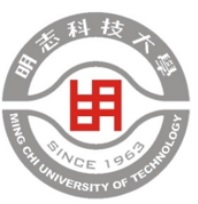
Azienda: Università tecnologica di Ming Chi
Paese: Taiwan
Settore: Educational / Academy
Soluzioni: pacchetto avanzato Moldex3D BLM: Flow, Pack, Cool, Warp
L'Università della Tecnologia di Ming Chi era originariamente chiamata "Ming Chi Institute of Technology". Più di 200 anni fa, la "Ming Chi Academy", fondata da un grande studioso, il signor Hu Cho-Yu nel sud di Fukien, si trovava nelle vicinanze dell'Università.
A quel tempo l'Accademia era la base di un centro intellettuale e culturale del nord di Taiwan.
Questa università è stata nominata "Ming Chi" con l'obiettivo di incoraggiare la facoltà e gli studenti a imparare dagli “anziani” virtuosi e ad abbracciare l'eredità e la visione condividendone la missione.
(Fonte: https://www.mcut.edu.tw/)
Introduzione alla problematica
Nel mondo manifatturiero odierno, il tempo è denaro.
Ciò è particolarmente vero nel settore dello stampaggio ad iniezione, in cui una riduzione dei tempi di raffreddamento può contribuire a ottenere risparmi significativi.
Pertanto, l'importanza del sistema di raffreddamento è indiscutibile.
In questo progetto, la Ming Chi University of Technology (MCUT) ha utilizzato Moldex3D per ottimizzare la progettazione del layout del sistema di raffreddamento conformato, che potrebbe migliorare il tempo di raffreddamento, ridurre i differenziali di temperatura e la deformazione delle parti.
I risultati sperimentali hanno anche dimostrato che i canali di raffreddamento conformati, progettati in modo appropriato, potrebbero fornire un migliore effetto di raffreddamento rispetto ai canali di raffreddamento convenzionali, riducendo il tempo di raffreddamento anche del 70%.
Le sfide
Argomento di studio
Durante l'intero processo di stampaggio a iniezione, il tempo di raffreddamento di solito rappresenta circa il 70% del tempo di ciclo. Aumentare la produttività riducendo i tempi di raffreddamento, garantendo nel contempo la qualità del prodotto, è quantomeno difficile da ottenere utilizzando i canali di raffreddamento tradizionali.
Gli studenti MCUT hanno deciso di affrontare il problema incorporando la tecnologia di raffreddamento conformato.
In questo caso, l'obiettivo era determinare il tempo di raffreddamento ottimale attraverso la simulazione con Moldex3D e convalidare i risultati attraverso esperimenti pratici.
Sono stati anche studiati i modi per ridurre il tempo di ciclo, i differenziali di temperatura e lo spostamento/deformazione.
La parte di questo progetto è una tazza 60x30x60 mm con uno spessore della parete di 2mm.
Era fatto di cera che veniva iniettata direttamente attraverso un cancello a spillo da 2 mm senza passare attraverso un sistema di canali.
La mesh è stata realizzata in Moldex3D posizionando nodi di sensori installati sulla parte per controllare la temperatura e il tempo di raffreddamento.
È stata inizialmente confrontata una serie di 45 varianti di canali di raffreddamento conformi e successivamente è stato confrontato il canale di raffreddamento conforme ottimale con il canale di raffreddamento convenzionale, oltre a nessun sistema di canali di raffreddamento (Fig. 1).
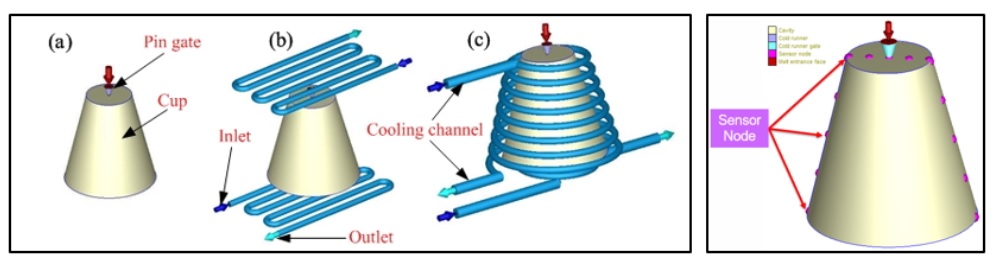
Fig. 1 Sinistra: modello CAD (a) senza canali di raffreddamento, (b) con canali di raffreddamento convenzionali e (c) con canali di raffreddamento conformi
A destra: installazione del nodo sensore
Nella prima valutazione, il raffreddamento conformato ottimale è stato in grado di raggiungere il tempo di raffreddamento più breve a 92,73 s (Fig. 2).
Il design aveva il diametro più piccolo (4 mm), la distanza minima del passo (6 mm) e la distanza più breve tra la linea centrale del canale e la superficie della parte (8 mm).
Questo design ha portato un canale di raffreddamento più lungo e alla maggiore superficie del canale che alla fine ha reso il processo di raffreddamento più efficiente ed efficace.
Inoltre, le analisi hanno dimostrato che aumentare il passo o la distanza verso la superficie della parte comportava un tempo di raffreddamento più lungo.
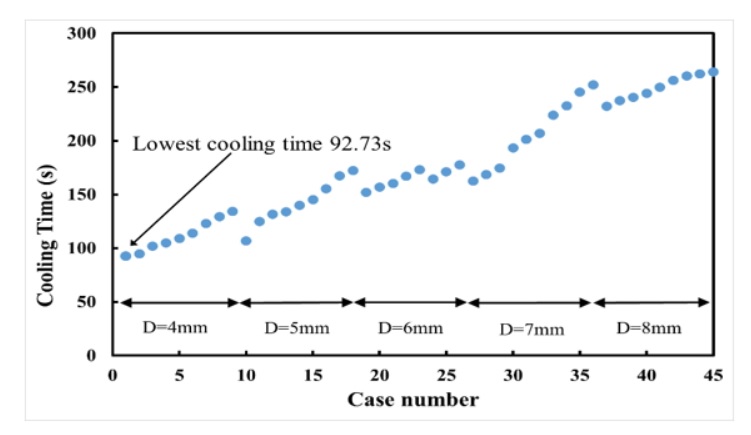
Fig. 2 Tempo di raffreddamento del canale di raffreddamento conforme
Nella seconda valutazione, il risultato ha mostrato che il canale di raffreddamento conformato ha fornito un controllo termico molto maggiore rispetto al canale di raffreddamento convenzionale e quello senza canale di raffreddamento e ha ridotto il tempo di raffreddamento rispettivamente del 70,03% e del 90,26% (Fig. 3).
Con questo progetto di raffreddamento conformato, la distribuzione della temperatura della tazza era più uniforme (Fig. 4).
Anche la differenza di temperatura dello stampo tra le pareti della cavità superiore e inferiore, che fornisce un contributo alla deformazione totale, è stata ridotta del 99,5% rispetto al design senza canali di raffreddamento (Fig. 5).
Questo progetto di raffreddamento conformato ha valori di deformazione ridotti e ha contribuito positivamente alla deformazione totale rispetto al sistema di raffreddamento convenzionale e nessun canale di raffreddamento del 24,05% e del 56,01%, rispettivamente (Fig. 6).
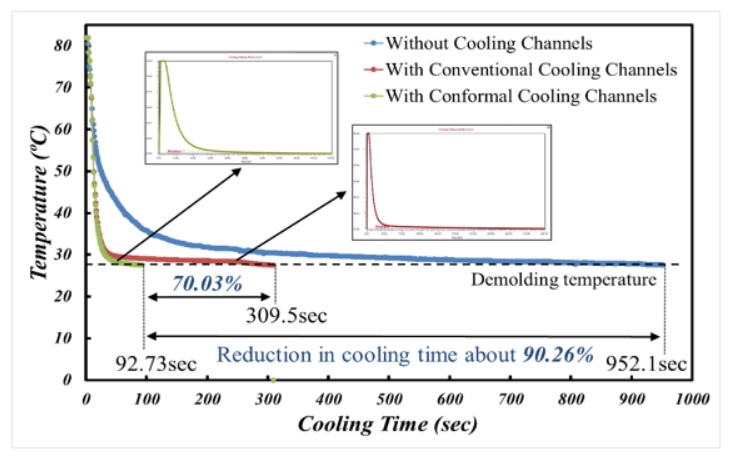
Fig. 3 Tempo di raffreddamento per raggiungere il confronto della temperatura di smagnetizzazione
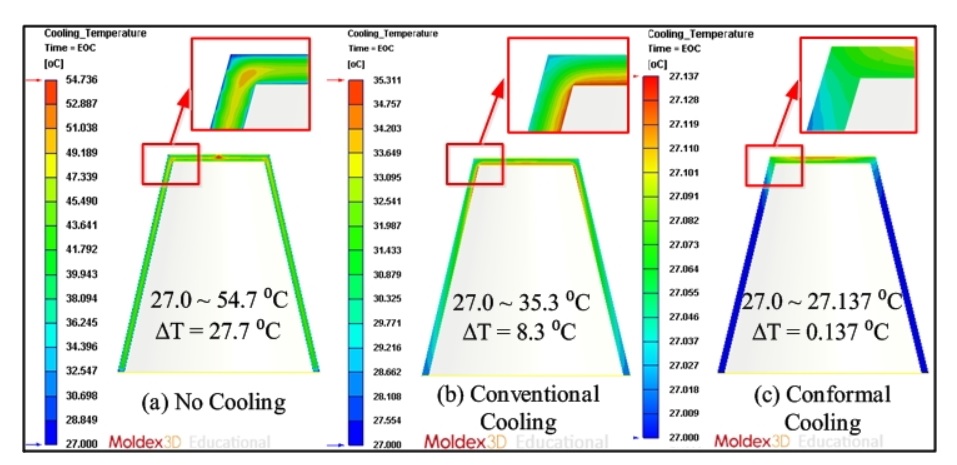
Fig. 4 Differenza di temperatura della parte all'interno della tazza (a) senza canali di raffreddamento, (b) con canali di raffreddamento
convenzionali e (c) con canali di raffreddamento conformi
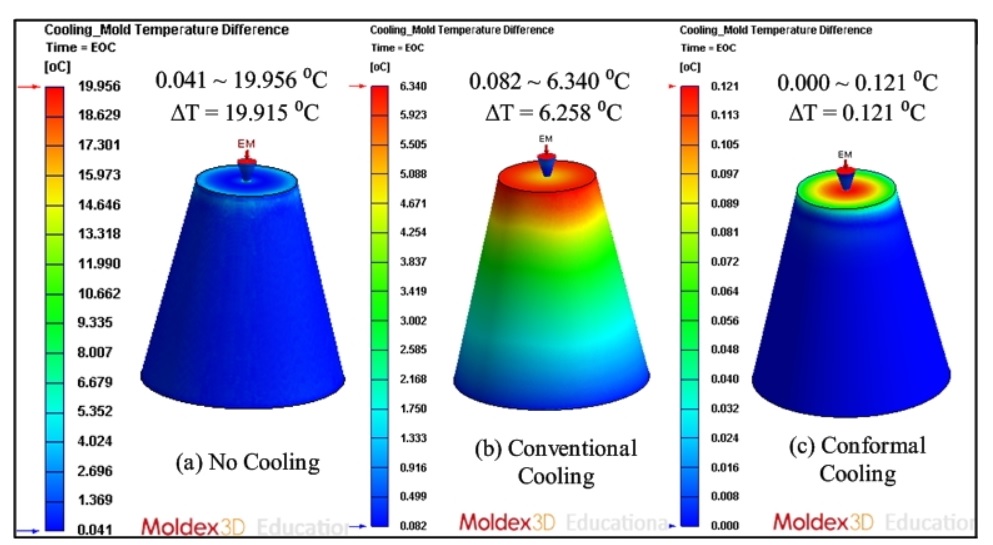
Fig.5 Differenza di temperatura dello stampo (a) senza canali di raffreddamento, (b) con canali di raffreddamento convenzionali e (c) con canali di raffreddamento conformi
Fig. 6 Confronto dello spostamento del prodotto su (a) spostamento X, (b) spostamento Y, (c) spostamento Z e (d) spostamento totale.
Al fine di verificare i risultati della simulazione, sono stati fabbricati stampi in resina epossidica riempiti di alluminio e sistemi di raffreddamento adeguati.
I canali di raffreddamento convenzionali erano fatti di cera K512, mentre i canali di raffreddamento conformi erano fatti di filamento di cera dopo ABS e PLA.
Nell'esperimento è stata utilizzata acqua come refrigerante.
I sensori di temperatura sono stati installati nello stampo durante il processo di iniezione per controllare la temperatura superficiale, la temperatura della parte e il tempo di raffreddamento.
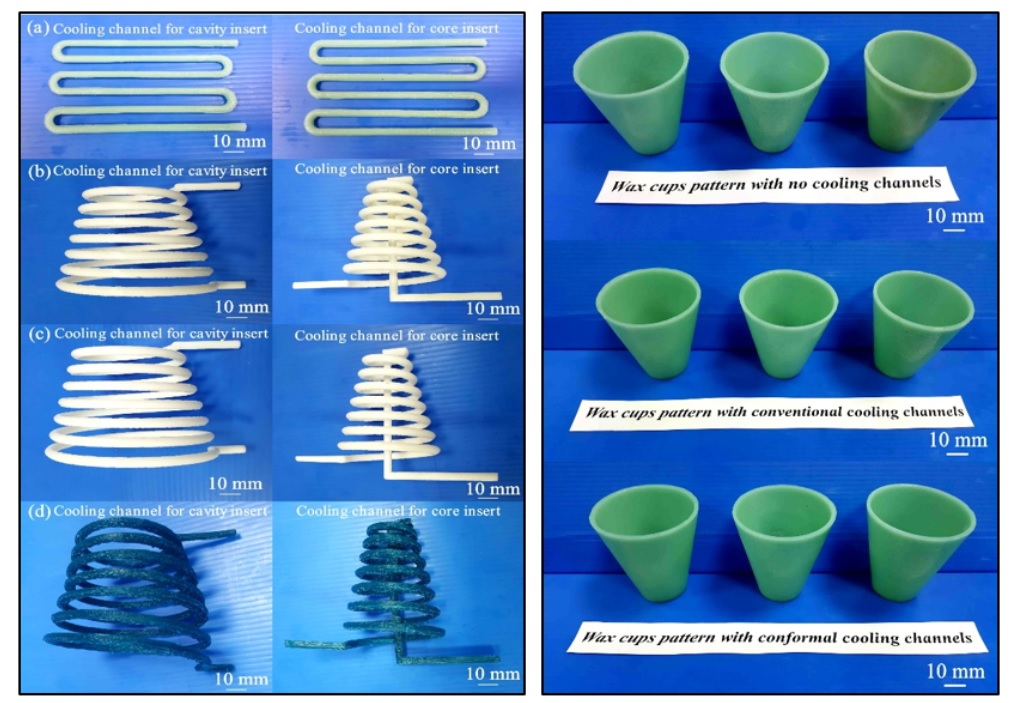
Fig. 7 Sinistra: (a) raffreddamento convenzionale Cera K512 con, (b) raffreddamento conforme ABS, (c) raffreddamento conforme PLA e (d) raffreddamento conforme filamento di cera
A destra: prodotto in cera fabbricato con stampi ad iniezione a bassa pressione
L'esperimento è stato condotto utilizzando la tecnologia di stampaggio ad iniezione di cera.
La macchina per iniezione a bassa pressione è stata utilizzata per iniettare la cera nello stampo.
La temperatura di fusione e la temperatura del refrigerante sono state impostate rispettivamente a 82 ° C e 27 ° C.
Il ciclo è stato ripetuto 10 volte per garantire la precisione.
Come mostrato in Fig.8, i risultati sperimentali sono in buon accordo con i risultati della simulazione di Moldex3D, che mostra che i canali di raffreddamento conformi possono migliorare l'effetto di raffreddamento e ridurre significativamente il tempo di raffreddamento del 69,61%.
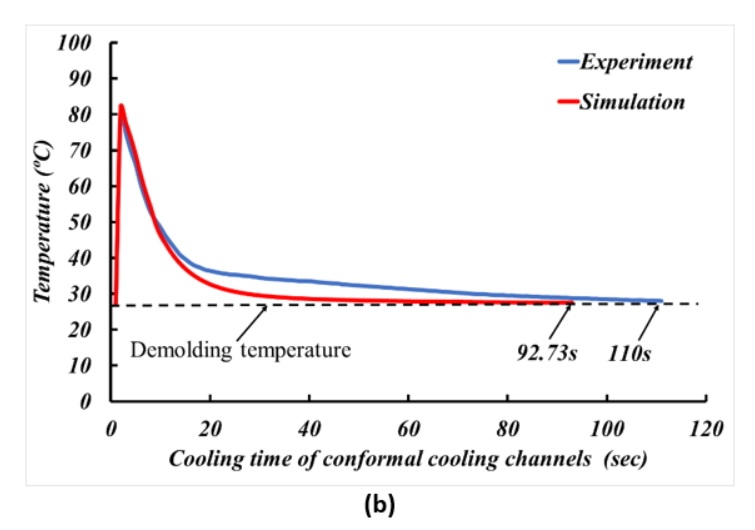
Fig. 8 Confronto tra esperimento e simulazione:
(a) Tempo di raffreddamento convenzionale, (b) Tempo di raffreddamento conformato
I Risultati
In conclusione, Moldex3D si è rivelato uno strumento utile per identificare il canale di raffreddamento conforme ottimale.
I risultati hanno indicato che i canali di raffreddamento conformi potrebbero effettivamente migliorare il tempo di raffreddamento, la differenza di temperatura e la deformazione delle parti.
I risultati sperimentali verificano anche che il canale di raffreddamento conforme possa fornire una migliore efficienza di raffreddamento rispetto a quello convenzionale.