Introduzione al processo di co-stampaggio ad iniezione
La co-iniezione (o stampaggio sandwich) è il processo attraverso il quale si alimentano diverse colate plastiche (parte esterna - pelle e parte interna - core), uno dopo l'altro, in uno stampo, durante il processo di stampaggio ad iniezione. Il materiale fuso devono fare contatto tra loro, ma non dovrebbero fluire l'uno nell'altro, se non nella parte vera e propria di contatto.
Una varietà di combinazioni di materiali, tra parte interna e parte esterna, es. una a tocco morbido e una parte interna a costituire il sostegno “duro”, o una parte esterna in materiale pregiato/vergine, ed una interna di riempimento in materiale riciclato.
Questo tipo di processo viene utilizzato in svariati casi, per risparmiare materia prima pregiata, in vari ambienti dall’automobilistico al domestico, o su parti di un certo spessore (anche per obiettivi strutturali).
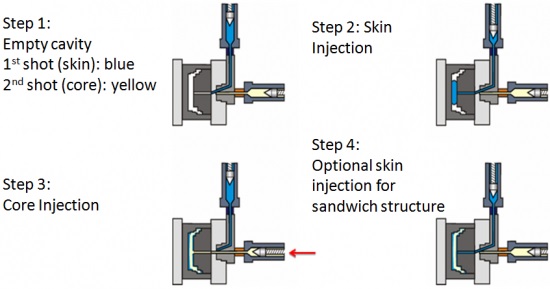
La riduzione dei costi, il riutilizzo dei rifiuti e materiale riciclato, il miglioramento delle prestazioni meccaniche del prodotto sono i principali vantaggi di utilizzare nella scelta di un processo di co-iniezione.
Il processo di co-iniezione inizia con l'iniezione di un primo materiale (pelle) nella cavità , attraverso un colpo breve e predeterminato in quantità e tempo, seguito da un secondo colpo (core) dietro la pelle fino a che la cavità sia completamente riempita e “stabilizzata” (fase di post – compressione o mantenimento).
Il comportamento del flusso lascia uno strato congelato sulla parete della cavità; mentre il secondo colpo (sequenziale) penetra nel nucleo di fusione attraverso il percorso di minore resistenza per spostare il primo materiale verso la superficie esterna.
A causa di questo comportamento, il primo materiale guidato dalla forma della cavità, spinge ancor più avanti e verso l’esterno aderendo al meglio la superficie dello stampo.
Quindi, si va a costituire una specie di sandwich ideale dove abbiamo un nucleo/core completamente racchiuso dalla pelle.
Panoramica delle funzioni simulazione con Moldex3D ( CIM Co-Injection Molding)
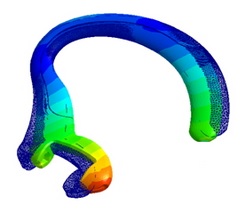
Modulo Moldex3D di co-iniezione offre potenti soluzioni di modellazione per stimare la distribuzione spaziale del materiale all'interno della cavità .
E 'importante in applicazioni strutturali, perché la rigidità del prodotto dipende in gran parte dalla distribuzione e dalla densità pelle/core . E' anche importante il fattore estetico in quanto il rapporto e la distribuzione dei due materiali iniettati condiziona anche il senso del tatto, che dipende anche dallo spessore della pelle, oltre ovviamente dal tipo di materiale utilizzato per la pelle esterna.
Un altro aspetto importante della co-iniezione è quello di massimizzare il contenuto di base.
Il modulo co - iniezione è in grado di prevedere la percentuale del riempimento a cui avviene la stabilizzazione e quindi anche come regolare il secondo colpo.
Tutte queste previsioni si basano su importanti fattori legati alle condizioni di processo , ad esempio velocità di iniezione, modalità di commutazione primo/secondo colpo, e le proprietà dei materiale plastici utilizzati (Viscosità, PVT ecc.).
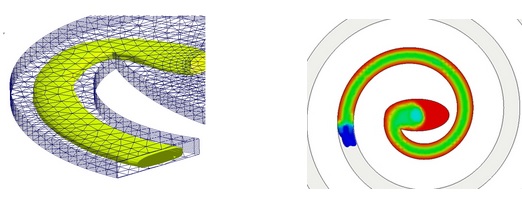
Che cosa può fare Moldex3D?
.Visualizzare i modelli di riempimento dinamici della pelle e del nucleo
.Prevedere potenziali difetti , tra cui lo squilibrio di flusso, la penetrazione di base , etc.
.Prevedere ritiro e deformazione riguardanti l'interazione tra la pelle e il nucleo di materiali
.Prevedere viscosità, densità e distribuzioni per migliorare l'uniformità sia in fase di iniezione sia in fase di compattamento
.Valutare il punto di commutazione delle due fasi (pelle e nucleo)
.Ottimizzare le condizioni di processo, come ad esempio il posizionamento del gate , la pressione di iniezione, o la forza di serraggio dello stampo (clamping force)
.Ottimizzare lo spessore della pelle e valutare correttamente i risultati anche per un’eventuale l'analisi strutturale meccanica avanzata
Modulo Add- On : CIM Co-Injection Molding