RIDUZIONE DEL 95% DELLE
LINEE DI GIUNZIONE IN ZONA CRITICA
Caso studio
Estratto dalla laurea magistrale
“CONTENITORI SICURI PER BIOPSIE A SISTEMA CHIUSO” di Alberto Aprà, Politecnico di Torino. A.A. 2020-2021
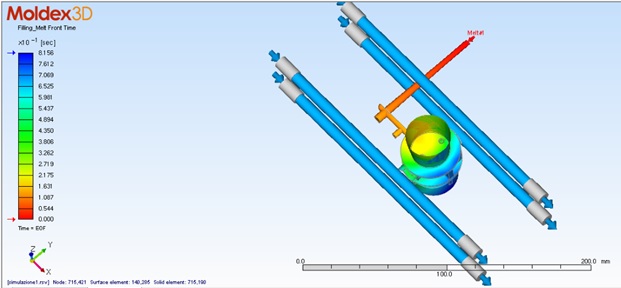
Figura 1: Complessivo del sistema originale con canali di raffreddamento e di iniezione
Lo studio tramite le diverse simulazioni comincia dal design originale, visibile nella figura 1, per andare a ricavare una analisi preliminare delle possibili criticità del sistema.
Come visibile nella figura 2 si possono verosimilmente associare le saltuarie fratture del componente in opera alla presenza di estese linee di giunzione nel cilindro orizzontale cavo.
In queste regioni si ha una serie di fattori che incrementano la fragilità: linee di giunzione ad angoli di incontro piccoli in modulo, presenza di elevati sforzi dati da un altro componente e gli spessori minimi dell’oggetto.
L'obiettivo è quello di andare a migliorare la resistenza meccanica senza impartire modifiche molto dispendiose all’oggetto.
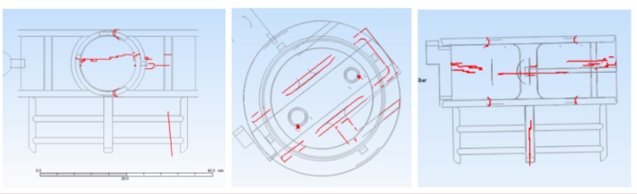
Figura 2: Linee di giunzione ottenute con il punto di iniezione originale
Con contenuti spostamenti del punto di iniezione originale i risultati sono molto simili a quello che si può osservare nella figura 2, poiché se il punto di iniezione è laterale si avrà sempre la divisione del flusso e la successiva riunione nella regione critica centrale.
A titolo di esempio si può osservare nella figura 3 lo spostamento verticale (a sinistra) e una differente geometria del punto di iniezione (a destra) che, in entrambi i casi, portano alla generazione di linee di giunzione simili, se non più critiche, rispetto al sistema originale
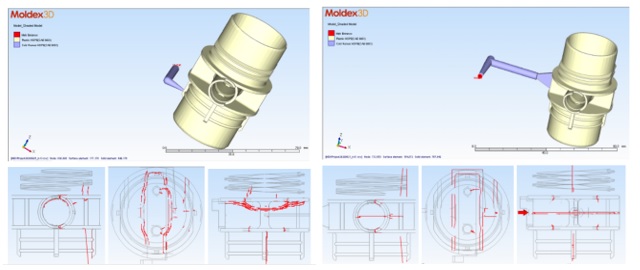
Figura 3: Punti di iniezione e linee di saldatura risultanti di due sistemi con piccole variazioni all’iniezione
Tramite l’animazione del riempimento dello stampo è possibile visualizzare facilmente che l’origine del problema è la regione forata che separa i supporti verticali (necessari per l’estrazione) e il cilindro orizzontale, come visibile nella figura 4.
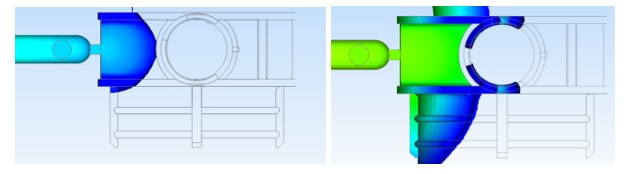
Figura 4: Visualizzazione, con il punto di iniezione originale, del flusso di fuso che si divide e riunisce andando a formare le linee di giunzione
Le modalità più semplici per aggirare il problema senza modifiche sostanziali dell’oggetto definitivo sono di posizionare il punto di iniezione in modo che questa regione sia riempita senza che il flusso si divida per poi riunirsi nella regione a metà altezza.
Una prima modalità è quella di iniettare dall’interno su uno dei due cerchi orizzontali, ma ciò porta comunque ad ottenere delle linee di giunzione all’interno del cilindro orizzontale, come visibile nella figura 5.
Tuttavia, esse, essendo nella porzione inferiore, meno sollecitata e che presenta uno spessore superiore, fanno in modo che questa possibilità risulti considerabile come possibile soluzione.
Il problema principale di questa opzione è l’impossibilità di applicazione sullo stampo originale, andandola a rendere oltre che non perfettamente risolutiva anche molto costosa.
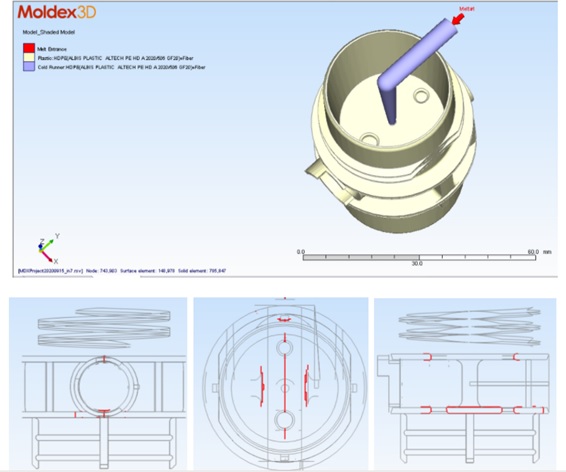
Figura 5: Punto di iniezione sul cerchio superiore e linee di giunzione risultanti
Nonostante questa opzione risulti inapplicabile allo stampo è comunque interessante valutarla in modo più approfondito specialmente per quanto riguarda l’angolo di incontro dei flussi che portano alla formazione delle weld lines.
Infatti, si può notare con un semplice confronto, visibile nella figura 6, che il modulo minimo degli angoli è decisamente inferiore nel caso del punto di iniezione originale, cosa che porta conseguenti proprietà meccaniche peggiori.
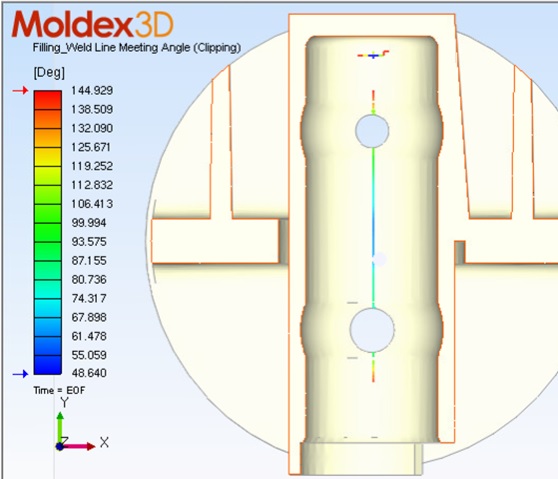
Figura 6: Confronto tra gli angoli di incontro con il punto di iniezione originale (sopra) e spostato sul cerchio orizzontale superiore (sotto)
Le linee di giunzione non possono essere completamente eliminate ma con il punto di iniezione ottimale si può ridurre la loro presenza nella regione critica di oltre il 90% in lunghezza ed evitare completamente che esse si posizionino nelle regioni critiche.
Il punto di iniezione ottimale, senza modifiche al design dell’oggetto è rappresentato nella figura 7.
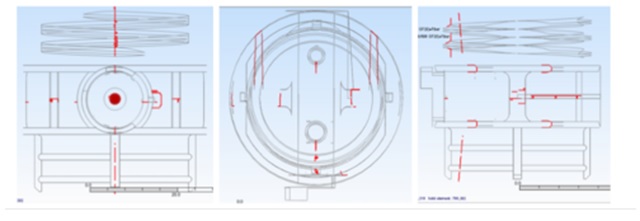
Figura 7: Punto di iniezione che fornisce i risultati migliori
Altri due sistemi con contenute modifiche alla geometria originale, per ottenere un differente flusso del fuso sono state indagate in quanto meno costose. Entrambe forniscono risultati che non riducono in modo così marcato la quantità di linee di giunzione nel cilindro orizzontale, ma riescono semplicemente a farle apparire in regioni meno critiche. Entrambe sono visibili nella figura 8.
Figura 8: Punti di iniezione con modifiche contenute dell’oggetto e weld lines originate