Moldex3D – Analisi True 3D e 2.5D per costruire parti di alta precisione
Nella produzione di pezzi con spessore sottile e “costante” (guscio), lo stress interno può verificarsi a causa di parametri del processo di stampaggio non ottimizzati, come ad esempio un non corretto raffreddamento nella zona punzone e/o nella zona matrice e quindi la presenza di forti gradienti di temperatura (>5°C).
Inoltre, se il progettista non ha dati completi sulle forze in gioco, nel progettare la parte, può incorrere in problemi di deformazione strutturale. D’altra parte, se il fattore di sicurezza, o tolleranza, fosse troppo restrittivo, potrebbe portare ad alti scarti di materiale; il dover creare parti con strutture/forme più complesse si accompagnano a costi di stampaggio superiori.
La tecnologia di meshing 2.5D Shell è già ampiamente utilizzata per l'esecuzione di analisi strutturali di componenti stampati a iniezione in una grande varietà di settori industriali, in particolare automotive, ma non solo.
Tradizionalmente, l'importanza delle proprietà dei materiali è spesso sottovalutata nell'analisi strutturale; ne deriva una non sufficiente valutazione degli effetti di orientamento delle fibre, temperatura di stampaggio, di gradienti di temperatura e di sforzo trasversali, delle tensioni residue, ed altro ancora.
Il risultato è che questo metodo di analisi semplificato, usato solitamente, porta a risultati imprecisi ed oggi non più accettabili.
Per ottenere i risultati delle analisi strutturali più accurate e complete, i progettisti sono soliti accompagnare ed integrare i risultati della simulazione dello stampaggio con analisi strutturale meccanica.
Anche questo passaggio non è semplice, in quanto i requisiti di maglia (mappatura della mesh) variano tra simulazione dello stampaggio ad iniezione e l'analisi strutturale meccanica.
L’analisi strutturale pone maggiormente l'accento sulla zona concentrazione degli sforzi; La simulazione dello stampaggio richiede la risoluzione maglia superiore nella direzione dello spessore, e del corretto comportamento, ad es., nelle regioni superficiali di contatto.
Pertanto, vari tipi di elementi di mesh e la loro densità sono necessari per eseguire, nel migliore dei modi, la simulazione stampaggio ad iniezione e fornire risultati di elevata affidabilità (reliability).
Moldex3D ha sviluppato una tecnologia di mappatura Shell 3D per risolvere i problemi di mappatura tra le diverse analisi.
Attraverso la sua tecnologia di simulazione True 3D, Moldex3D è in grado di trasferire dati e risultati 3D di simulazione di stampaggio all’ambiente 2.5D a elementi di maglia Shell, fornendo velocità ed efficienza, accompagnata da un’elevata precisione.
Utilizzando la funzione di mappatura Mesh in Moldex3D FEA Interface, i progettisti devono solo esportare i dati e la maglia, e poi importarli nella loro piattaforma CAE piattaforma di analisi strutturale per ulteriori analisi strutturali.
Come mostrato nella figura seguente, i progettisti utilizzano la tecnologia di mappatura Shell 3D per trasferire i risultati dalla simulazione dello stampaggio ad iniezione 3D per un modello strutturale 2.5D (Fig. 1).
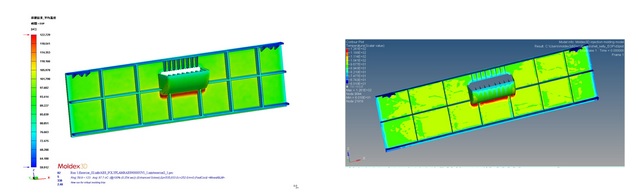
(Fig.1)
Dopo aver specificato carico e condizioni al contorno (Fig. 2),
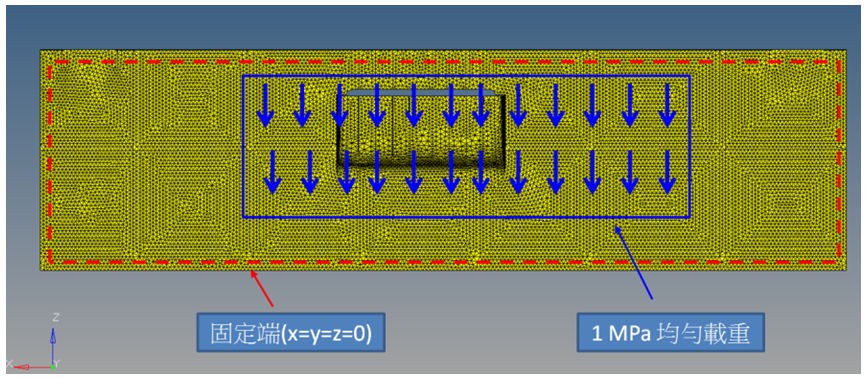
(Fig.2)
i progettisti possono facilmente ottenere risultati delle analisi sulla distribuzione degli spostamenti e dello stress (Fig. 3 e Fig. 4).
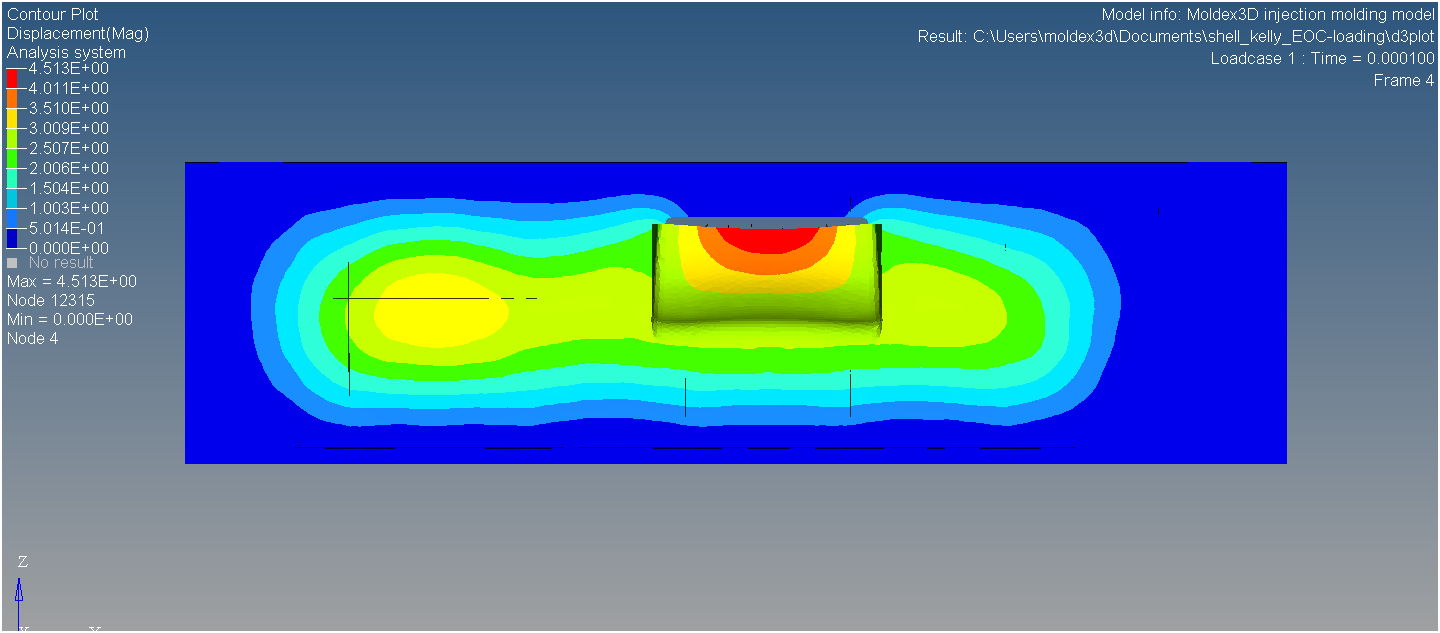
(Fig.3)
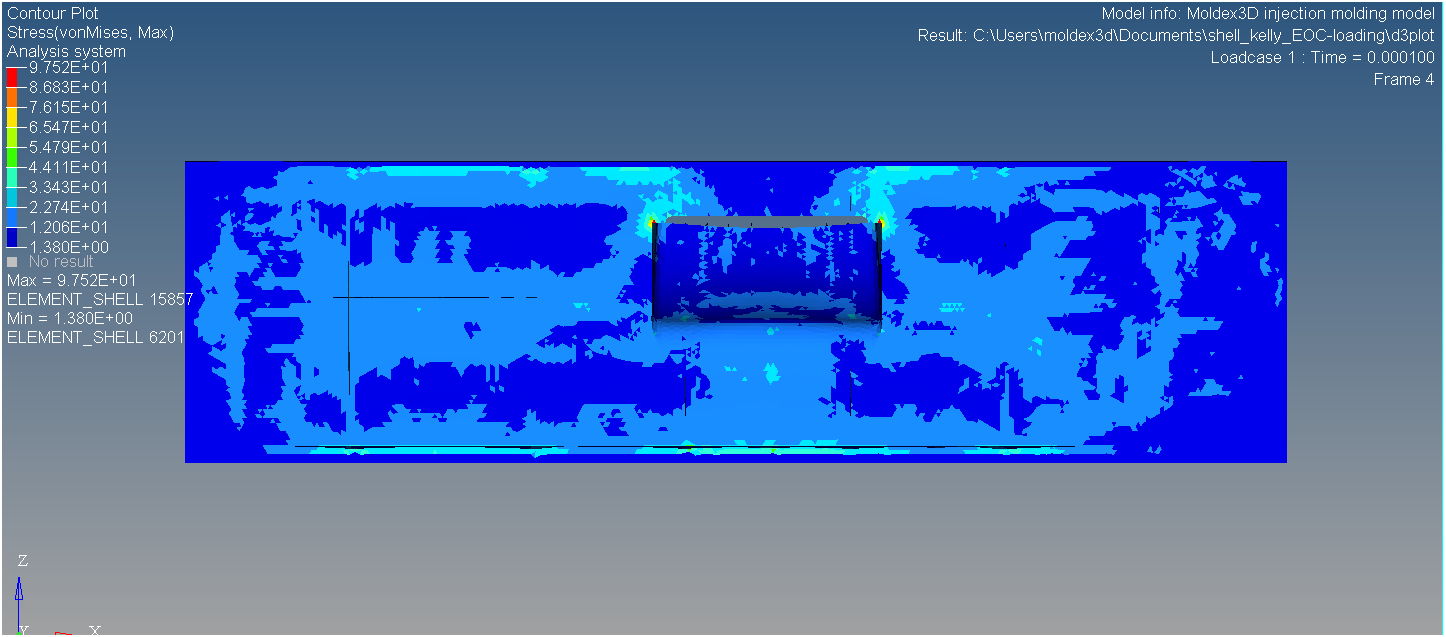
(Fig.4)
La tecnologia di simulazione True 3D di Moldex3D è quindi in grado di generare risultati delle analisi più accurati, per una più realistica analisi strutturale in ambiente 2.5D.
Questa modalità di procedere è diventato un mainstream attraverso le industrie che quindi pretendono di avere dati di simulazione True3D del processo di stampaggio, in particolare con materiali rinforzati con fibre, dove densità e orientamento spaziale sono importanti.
Tutto questo per permettere ai i progettisti di meglio valutare gli effetti dei processi di stampaggio e di avere un migliore controllo sulla qualità del prodotto; integrare pienamente la simulazione dello stampaggio ad iniezione, o anche diversi altri processi di stampaggio, con l'analisi strutturale, secondo le modalità descritte sopra, diviene fondamentale, per una corretta valutazione della situazione.