Il processo di stampaggio ad iniezione assistita da fluido (FAIM) applica una tecnica per consentire al fluido assistito di entrare dopo lo stampaggio ad iniezione di plastica e formare uno svuotamento, ovvero, una struttura cava all'interno dei prodotti.
La FAIM (Fluid Assisted Injection Molding) è in grado di produrre pezzi cavi con un buon controllo dimensionale che non è possibile ottenere mediante iniezione convenzionale e soffiaggio.
Inoltre, a differenza del tradizionale stampaggio ad iniezione, il fluido può mantenere la pressione dalla parte interna per una migliore distribuzione della pressione attraverso lo spessore e quindi può produrre migliori finiture superficiali, ridurre il restringimento e lo stress residuo e ottenere una maggiore precisione dimensionale, migliore deformazione.
Come tale, la tecnica di FAIM continua a essere promossa con molti nuovi brevetti di metodologia di processo in tutto il mondo [i, ii, iii].
In base alla quantità di materiale fuso iniettato nellaIn base alla quantità di materiale fuso iniettato nella cavità, possiamo classificare il processo FAIM generalmente in due tipi:
1. Metodo short-shot: in questa applicazione FAIM, la quantità della plastica iniettata è inferiore allo spazio della cavità e si basa sul fluido per premere e riempire completamente la cavità. Questo metodo è molto adatto per prodotti a forma di asta o cavità di grandi dimensioni e il tasso di vuoto è normalmente inferiore al 35%.
2. Metodo full-shot: con l'iniezione dell'intera quantità di resina nello spazio della cavità, il fluido assistito supporta quindi solo l’impaccamento di più materiale per il restringimento durante la fase di raffreddamento e collabora con diverse tecniche (da discutere in seguito) per un migliore controllo del processo e del risultato finale.
Pertanto, consente una gamma più ampia di velocità/pressioni di svuotamento e può efficacemente migliorare i problemi di risucchi o difettosità di superficie e/o di deformazione per prodotti che alla fine hanno pareti sottili.
Il processo FAIM full-shot è una tecnica più favorita tra i produttori poiché il metodo short-shot ha maggiori probabilità di causare difetti come segni superficiali di flusso o segni dovuti alla esitazione nel fluire del materiale.
Ad esempio, il push-back è una tecnica comune di stampaggio ad iniezione assistita dall'acqua (WAIM) (mostrato in Fig. 1).
In questo metodo di stampaggio, gli ingressi della parte fusa e per l'acqua si trovano su due diversi lati della cavità e l'acqua viene iniettata dopo che la cavità è stata riempita completamente per spingere nuovamente la plastica fusa nel sistema di iniezione.
Con questa tecnica, non solo è possibile eliminare il problema dei segni di flusso presenti nel metodo short-shot, ma anche ridurre lo spreco di materiale riutilizzando la resina che ritorna nell'unità di iniezione e rimuovendo il trabocco dalla cavità (overflow).
Tuttavia, questa tecnica richiede un design speciale dell'ugello per impedire al fuso di rifluire durante la fase di riempimento.
Inoltre, gli ingressi del materiale fuso e quello del fluido devono essere ben considerati nella progettazione del prodotto.
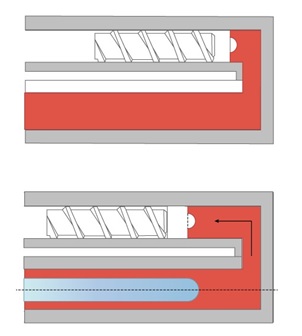
Fig. 1 Illustrazione del metodo push-back [i]
Questo studio mira a simulare un pedale per auto modellato con il metodo push-back. Lo spessore della parete del pedale non è uniforme, perché deve soddisfare i requisiti di resistenza e solidità meccanica (vedi Fig. 2).
Il materiale applicato in questo studio è un PA6, un materiale cristallino con proprietà predefinite fornite dal laboratorio materiali di Moldex3D come elencato nella Tabella 1.
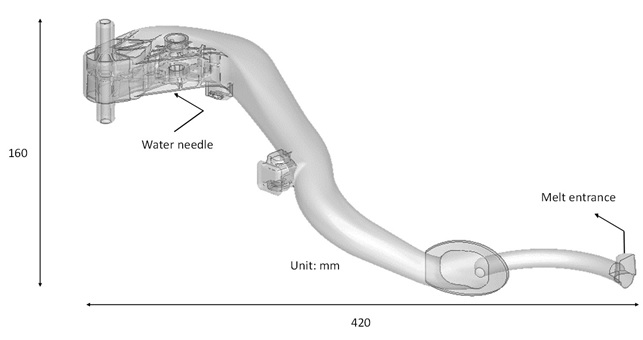
Fig. 2 Illustrazione della geometria del pedale
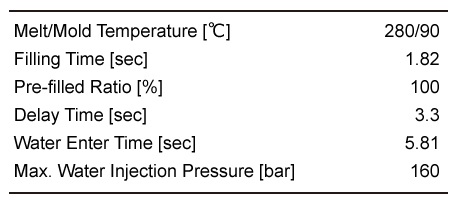
Tabella 1 Condizioni di processo
La caratteristica principale del metodo push-back è l'apertura dell'ugello per consentire al fuso di fluire all'indietro attraverso l'unità di iniezione quando il fluido entra.
Durante la simulazione, la pressione all'ingresso del fuso viene impostata su zero all'avvio dell'iniezione di acqua.
Pertanto, la distribuzione complessiva del gradiente di pressione si inverte, più alta dall'iniezione di acqua e più bassa vicino all'ingresso del fuso.
Questo comportamento può essere osservato attraverso la variazione della distribuzione della pressione durante la penetrazione dell'acqua mostrata in Fig. 3.
Il diagramma semplificato nella Fig. 4 mostra l'effetto del gradiente di pressione alla penetrazione dell'acqua e il potenziale percorso dell'acqua assistita usando la direzione della velocità.
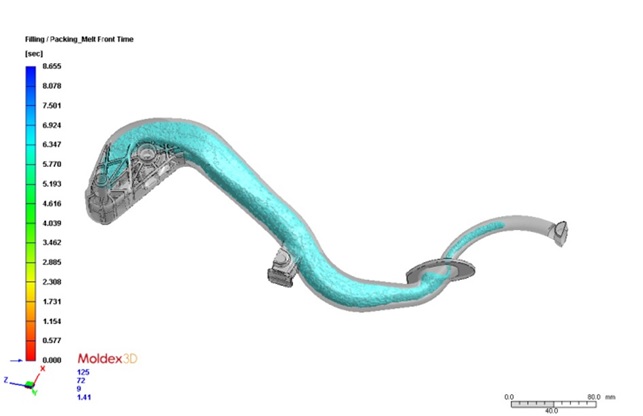
Tempo di riempimento: 7,7 sec Tempo di riempimento: 8,1 sec (a) Fine del tempo di riempimento
Fig. 3 Risultati della penetrazione dell'acqua e della distribuzione della pressione in momenti diversi
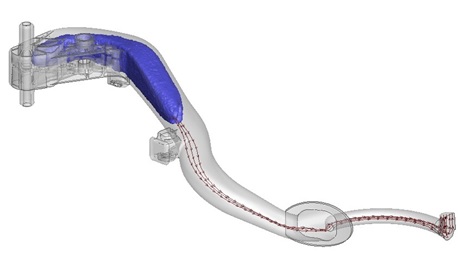
Fig. 4 Semplificazione del diagramma di penetrazione dell'acqua assistita al tempo di riempimento di 8,3 sec.
Quando entra l'acqua, la variazione con il tempo della pressione dell'acqua e della portata di riflusso all'entrata del fuso può essere vista in Fig. 5.
Il risultato mostra chiaramente che la portata di riflusso è influenzata dal controllo della pressione dell'acqua.
Quando raggiunge la fine del core-out (tempo di riempimento: 8,7 sec), la pressione dell'acqua verrà ridotta per controllare la quantità di plastica che scorre indietro e impedire all'acqua di rifluire all'ugello, quindi la penetrazione dell'acqua rimarrà nella camera fredda.
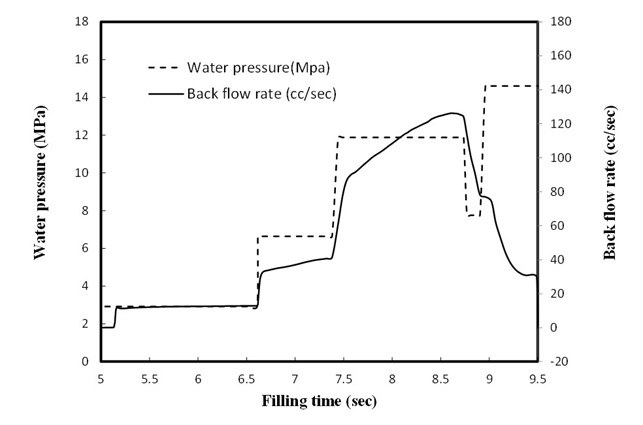
Fig. 5 La variazione della pressione dell'acqua e della portata del processo push-back
La Fig. 6 mostra che il risultato della simulazione si abbina bene con l'esperimento, la valvola di riflusso si chiuderà al tempo di riempimento di 8,8 sec. Alla chiusura della valvola, la pressione dell'acqua assistita verrà aumentata.
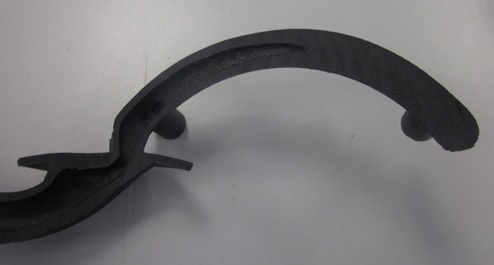
(a)
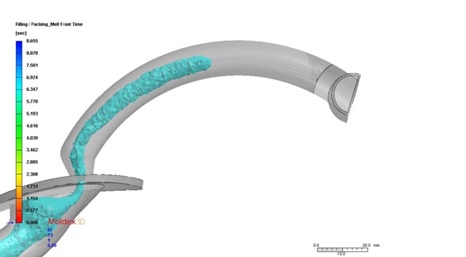
(b)
Fig. 6 La validazione del risultato core-out, tra (a) Esperimento e (b) Simulazione, della penetrazione dell'acqua all'interno della parte del pedale
Per esaminare ulteriormente le prestazioni del core-out, la Fig. 7 mostra il risultato del core-out in 4 diverse sezioni trasversali (a).
Fig. 7 Il confronto dell'area core-out in (a) 4 diverse sezioni trasversali, (b) risultati sperimentali e (c) risultati della simulazione
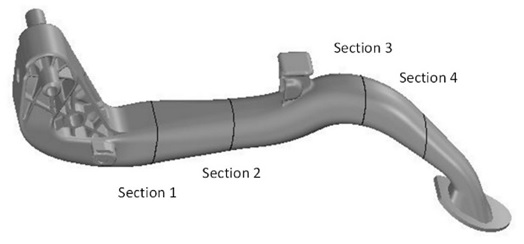
Entrambi i risultati sperimentali (b)
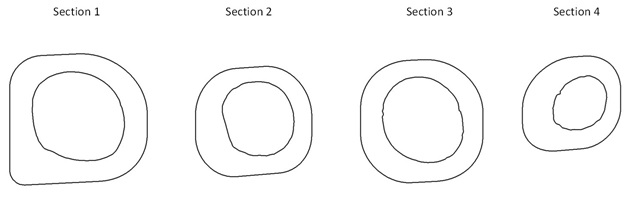
e numerici (c)
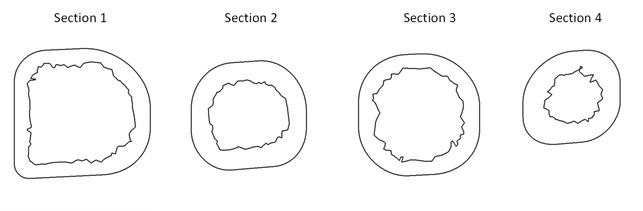
mostrano che il rapporto core-out è più alto nelle aree con una grande sezione trasversale.
Fig. 7 Il confronto dell'area core-out in (a) 4 diverse sezioni trasversali, (b) risultati sperimentali e (c) risultati della simulazione
D'altra parte, la Sezione 4 è più vicina all'ingresso del materiale fuso e ci sarà uno strato di congelamento più spesso, una pressione dell'acqua più bassa e un riflusso più piccolo (Fig. 4) quando l'acqua raggiungerà vicino all'estremità di riempimento, con conseguente minore area di fuoriuscita del nucleo.
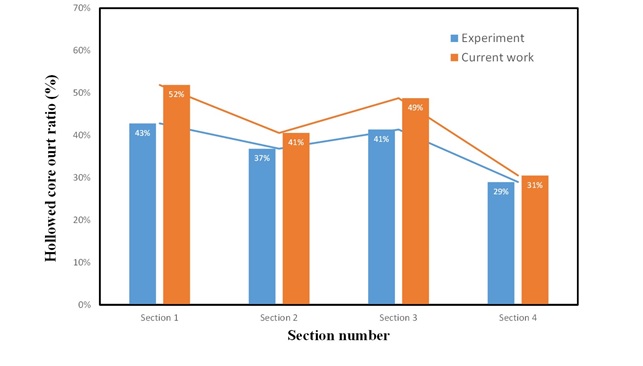
Fig. 8 Confronto del rapporto core-out tra risultato sperimentale e risultato della simulazione
La Figura 8 mostra che i risultati sperimentali e di simulazione del rapporto core-out sono altamente correlati.
Tuttavia, vi è una maggiore discrepanza tra i risultati della simulazione rispetto all'esperimento nell'area di core-out nelle sezioni 1 e 3, come mostrato. La causa può essere l'attuale assunzione del flusso laminare dell'acqua assistita non può catturare il comportamento del vortice indotto dalla viscosità nella parte più spessa.
Con l'avanzare della tecnologia di stampaggio ad iniezione assistita dall'acqua, il metodo full-shot sta acquisendo importanza anche studi recenti. Questo articolo è il primo studio di ricerca sull'analisi numerica del metodo full-shot per il processo push-back.
Un'analisi di stampaggio completamente tridimensionale viene eseguita sul processo di riempimento con geometria complessa, considerando l'effetto delle condizioni di processo sul comportamento core-out.
La simulazione è anche validata con il risultato sperimentale. Questo studio servirà come riferimento prezioso per futuri studi sui metodi full-shot.
[i] M. L. Wang, R. Y. Chang, C. H. Hsu, Molding Simulation: Theory and Practice, Hanser Publications, 2018
[ii] Yen-Shou Chen, “A Study of the Liquid-Assisted Injection Molding of Thermoplastic Materials” Thesis of Chang Gung University, 2002
[iii] L. Li, Y. Peng and W. Wei, “Recent advances on fluid assisted injection molding technique”, Recent Patents on Mechanical Engineering, Vol.7, No.1, 82-91, 2014
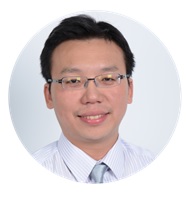
Dr. Jim Hsu
Direttore senior presso la divisione R&D di CoreTech System (Moldex3D)
Jim Hsu ha conseguito un dottorato presso il Dipartimento di Ingegneria Chimica, Università Nazionale Tsing Hua. Attualmente è Program Manager presso la Divisione R&D di Moldex3D, concentrandosi sullo sviluppo di soluzioni di personalizzazione del solutore e delle specifiche del programma.
I suoi campi di ricerca includono la ricerca sui materiali della reologia dei polimeri, la fluidodinamica computazionale / lo sviluppo del solutore CAE, il processo di confezionamento IC, lo stampaggio a iniezione con fluido (gas, acqua), lo stampaggio a co-iniezione e lo stampaggio a trasferimento di resina.
Il Dr. Hsu ha pubblicato circa 20 articoli tecnici e ottenuto numerosi brevetti.
Collabora inoltre con numerosi produttori di imballaggi IC (Integrate Computers) per progetti di sviluppo.
<< Un ringraziamento particolare a Gorka Jaio di Batz per aver fornito dati sperimentali sulla penetrazione dell'acqua e stimolare discussioni.
E grazie ai colleghi Henry Huang e William Wu per aver offerto feedback e suggerimenti lungo la strada. >> Jim Hsu