UMass - University of Massachusetts
Metal Replacing
Progettazione di un deragliatore posteriore in plastica per bicicletta
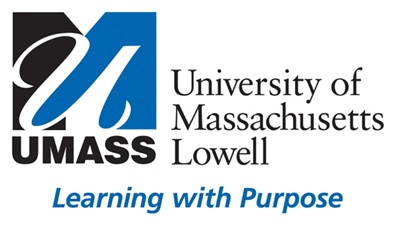
Profilo del cliente
- •Cliente: Università del Massachusetts Lowell (UMass Lowell)
- •Paese: U. S. A.
- •Settore: Educativo / Accademia
- •Soluzione: Moldex3D Studio, Expert, Flow, Pack, Cool, Warp, Fiber, FEA Interface
Il programma Plastics Engineering (ESE) è amministrato dal Dipartimento di Ingegneria delle Materie Plastiche, UMass, Lowell.
Vari livelli di supporto esterno hanno permesso al programma di continuare la sua missione di essere riconosciuto per l'eccellenza nell'educazione e nella ricerca sull'ingegneria delle materie plastiche. (Fonte)
Premessa
I deragliatori posteriori sono i componenti strutturali per gli ingranaggi delle bici (Fig. 1).
Sono comunemente realizzati utilizzando compositi termoindurenti rinforzati con alluminio, acciaio o fibre.
Il componente è solitamente un assemblaggio di due parti metalliche che tengono la catena in mezzo. Questo progetto ha proposto di utilizzare la simulazione di processo e strutturale per riprogettare il componente per la produzione con una resina rinforzata con fibre. Questo approccio include la riprogettazione e l'ottimizzazione della parte per lo stampaggio a iniezione e l'analisi strutturale utilizzando i risultati CAE come input per le proprietà del materiale ortotropico. L'accoppiamento della simulazione di processo con il FEA strutturale consente l'ottimizzazione avanzata della progettazione di parti e stampi.
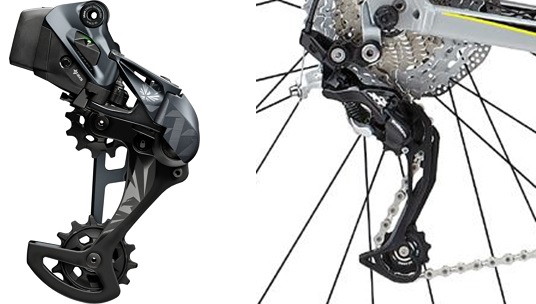
Fig. 1 Esempi di gruppo cambio posteriore bici
Sfide
- •Ottimizzare la progettazione di parti e stampi per un componente strutturale rinforzato con fibre
- •Per ridurre al minimo la deflessione della parte causata dall'orientamento della fibra
- •Controllo dei parametri di processo per l'ottimizzazione della deformazione e la deflessione minima (Fig. 2)
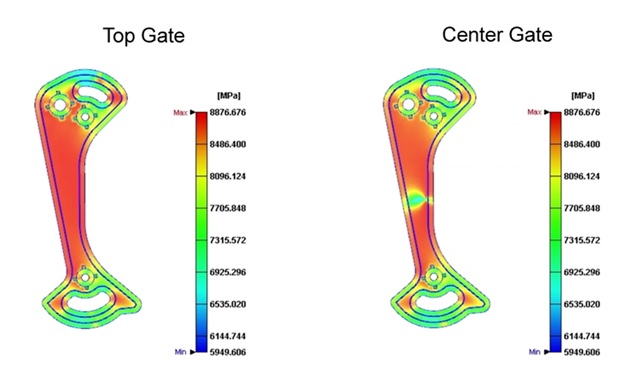
Fig 2. Risultati della deformazione del progetto originale: modulo elastico
Soluzioni
Il team di UMass Lowell ha utilizzato Moldex3D per studiare la correlazione tra progettazione di parti, progettazione di stampi, orientamento delle fibre e proprietà strutturali. Il software è stato utilizzato per convalidare il contenuto di fibre e la selezione della resina da una prospettiva di elaborazione e funzionale. L'approccio dimostra l'efficacia della combinazione di simulazione di processo e simulazione strutturale per la riprogettazione di prodotti con polimeri rinforzati con plastica.
Benefici
- •Riprogettazione efficace delle parti con plastica e convalida delle proprietà strutturali rispetto al design originale (metallo)
- •Previsto con precisione le prestazioni meccaniche della parte progettata utilizzando l'interfaccia FEA le proprietà del materiale relative al processo.
- •Contenuto e orientamento delle fibre ottimizzati grazie al design ottimale dello stampo
- •Evitati costosi prototipi e ricostruzioni di stampi attraverso l'accoppiamento di lavorazioni e simulazioni strutturali.
Caso di studio
The objectives of this study were to design a structural component using fiber-reinforced thermoplastic to replace metal. The UMass team used Moldex3D to analyze the effects of processing on orthotropic material properties, and tried to optimize the design for manufacturing, considering fiber content, part design and mold design. Then, they validated product design by coupling Moldex3D and FEA software.
To achieve desired structural properties, the team proposed several designs with (1) different gate locations, (2) fiber content and (3) the process parameters (Fig. 3). Three different gate locations and other designs were analyzed; the optimum design was defined considering the fiber orientation and the structural properties.
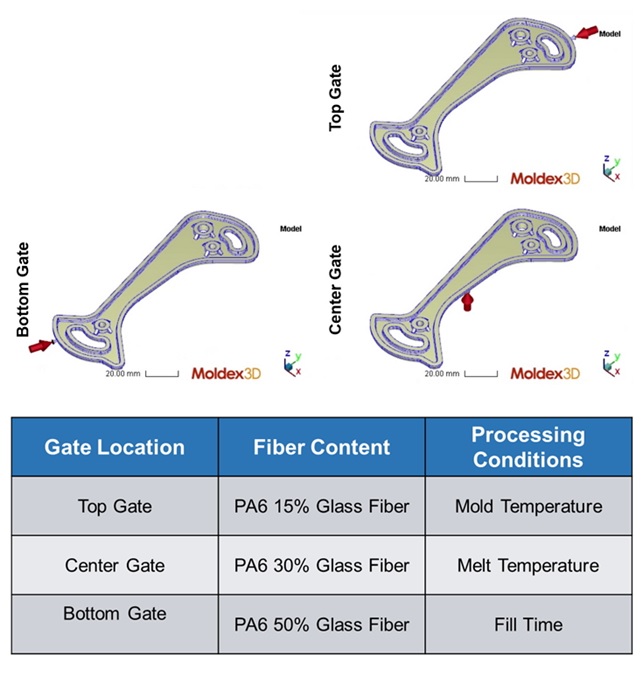
Fig 3. Posizioni dei gate e approccio di analisi
Il team di UMass Lowell ha cercato di ottimizzare l'orientamento della fibra e il modulo elastico utilizzando Moldex3D, i risultati sono mostrati di seguito. (Fig. 4 e 5).
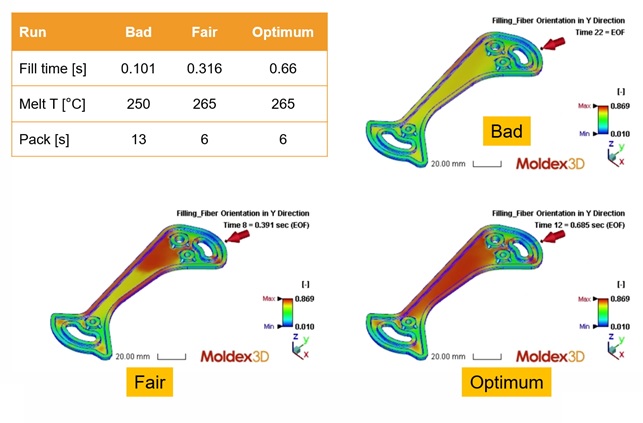
Fig 4. Ottimizzazione dell'orientamento delle fibre regolando i parametri di processo
Fig 5. Ottimizzazione del modulo elastico regolando i parametri di processo
Hanno anche valutato tre composti caratterizzati da diversi contenuti di fibre per sintonizzare le proprietà meccaniche. È stato sviluppato un modello strutturale per analizzare la rigidità della parte. Il modello di materiale ortotropico è stato esportato da Moldex3D e inserito nel modello strutturale. Le prestazioni della parte sono state valutate considerando il rapporto forza-peso. La parte riprogettata mostra un rapporto forza-peso più elevato rispetto alle parti metalliche originali (Fig. 6).
.jpg)
Fig 6. Risultati strutturali
L'aumento dello spessore nominale della parete ha comportato un significativo miglioramento della rigidità. Il team ha scoperto che 3 mm era lo spessore ottimale in base al rapporto forza-peso. Anche i disegni delle costole longitudinali e incrociate hanno notevolmente migliorato la reazione di forza. Confrontando i disegni senza costole, con costole longitudinali e con costole incrociate, hanno trovato la costola longitudinale ottimale, innescando un elevato orientamento delle fibre lungo le costole. Un maggiore contenuto di fibre ha permesso una rigidità paragonabile alle parti in acciaio e alluminio (Fig. 7 ~ 10).
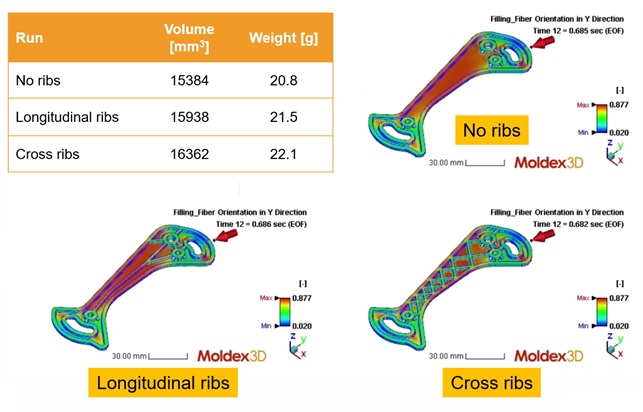
Fig 7. Risultati dell'orientamento delle fibre dei progetti originali e rivisti
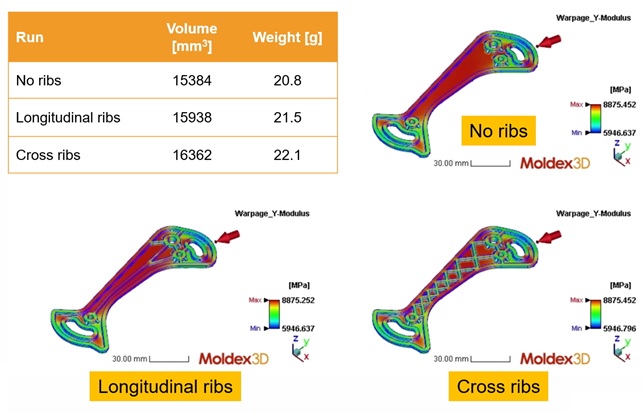
Fig 8. Risultati del modulo elastico dei disegni originali e rivisti

Fig 9. Risultati strutturali del progetto rivisto: influenza delle costole
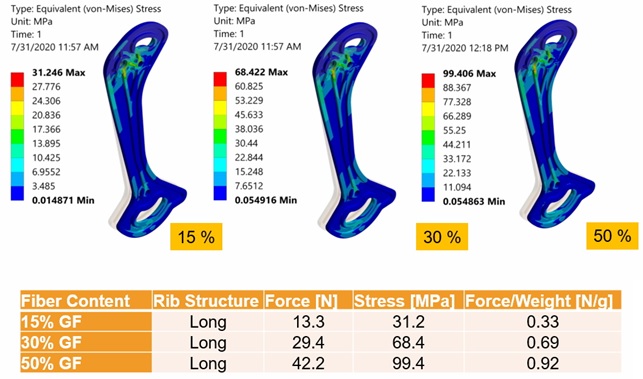
Fig 10. Risultati strutturali del progetto rivisto: influenza del contenuto di fibre
Di conseguenza, hanno deciso che il miglior design era di 3 mm con nervature longitudinali e contenuto di fibre del 30%. I progetti ottimizzati dettagliati e i parametri di processo sono mostrati in Fig. 10 e 11.
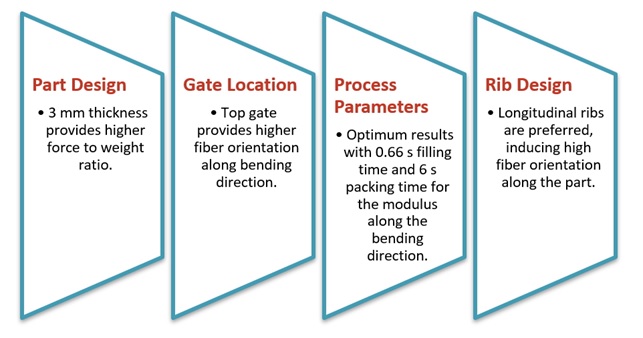
Fig 11. Progettazione di parti e processi con Moldex3D
Fig 12. Interfaccia FEA e valutazioni strutturali
Risultati
Utilizzando Moldex3D e gli strumenti Design of Experiment, il team UMass è stato in grado di esplorare e confrontare molte iterazioni di progettazione a basso costo.
Le proprietà meccaniche di un termoplastico rinforzato con fibre potrebbero essere quantificate e ottimizzate a partire dai risultati dell'orientamento delle fibre.
Il modulo Moldex3D Warp ha aiutato a esplorare se la parte può essere assemblata correttamente evitando costose modifiche alla progettazione dello stampo.
Attraverso l'interfaccia FEA, le proprietà del materiale relative al processo potrebbero essere utilizzate per prevedere con precisione le prestazioni meccaniche della parte progettata.
L'esportazione del modello di materiale ortotropico è stata estremamente utile per esplorare soluzioni di sostituzione dei metalli, consentendo di superare la complessità delle proprietà dei materiali non isotropi.