Convalida del processo VARTM in composito a struttura sandwich (PVC) con Moldex3D
A cura di Barton Lin, ingegnere senior presso il team di supporto tecnico, Moldex3D
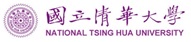
La National Tsing Hua University (NTHU) si è sviluppata in un'università di ricerca completa che offre una gamma completa di corsi di laurea in scienza, tecnologia, ingegneria, scienze umane, scienze sociali e management. NTHU si classifica costantemente come una delle principali università dell'Asia orientale ed è ampiamente riconosciuta come un incubatore leader per futuri leader.
(Fonte: http://nthu-en.web.nthu.edu.tw/bin/home.php?Lang=zh-tw)
Premessa
La maggior parte delle pale delle turbine eoliche oggi sono prodotte con materiali compositi.
I materiali compositi avvolgono il materiale del nucleo con un certo numero di strati di fibre per formare una struttura a sandwich, che può ridurre efficacemente il peso delle pale mantenendo un’elevata resistenza strutturale.
Attualmente, la maggior parte dei materiali di base sono realizzati in PVC e legno di balsa.
Per facilitare il processo di infusione della resina, vengono praticate scanalature di una certa dimensione sulla superficie dell'anima.
Per ottenere risultati di simulazione accurati, è necessario modellare e simulare contemporaneamente il materassino in fibra e le scanalature, il che richiede un metodo di simulazione diverso da quello tradizionale, robusto ed efficiente.
Sfide
Poiché il materiale del nucleo conteneva scanalature e canali, al team è stato assegnato non solo il compito di simulare il materassino in fibra, ma anche studiare e ottimizzare una geometria più complessa, il che ha aumentato la difficoltà nell'ottenere risultati di simulazione accurati.
Soluzioni
Moldex3D RTM può definire e assegnare diverse proprietà dei materiali e orientamento delle fibre per ogni strato, il che aiuta a semplificare il complesso flusso di lavoro di simulazione RTM.
Con l'aiuto delle funzionalità e caratteristiche di Moldex3D RTM per la simulazione di permeabilità equivalente, il team di Tsing Hua è stato in grado di prevedere e catturare , in modo preciso e puntuale, i comportamenti del flusso all'interno delle scanalature e dei canali, che corrispondevano bene ai risultati sperimentali.
Benefici
• Consentire la simulazione realistica di strutture sandwich in materiale composito
• Processo di simulazione RTM ottimizzato per ridurre i tempi di sviluppo del prodotto
•Ottimizzazione della struttura e dei processi
Argomento di studio
Lo studio esistente spesso tratta l'intero rinforzo, inclusi sia il materiale del nucleo che i fogli di fibra (tessuto FRP), come un singolo oggetto e descrive i modelli del flusso di resina con un'unica equazione di governo, ovvero la legge di Darcy.
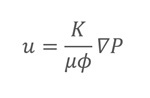
Nell'equazione si comprende la velocità di flusso e la viscosità della resina, la permeabilità e la porosità del mezzo di flusso, e il gradiente di pressione.
In tal modo, le influenze della distribuzione e della regione priva di fibre nel nucleo sul modello di flusso non possono essere disaccoppiate, limitando l'accuratezza e la flessibilità dei modelli sviluppati.
In questo studio, il team NTHU combina tessuto di fibra di vetro e anima in PVC con il canale come un composito a struttura sandwich che sarà il nostro modello di studio (Fig. 1).
Il metodo sperimentale è il Vacuum Assisted Resin Transfer Moulding (VARTM) (Fig. 2).
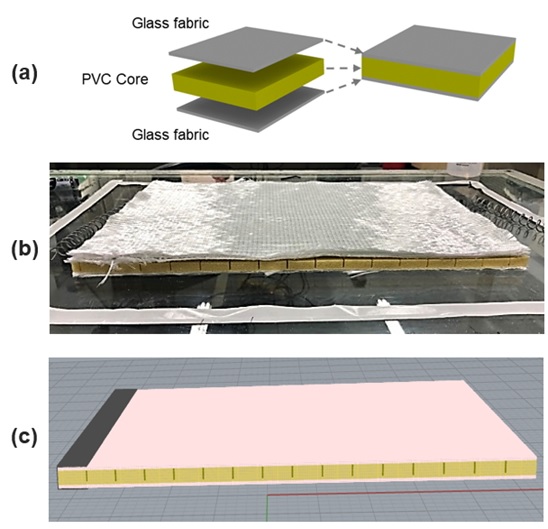
Fig. 1 Il modello della struttura a sandwich: (a) diagramma schematico, (b) oggetto reale e (c) mesh solida per la simulazione.

Fig. 2 Il metodo sperimentale in questo studio
Il team NTHU ha simulato separatamente i comportamenti del flusso di resina all'interno della fibra e della regione priva di fibre (cioè i canali) nel nucleo in PVC utilizzando il metodo dei volumi finiti (FVM) (Fig.3).
La dimensione del nucleo è 480 × 320 × 10,2 mm3.
Ci sono due tipi di canali nel core. I canali rettangolari con una larghezza di 1 mm e un'altezza di 8,2 mm sono disposti orizzontalmente in uno schema incrociato. La distanza tra i due canali paralleli più vicini è di circa 29 mm. I 408 canali cilindrici verticali con un diametro di 2 mm e un'altezza di 10,2 mm sono distribuiti uniformemente nel nucleo.
Il flusso di resina nella fibra è modellato utilizzando la legge di Darcy.
Dopo aver progettato la struttura del materiale del nucleo, anche il comportamento del flusso all'interno dei canali viene modellato tramite la legge di Darcy (permeabilità equivalente).
In tal modo, l'intera simulazione può essere progettata utilizzando lo stesso tipo di equazioni di governo, rendendo le condizioni al contorno relativamente facili da impostare.
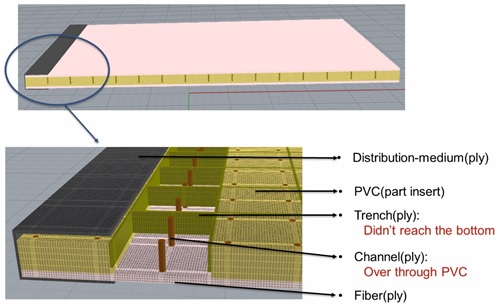
Fig. 3 Mesh solida e impostazione degli attributi
I risultati della simulazione sono stati confrontati con i risultati sperimentali per illustrare la fattibilità del modello proposto.
Il modello di flusso simulato mostra bene i modelli osservati (Fig. 4). Inoltre, il framework di simulazione proposto ha la flessibilità di gestire varie combinazioni di materiali e fibre di base, che è una caratteristica molto apprezzata in ambiente industriale.
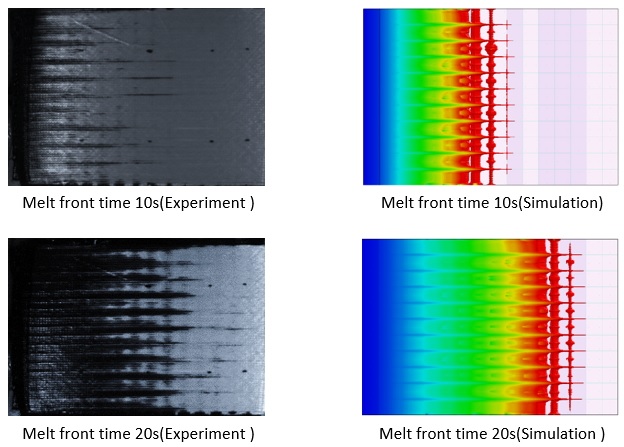

Fig. 4 Tempo di fusione tra esperimento e simulazione.
Risultati
In questo studio, il team NTHU ha utilizzato l'esclusiva “funzione di permeabilità equivalente” di Moldex3D RTM per simulare accuratamente le caratteristiche di flusso nella scanalatura e del canale di flusso per il materiale d'anima in PVC e ha ottenuto un'elevata coerenza tra i risultati della simulazione e le verifiche fisiche sperimentali.