Simulazione con Moldex3D e determinazione del progetto ottimale del prodotto nel più breve tempo possibile

Albert Hu, Technical Manager presso product division di CoreTech System (Moldex3D)
Un processo generale di produzione per prodotti in plastica coinvolge molte fasi, tra cui il progetto del prodotto in senso stretti è in progetto di tutta l’infrastruttura per produrlo strutture (stampo, attrezzature, utensili per stampi e sistema di stampaggio).
Se il design del componente non è abbastanza appropriato, causerà difficoltà per la produzione nelle fasi successive e più sforzo di comunicazione delle modifiche di progettazione e definizione finale della parte e dello stampo.
Questo articolo si concentra su come, durante la fase di progettazione del prodotto in plastica, utilizzare la simulazione CAE per avvicinarsi al progetto ottimale, prevenire potenziali problemi in avvio e garantire una produzione definitiva regolare.
Di solito ci sono ispezioni Design for Manufacturing (DFM) nella fase di progettazione del prodotto.
Normalmente, i capisaldi DFM includono i valori di restringimento dei materiali plastici, gli angoli di sformo, e particolare attenzione nelle zone con nervature o accumulo di spessori.
Viene quindi suggerita una particolare attenzione allo spessore della parte, il progetto delle nervature e delle bugne, riferiti alle tolleranze di progetto assegnate. Queste ispezioni delle specifiche possono essere completate tramite features CAD o ispezione manuale.
Ad esempio, anche se normalmente cerchiamo uno spessore uniforme della parte, quando sono richieste variazioni di spessore, si suggeriscono varianti come mostrato in Fig. 1.
D'altra parte, la Fig. 2 e 3 mostrano ipotesi di progetto suggerite per nervature e bugne mostrati in Fig. 4.
Tuttavia, lo stampaggio a iniezione di materie plastiche è un processo dinamico, quindi lo stesso materiale plastico realizzato da diversi produttori e con modelli diversi può fare grandi differenze (importanza delle caratteristiche del materiale).
Inoltre, diverse macchine a iniezione hanno diverse risposte in fase di stampaggio e diverse condizioni di processo influenzeranno le qualità del prodotto.
Di conseguenza, problemi si possono verificare durante la produzione reale anche quando si è fatta particolare attenzione alla fase “manufacturing” (DFM).
Ad esempio, sebbene abbiamo seguito i suggerimenti di progettazione di spessori e nervature, i prodotti finali possono ancora avere comunque una deformazione eccessiva, una bassa resistenza meccanica strutturale, difetti superficiali o persino un riempimento incompleto o non possono essere stampati correttamente con i parametri assegnati.
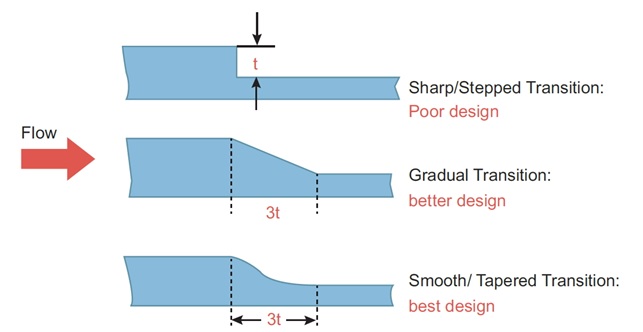
Fig. 1 I disegni suggeriti per le variazioni di spessore
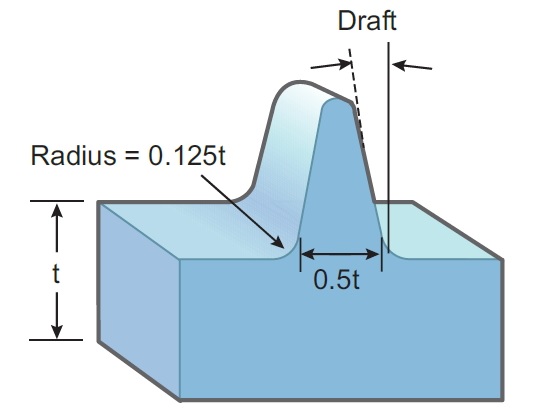
Fig. 2 I disegni delle dimensioni delle nervature suggeriti
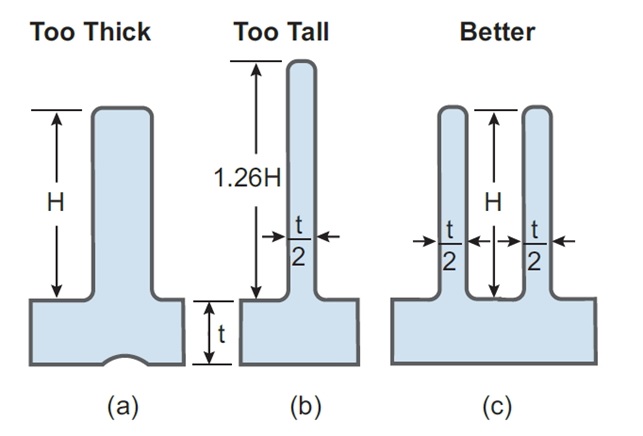
Fig. 3 Disegni equivalenti di una costola
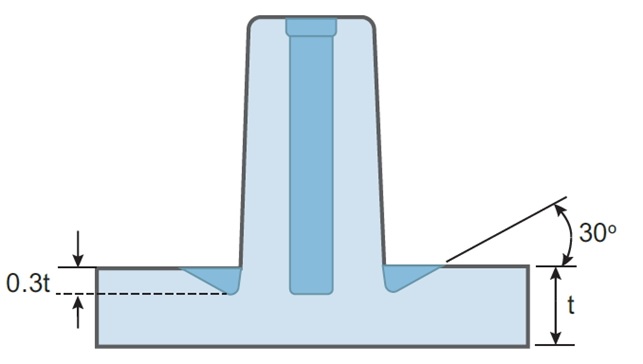
Fig. 4 Disegni delle feature del boss con il riferimento dello spessore della parte
Pertanto, non ci sono regole perfette a priori, per tutti i progetti di prodotto, ma ci può essere un suggerimento migliore da considerare come raccomandazioni da prendere in considerazione nella fase iniziale del progetto del componente e l’assegnazione dei parametri di stampaggio.
Oltre a utilizzare il software CAD per procedere alle ispezioni DFM, l'analisi CAE può ulteriormente aiutare a regolare le dimensioni geometriche, convalidare i progetti in modo ottimizzato (DOE) e risolvere i problemi in modo iterativo per passi.
Tali modifiche e convalide iterative del progetto può essere un processo prolisso e, per superare questa difficoltà, Moldex3D SYNC dal 2021 supporta gli strumenti di ottimizzazione della geometria, aiutando gli utenti a semplificare notevolmente il flusso di lavoro di analisi CAE.
Con questo strumento, i progetti con tutte le variazioni di dimensione e i corrispondenti risultati dell'analisi CAE possono essere completati attraverso diversi semplici passaggi in un ambiente CAD famigliare.
Il seguente caso di un connettore dimostra come utilizzare Moldex3D SYNC per ottenere i disegni geometrici ottimizzati.
La Fig. 5 mostra il modello di prodotto originale che ha superato l'ispezione DFM e la Fig. 6 è il risultato iniziale della simulazione.
Come illustrato nell'analisi del flusso, lo squilibrio del flusso si verifica su entrambi i lati del connettore.
La Fig. 7 mostra il risultato dell'analisi della deformazione e la deformazione causerà un problema per l'intestazione del pin quando viene inserita, che deve essere migliorata prima della produzione. Dalla sezione trasversale del design originale, entrambi i lati hanno uno spessore diverso e l'estremità più spessa dovrebbe essere leggermente modificata.
Sebbene dimostri che la modifica dello spessore può migliorare lo squilibrio del flusso e la deformazione (è richiesta anche l'analisi strutturale), non possiamo determinare le dimensioni modifica necessaria per ottenere lo spessore ottimale e sarà molto dispendioso in termini di tempo analizzare ogni progetto con spessore diverso (Fig. 8). Con lo strumento di ottimizzazione della geometria in Moldex3D SYNC, possiamo specificare rapidamente i parametri variati e impostare tutti i gruppi di analisi e quindi ottenere una serie di risultati di analisi ottimali (Fig. 9), in cui la deformazione è stata migliorata mentre il fronte del fuso ha un comportamento corretto nel suo fluire.
Fig. 5 La custodia del connettore e la sua sezione trasversale
Fig. 6 I risultati dell'analisi CAE mostrano uno squilibrio di flusso su entrambi i lati.
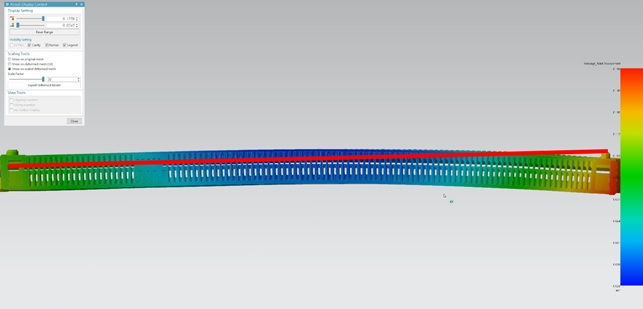
Fig. 7 La deformazione della deformazione causata dallo squilibrio del flusso
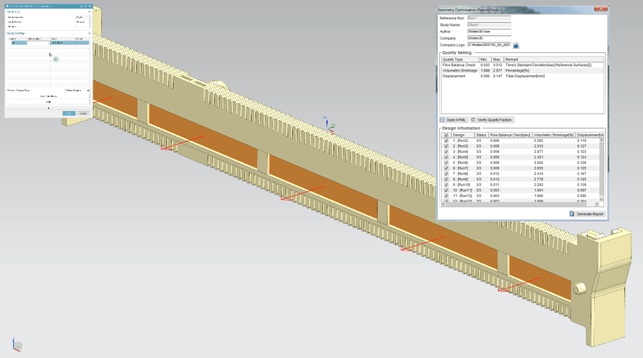
Fig. 8 Impostazione dell'intervallo di variazione dei parametri geometrici e generazione di tutti i gruppi di analisi contemporaneamente
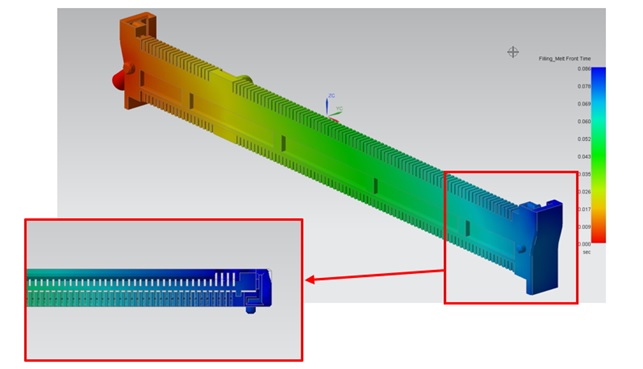
Fig. 9 In uno dei set di analisi, il fronte di fusione di entrambi i lati coincide quasi alla fine
L'esempio precedente mostra che le ispezioni DFM statiche non possono evitare al 100% i problemi causati dal processo di produzione dinamico, ma l'analisi di stampaggio CAE può aiutare parecchio e indirizzare il progettista sulla strada migliore.
Lo strumento di ottimizzazione della geometria Moldex3D SYNC può semplificare ulteriormente il flusso di lavoro di analisi attraverso la perfetta integrazione tra CAD e CAE.
Se consideriamo i risultati dell'analisi come parte della modellabilità del prodotto, la combinazione di CAD e CAE può migliorare efficacemente l'efficienza di progettazione del prodotto e ridurre in modo sostanziale il time-to-market.