Miglioramento delle previsioni della pressione di stampaggio a iniezione utilizzando dati avanzati sui materiali
•Cliente: SABIC
•Paese: India
•Industria: prodotti chimici/materiale plastico/produzione di metalli
•Soluzione: Moldex3D Professional, Flow, Pack, Cool, Warp, BLM, Machine Mode
SABIC è un leader globale nella chimica diversificata con sede a Riyadh, in Arabia Saudita.
Produce su scala globale nelle Americhe, Europa, Medio Oriente e Asia Pacifico, realizzando tipi di prodotti nettamente diversi: prodotti chimici, materie plastiche e materie plastiche ad alte prestazioni, agronutrienti e metalli. La divisione Specialties di SABIC produce prodotti altamente differenziati che includono resine e composti termoplastici speciali per ingegneria, compositi, termoindurenti e additivi e soluzioni di produzione additiva.
Offrendo un insieme distinto di proprietà fisiche multifunzione per servire un'ampia gamma di settori, il portafoglio del marchio comprende resine ULTEM™, composti LNP™, resine NORYL™, copolimeri LEXAN™ e resine EXTEM™.
I Global Application Technology Centers di SABIC sfruttano i loro ingegneri di prodotto e le competenze nella lavorazione dei materiali per supportare i clienti con richieste specifiche di progettazione, sviluppo di applicazioni e test per aiutare a portare i loro prodotti innovativi sul mercato prima.
Il team dei dati sui materiali utilizza laboratori di caratterizzazione dei materiali all'avanguardia, capacità di ingegneria predittiva e test a livello di parte per convalidare i dati sui materiali utilizzati per la progettazione delle applicazioni.
Sommario
•Le recenti tendenze del settore indicano che le applicazioni di stampaggio a iniezione stanno diventando sempre più complesse con l'uso di resine altamente personalizzate. Ciò richiede lo sviluppo di metodi analitici avanzati, modelli di materiali e capacità del risolutore CAE per una simulazione di processo accurata
•I risultati della simulazione CAE devono essere accurati in modo da poter prendere decisioni sicure sulla progettazione di parti, stampi, macchine e processi
•SABIC ha sviluppato un approccio sistematico e passaggi codificati che replicano lo scenario di stampaggio reale in CAE e ha migliorato la caratterizzazione della viscosità della resina. Ciò ha aiutato SABIC a prevedere le pressioni di iniezione entro il 10% del valore effettivo per le resine valutate
•Il tutoo permette al team di progettazione di prendere decisioni sicure durante lo sviluppo di parti, stampi e processi, riducendo le rilavorazioni, accelerando i tempi di sviluppo e ottimizzando i costi di sviluppo.
Sfide
Quando si replica un problema complesso multidominio in CAE, dobbiamo guardare in modo olistico ai modi di rappresentare la parte, l'utensile, il materiale e la macchina come condizioni al contorno appropriate, quindi come insieme delle parti e dei sistemi coinvolti.
Dobbiamo esaminare aspetti critici come la misurazione della temperatura superficiale dello stampo, la temperatura di fusione e ridurre la loro incertezza mentre li utilizziamo come input in CAE.
Dobbiamo assicurarci che attraverso uno studio reologico dettagliato nello stampo venga studiata l'influenza della velocità di iniezione sulla pressione per stampare il pezzo portando alla derivazione della finestra di stampaggio ottimale.
La perdita di pressione che si verifica nel cilindro della vite della macchina può essere significativa e dovrebbe essere rilevata attraverso uno studio appropriato.
Tutti questi studi forniscono informazioni sul processo e gettano le basi per l'impostazione del modello in ambiente CAE.
Ciò contribuirà a rendere il modello CAE rappresentativo del processo effettivo costituito dalla parte, dal materiale, dai canali di flusso, dalle condizioni di temperatura iniziali di fusione e stampo (Digital Twin).
Tradizionalmente, durante la caratterizzazione della viscosità del materiale polimerico, ciò viene fatto includendo l'influenza della temperatura e della velocità di taglio.
L'influenza della pressione sulla viscosità non viene considerata.
La pressione aumenta notevolmente la viscosità del polimero e questo è molto rilevante per le resine amorfe.
Nel materiale amorfo, la Tg aumenta all'aumentare della pressione subita dal polimero.
Ciò si verifica quando il volume libero si riduce con l'aumento della pressione, il che aumenta ulteriormente la viscosità.
Nel metodo applicato, abbiamo tenuto conto dell'effetto della pressione sulla viscosità, rappresentato dal parametro D3 nel modello di viscosità Cross-WLF utilizzato.
Fig A
La Fig. A sopra mostra il divario nella pressione di iniezione tra lo stampaggio sperimentale e il CAE, dove il file del materiale qui non ha D3 (dipendenza dalla pressione).
Soluzioni
Il team SABIC ha affrontato questo problema in modo sistematico.
1)Caratterizzazione del materiale – Oltre ai parametri Cross-WLF convenzionali, anche il termine di dipendenza dalla pressione, D3 nel modello Cross-WLF è fondamentale per effettuare una stima accurata del comportamento del flusso della resina ad elevate pressioni di iniezione. SABIC ha una metodologia per la misurazione di D3.
2)Configurazione sperimentale – Dopo aver pre-essiccato il materiale secondo le impostazioni richieste utilizzando un essiccatore ad assorbimento e aver ottimizzato le impostazioni del processo utilizzando tecniche di stampaggio scientifiche, SABIC ha eseguito le impostazioni per un'ora (60 cicli) per consentire al processo di stabilizzarsi e ottenere un equilibrio prima di effettuare qualsiasi misura.
3)Registrazioni dei dati – Gli input come la temperatura del fuso e la temperatura dello stampo vengono misurati mediante spurgo e controllo sulla superficie della cavità mediante sonde termiche. Tutti i parametri di movimento della vite come corsa e velocità vengono acquisiti con una curva continua di variazione della pressione rispetto a t.r. tempo dalla macchina.
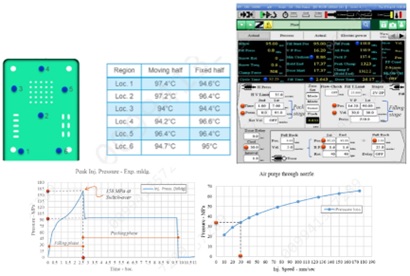
4)Modello CAE – La parte e il sistema di alimentazione, che include il gate, il canale freddo e la zona calda, sono stati tutti modellati utilizzando elementi 3D, condizione fondamentale per un’analisi ed una simulazione accurata. È stato speso un notevole sforzo per comprendere la sensibilità della mesh del modello su alcuni dei risultati chiave come la pressione e il modello di flusso prima di deciderlo. Per includere la perdita di pressione che si verifica nel cilindro della vite della macchina, la parte anteriore della geometria dell'ugello della macchina è inclusa nel modello del sistema di alimentazione e infine sono integrati con la geometria della parte: tutti questi sono meshati utilizzando elementi 3D, formando così la base per il modello meshato. Vengono anche misurate le prese d'aria progettate nello stampo e le stesse sono modellate nel modello CAE.
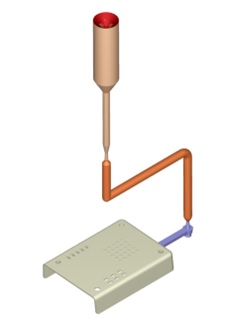
5)Post-elaborazione – La simulazione del processo di stampaggio che prevede uno studio tipico di riempimento e impaccamento è stata eseguita in Moldex3D. Il confronto della pressione di picco tra stampaggio sperimentale e simulazione (CAE), in cui i dati sui materiali utilizzati nella simulazione CAE sono senza D3 nel modello di viscosità, la simulazione è sottostimata di circa il 28,9%. Il confronto della pressione di picco, con l'inclusione di D3 nel modello di viscosità, è notevolmente migliorato e ha un buon accordo con la pressione misurata. La simulazione ora sottostima la pressione di picco misurata del 4,2%.
Benefici
Questo modello ha la rappresentazione più accurata e veritiera rispetto la realtà fisica (Digital Twin).
•La resina ha caratterizzazione reologica migliorata,
•Misurazioni accurate e inclusione della temperatura del fuso e dello stampo,
•Misurazione dettagliata e inclusione dell'ugello della macchina nel percorso del flusso,
•Rendering dettagliato delle trappole d'aria utilizzate nel modello,
•Replicare le impostazioni della macchina come input per il riempimento e l’impaccamento
Tutto ciò si traduce in un modello solido di simulazione CAE che fa ipotesi minime sulle proprietà del fuso e sulle condizioni di stampaggio, fornendoci così dati per prendere decisioni informate.
Conclusioni
L'approccio utilizzato qui durante la conduzione di esperimenti di stampaggio è stato sistematico e fatto con un approccio scientifico.
È stato osservato e documentato che la chiave per ottenere una correlazione di successo tra stampaggio sperimentale e simulazione (CAE) risiede nella caratterizzazione del comportamento del materiale, nella misurazione accurata e nella registrazione dei parametri chiave del processo come la velocità di iniezione, la temperatura di fusione e la modellazione dell'intero percorso di flusso della resina.
Nel dominio della simulazione, è importante sviluppare il modello ad elementi finiti (FE) che rappresenti veramente il più possibile lo scenario del mondo reale.
In questo modo, i risultati della convalida mostrano che è possibile stabilire una buona correlazione nella simulazione dello stampaggio a iniezione per prevedere la pressione di picco.
Questo a sua volta consentirà al team di progettazione di prendere decisioni con sicurezza durante lo sviluppo di parti, stampi e processi. I principali fornitori di materiali a livello mondiale come SABIC possono fornire dati avanzati sui materiali come il coefficiente di viscosità D3, essenziali per previsioni accurate. I dati avanzati sui materiali e la scelta della giusta tecnologia di simulazione aiutano a risparmiare tempo e denaro, ecc.