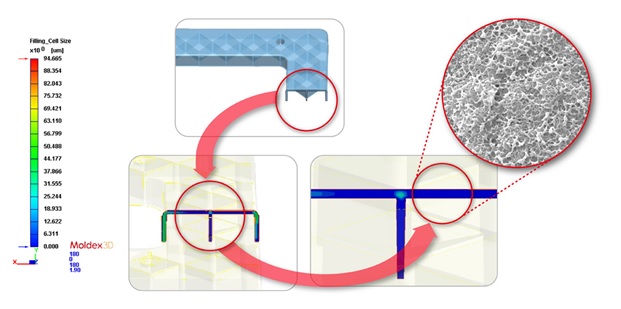
Posizione 2-Regione del flusso medio: le cellule crescono man mano che si allontanano dal gate; sia la simulazione che il SEM hanno rivelato la stessa tendenza. Le cellule sulla pelle superficiale hanno meno tempo per crescere rispetto al nucleo della parte, quindi la dimensione è più piccola.
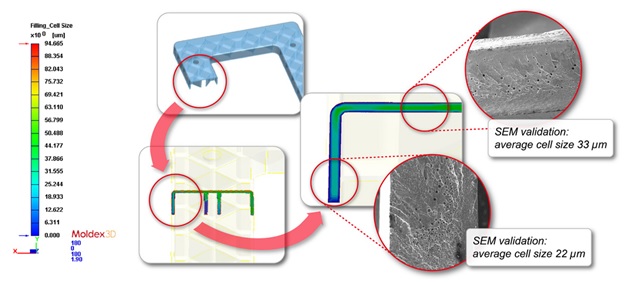
Posizione 3- Fine della regione di flusso: alla fine dell'area di flusso, il materiale ha percorso l'intero tratto che consente alla cellula di crescere; inoltre, la pressione sul fronte del flusso è bassa e non impone alcun vincolo alla crescita delle bolle.
Si osserva sia durante la simulazione, sia nella convalida SEM, che si formano cellule di grandi dimensioni.
Inoltre, le dimensioni delle celle possono variare in diverse parti di questa regione.
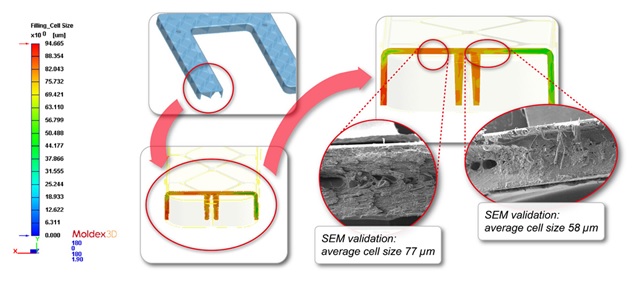
4. Predizione e convalida della densità delle cellule:
Oltre alla dimensione della cella, la densità cellulare è di grande importanza per il processo MuCell®.
La densità cellulare e la dimensione della cella sono in competizione, quando la dimensione media delle cellule cresce lungo la lunghezza del flusso, occupa un'area più grande e inevitabilmente la densità della cellula scende lungo il percorso.
Qui, i risultati della simulazione e SEM sono mostrati per il confronto (come mostrato anche nelle immagini seguenti).
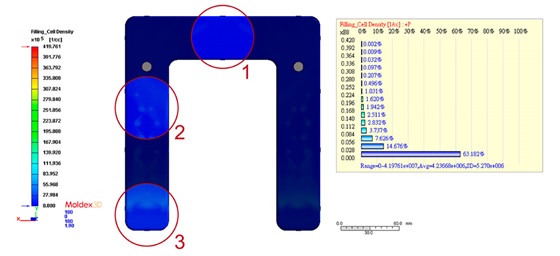
Posizione 1- Regione di gating: la densità è più difficile da misurare in SEM.
Confrontando i risultati della simulazione e SEM, gli utenti sono in grado di comprendere la rilevanza tra l'analisi e la parte sperimentale nel calcolo della densità.
Nell’intorno dell’area del gate, quando la pressione è superiore alla pressione di saturazione, la bolla non si forma.
Mentre la bolla inizia a crescere in quest'area, l'alta pressione limita le dimensioni delle cellule e consente la formazione di ogni singola bolla (nucleazione cellulare) senza unirle in un'unica grande bolla.
Qui, la simulazione e SEM mostrano gli stessi risultati in questo scenario.
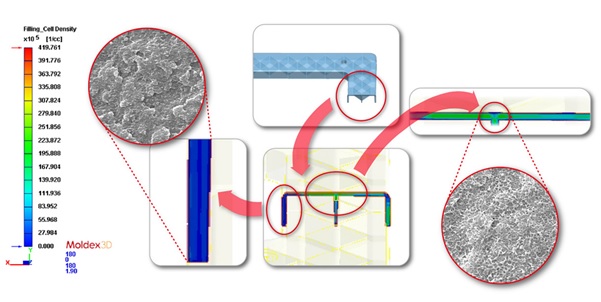
Posizione 2 - Zona di flusso medio: man mano che il flusso avanza lungo il percorso, le cellule crescono. Quando diventano più grandi, un dato spazio contiene meno cellule, con conseguente riduzione della densità cellulare.
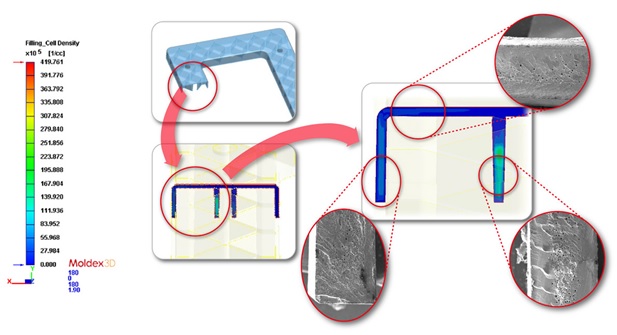
Posizione 3- Fine della regione di flusso: alla fine dell'area di flusso, le bolle sono molto sviluppate e unite insieme, risultando in una densità molto bassa con solo poche cellule visualizzate da SEM
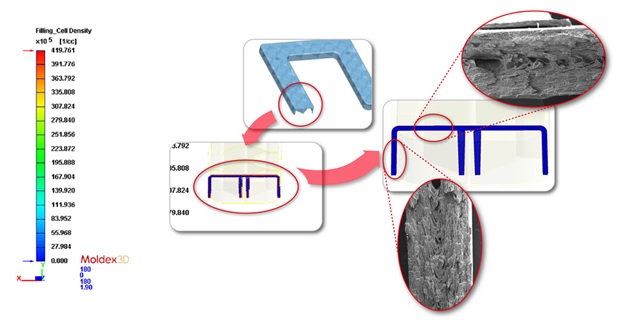
Risultati
In sintesi, attraverso questo caso di studio, potremmo riconoscere che:
• La tecnologia MuCell® è ideale per le parti che richiedono un segno di dispersione ridotto al minimo.
Anche quando il disegno del pezzo non è convenzionalmente ottimale (regioni con spessori elevati lontani dal gate, rapporto nervatura / parete alto), i segni del dissipatore possono essere eliminati.
• La tecnologia MuCell® è in grado di migliorare significativamente le deformazioni in generale.
• In teoria, il miglioramento della qualità è influenzato dalla crescita cellulare lungo la parte, che dipende da diversi fattori, ad esempio la lunghezza di percorso del flusso e lo spessore medio.
In questo caso di studio vediamo chiaramente la crescita delle cellule rispetto a questo fattore.
Soprattutto, tutti questi punti chiave sopra menzionati sono in grado di essere simulati con precisione e predetti dalla simulazione MuCell® di Moldex3D.
Con l'aiuto di Moldex3D, Proplast era in grado di investigare completamente nel processo MuCell® per identificare i principali vantaggi e ha aiutato con successo i propri clienti nell'implementazione della tecnologia MuCell® per ottenere una qualità superficiale ottimale.
Il valore della simulazione CAE
"La metodologia applicata all'analisi CAE con Moldex3D, che è stata sviluppata e valutata in Proplast, simula in modo accurato e affidabile il processo di stampaggio a iniezione microcellulare MuCell®, la qualità e la morfologia dell'espansione cellulare.
La simulazione del flusso dei componenti MuCell® eseguita con Moldex3D fornisce parametri di processo ottimizzati e qualità globale dello stampaggio (possibile riduzione del peso, contrazione volumetrica, caduta di pressione. risucchi e distorsione/deformazione) e descrizione microstrutturale locale della struttura cellulare (dimensione, densità e distribuzione delle cellule).
Una buona coerenza predittiva è stata osservata per quanto riguarda lo studio qui menzionato e i parametri di processo, l'espansione MuCell®, la capacità di riduzione del peso e la deformazione, "ha affermato Andrea Romeo, Responsabile CAE di Proplast.
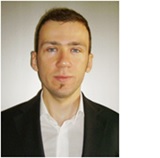
La simulazione del flusso dei componenti MuCell® eseguita con Moldex3D fornisce parametri di processo ottimizzati e qualità di stampaggio globale, nonché una descrizione microstrutturale locale della struttura cellulare.
MDXITA – prt2019_0038- Giorgio Nava