Moldex3D aiuta DURA Automotive a risolvere la deformazione dell'incapsulamento dei finestrini di un veicolo
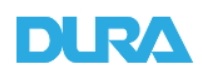
DURA Automotive Systems è un fornitore automobilistico globale specializzato nella progettazione, ingegneria e produzione di soluzioni che guidano l'evoluzione della mobilità. Con un'eredità che comprende oltre 100 anni di lavoro, l'azienda è riconosciuta dai principali produttori di veicoli come partner fornitore preferito di sistemi meccatronici innovativi, altamente integrati e soluzioni light weight.
(Fonte:
http://www.duraauto.com/)
Sommario
Il manufatto è un incapsulamento per finestrino d’auto con tre diversi inserti: vetro trasparente, canale di scorrimento in vetro (GRC) e piccolo inserto in alluminio.
La deformazione del GRC ha reso la parte incapace di soddisfare i requisiti di spazio e scarico, causando difficoltà nel processo di assemblaggio.
Gli ingegneri di DURA Automotive hanno utilizzato Moldex3D per identificare la causa principale della deformazione e hanno scoperto che la spessa parete in PVC a contatto con il GRC ha portato a questo errore funzionale.
Pertanto, hanno applicato un inserto in ABS per ridurre lo spessore nella regione, senza compromettere la rigidità della parte.
Di conseguenza, DURA è stata in grado di trovare, in modo efficace e funzionalmente valido, il progetto ottimizzato e ha deciso di modificare l’assieme in base ai risultati di Moldex3D al fine di ridurre la deformazione e risolvere il problema di assemblaggio.
Le sfide
• La deformazione causava un guasto del gruppo di scarico
• Risucchi e segni in superficie
• Rispetto dei tempi di raffreddamento richiesti
Soluzioni
DURA ha utilizzato Moldex3D per verificare la progettazione modificata di un canale di scorrimento in vetro per risolvere i problemi di deformazione, raffreddamento e segno di risucchio e difettosità in superficie.
Benefici
• Ottenuto un riempimento più equilibrato
• Deformazione migliorata, risolto il problema di assemblaggio e soddisfacevano i requisiti di gap e flush
• Riduzione dei risucchi e delle difettosità di superficie
• Riduzione del tempo di raffreddamento richiesto del 66%
• Riduzione delle prove di stampo e dei tempi di sviluppo
Argomento di studio
DURA ha dovuto soddisfare i requisiti di spazio di un incapsulamento per il finestrino auto. La parte è composta da diversi inserti tra cui vetro trasparente, canale di scorrimento in alluminio e piccolo inserto in alluminio.
Questi tre inserti sono sovrastampati con materiali in PVC (Fig. 1, 2).
Per soddisfare i requisiti di assemblaggio, DURA non ha potuto compromettere più di tanto lo spessore del canale vicino al vetro, sebbene sia la causa della deformazione.
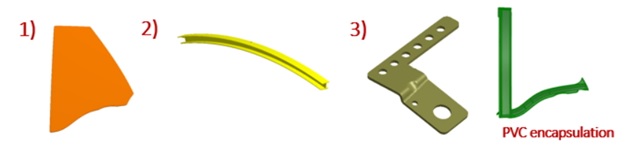
Fig. 1 Gruppo di incapsulamento progettato con (1) vetro trasparente, (2) canale di scorrimento del vetro e (3) inserto in alluminio.
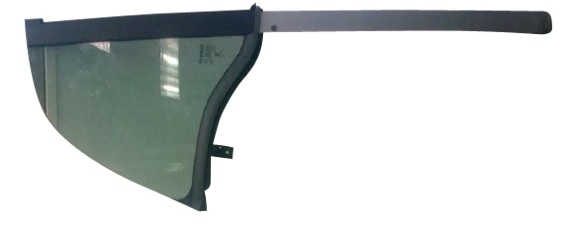
Fig. 2 Assemblaggio fisico
Tuttavia, la parte GRC stava ottenendo una deflessione di 5 mm lungo la direzione X a causa del restringimento e del raffreddamento irregolari. (Fig. 3). Pertanto, la zona GRC non riusciva a soddisfare i requisiti di gap e flush e ciò ha comportato difficoltà nel processo di assemblaggio. Moldex3D ha aiutato DURA ad analizzare e correlare i problemi esistenti per scoprire il motivo della deflessione del GRC (Fig. 4).
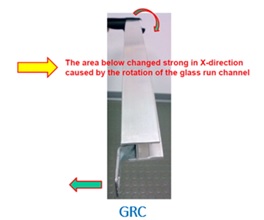
Fig. 3 La deformazione del GRC
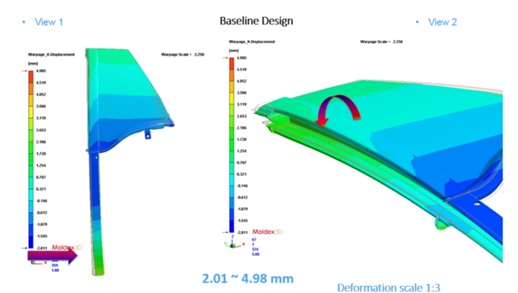
Fig. 4 Il risultato della deformazione di Moldex3D ha catturato il GRC deformato di 5 mm nella direzione X.
Con Moldex3D si sono analizzatii motivi alla base della deformazione.
I risultati della simulazione hanno mostrato che l'alta variazione dello spessore della parete vicino all'area GRC (Fig. 5), l'alto restringimento dovuto al punto caldo accumulato (Fig. 6), il restringimento volumetrico non uniforme e il tempo di raffreddamento insufficiente portavano al problema evidenziato. Si avevano anche segni di dispersione alla fine del raffreddamento (Fig. 7).
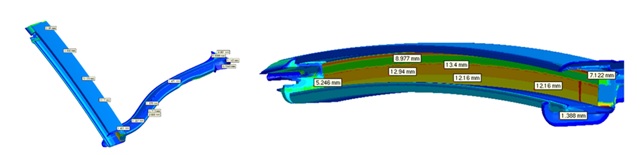
Fig. 5 Vi sono spessori variabili della parte.
Lo spessore massimo è 13,4 mm e lo spessore minimo è 0,5 mm.
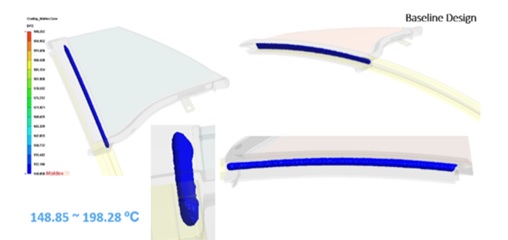
Fig. 6 La iso-superficie della zona di fusione plastica ha mostrato che internamente la parte ha ancora un nucleo importante fuso dopo il ciclo di raffreddamento.
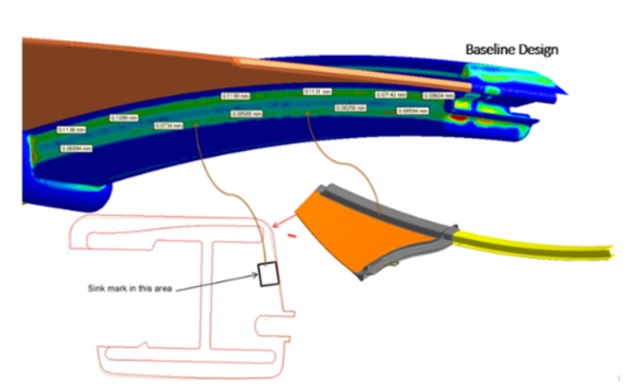
Fig. 7 La profondità massima del risucchio era di circa 0,1 mm alla fine del raffreddamento.
Dopo aver eseguito un paio di iterazioni per modificare le condizioni del processo per ridurre la deformazione, DURA non era ancora riuscita a soddisfare i requisiti di gap e flush.
Pertanto, hanno deciso di posizionare un inserto in ABS senza compromettere lo spessore e la resistenza della parte (Fig. 8 e 9).
DURA ha anche utilizzato Moldex3D come strumento di validazione
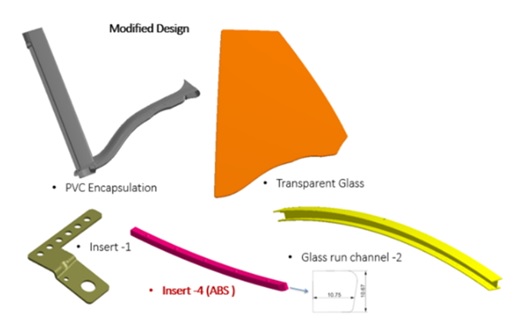
Fig. 8 Il design modificato
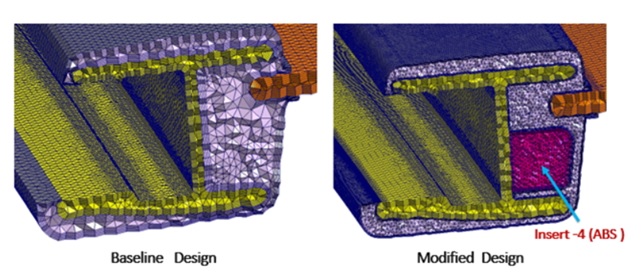
Fig. 9 Design di base e design modificato con un inserto in ABS
Di conseguenza, DURA è stata in grado di ridurre efficacemente la deformazione (Fig. 10 e 11) e risolvere con successo il problema del montaggio.
Si è ridotto significativamente il tempo di raffreddamento da 112 a 38 secondi (Fig. 12 e 13) ed eliminato i segni del lavandino (Fig. 14).
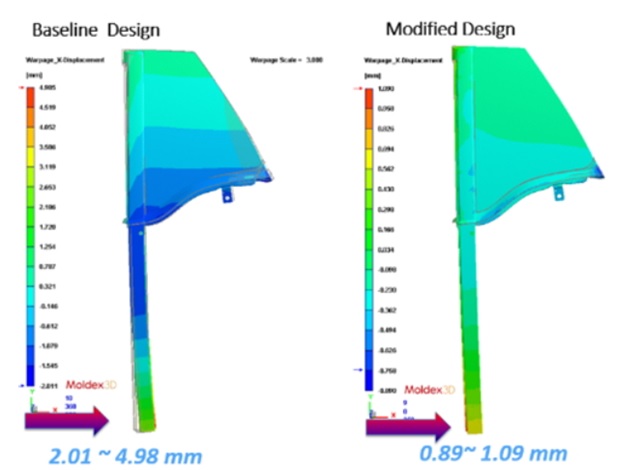
Fig. 10 Nel modello modificato, l'asse X è stato ridotto da 5 mm a 1 mm.
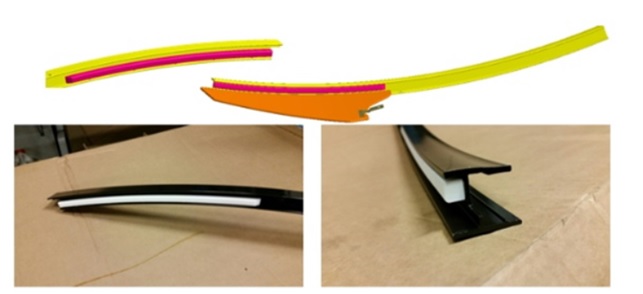
Fig. 11 Il prodotto reale del GRC con inserto in ABS ha mostrato che dopo aver posizionato l'inserto in ABS, lo spostamento dell'asse X è stato ridotto a 1 mm.
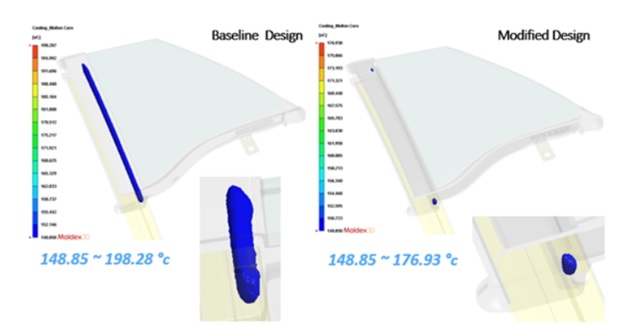
Fig. 12 La iso-superficie della zona di fusione plastica ha mostrato che il nucleo di fusione è stato ridotto dopo l'aggiunta dell'inserto ABS.
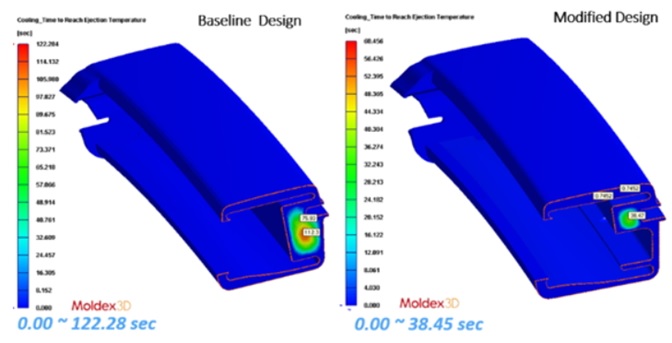
Fig. 13 Il tempo di raffreddamento richiesto è stato ridotto dopo l'aggiunta di un inserto ABS.
Sono bastati dai 35 ai 40 secondi per raggiungere la temperatura di espulsione per il progetto modificato.
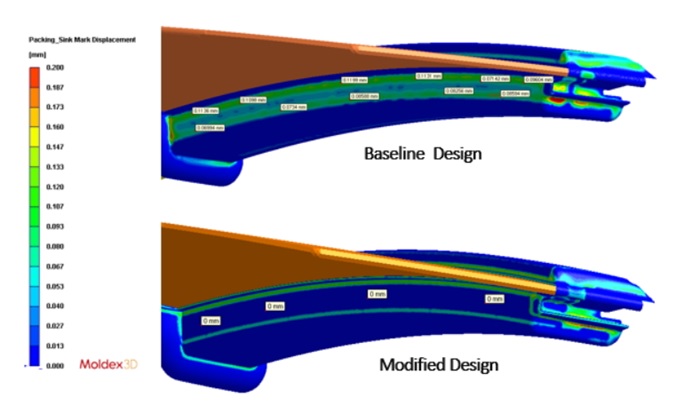
Fig. 14 La profondità del risucchio e dei segni in superficie è stata ridotta da 0,1 mm a 0 mm
Risultati
Il team DURA CFT ha utilizzato Moldex3D per verificare coerenza delle modifiche del progetto e ha scoperto che lo spessore del GRC può essere ridotto dell'85% senza compromettere la rigidità della parte.
Di conseguenza, hanno identificato la causa principale delle difettosità e verificato che il progetto modificato aiutava a ridurre la deformazione, i difetti di superficie ee il tempo di raffreddamento (Tabella 1).
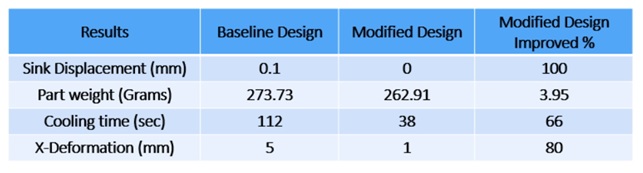
Tabella 1 Confronto della linea di base e del design modificato
Per ulteriori informazioni info@moldex3d.it
(GN – Ottobre 2019 , prt. 20190079)
TAGS: Automotive, Cool, Designer BLM, Flow, Moldex3D Advanced Package, Pack, Viscoelasticity, Warp