Combinazione del sistema PU FOAMAT con la simulazione CAE per una previsione accurata della formazione di schiuma PU

Joe Wang, Manager presso material measurement Center di CoreTech System (Moldex3D)
La schiuma di poliuretano (schiuma PU) è un materiale termoindurente comune utilizzato nella produzione automobilistica.
È un materiale poroso, a bassa densità e ad alta resistenza, e queste caratteristiche rendono la schiuma di poliuretano un materiale popolare che è utilizzato per applicazioni leggere e isolanti.
Le applicazioni più comuni includono componentistica per autoveicoli, sedili, interni e parti sotto-cofano e packaging per componenti elettronici a bordo.
Le proprietà finali desiderate della schiuma possono essere modificate attraverso la scelta di componenti specifici insieme alle quantità richieste e alle condizioni di processo, rendendone un materiale versatile di scelta in molti settori industriali.
Inoltre, a causa della natura termoindurente del polimero, può resistere a temperature più elevate senza sciogliersi.
Sebbene il poliuretano abbia i vantaggi sopra menzionati, ci sono alcune difficoltà tecniche nella lavorazione della schiuma di poliuretano che devono essere superate.
In realtà, la posizione della schiuma all'interno della parte non è di facile indentificazione e accesso.
Spesso i difetti della parte come grandi vuoti dovuti a riempimento incompleto e schiumatura imperfetta possono essere identificati solo dopo che lo stampo è stato realizzato e la parte è stata prodotta.
Anche altri fattori, come le posizioni e le condizioni di sfiato, hanno un'influenza significativa sulla qualità della parte.
Inoltre, una grande quantità di materiali poliuretanici viene “sprecata” durante il processo di schiumatura e deve essere ridotta o riciclata.
La simulazione CAE viene comunemente utilizzata per rilevare i comportamenti dinamici nel processo di riempimento e schiumatura dello stampo della schiuma di poliuretano (schiuma PU) e per mettere a punto le corrette condizioni di processo e ottimizzare i progetti del prodotto.
Gli approcci di Moldex3D sono di combinare strettamente lo sviluppo del modello con la fase sperimentale per comprendere meglio il fenomeno della schiumatura, parametrizzare e modificare il modello del materiale e convalidare i modelli una volta sviluppati.
La caratterizzazione dei materiali dovrebbe essere molto accurata per essere in grado di prevedere le proprietà di riempimento, espansione della schiuma, polimerizzazione e schiuma finale, che sono ancora piuttosto impegnative.
Alle difficoltà di simulazione esistenti si aggiungono proprietà di reazione PU poiché la reazione è veloce e il volume cambia costantemente.
L’aumento della schiuma, la temperatura di reazione, la pressione di aumento, la polimerizzazione e la viscosità devono essere misurate per riflettere con precisione i parametri fisici durante la formazione della schiuma.
Il poliuretano (isocianato di poliolo) è una schiuma soffiata chimicamente, in cui l'agente schiumogeno CO2 viene prodotto tramite reazione chimica tra isocianato e acqua.
Allo stesso tempo, l'isocianato reagisce anche con il poliolo in modo concorrente che genera il polimero.
È necessario un nuovo modello cinetico che disaccoppia queste due reazioni di completamento.
Anche se il nostro approccio si basa sul precedente lavoro di letteratura, è unico in quanto costituisce un nuovo modello cinetico, che segue un formalismo matematico semplificato che disaccoppia le reazioni di schiuma e polimerizzazione.
Inoltre, l'approccio è completamente fondato su dati sperimentali, dove l'isocianato è sempre in eccesso e non influenza la cinetica di reazione.
In questo studio, abbiamo utilizzato FOAMAT (Fig. 1), un sistema universale di qualificazione della schiuma, per studiare a fondo le caratteristiche della schiuma PU. I dati sperimentali vengono quindi dotati di un modello di materiale appropriato, generando parametri di modellazione.
I parametri del materiale vengono successivamente utilizzati nelle simulazioni e, utilizzando un contenitore specifico (contenitore a temperatura), i risultati sperimentali risultanti (altezza e temperatura) vengono confrontati con i risultati delle simulazioni.
Attualmente il software di simulazione PU è ancora poco diffuso, con un'enorme domanda di mercato e una potenziale base di clienti, in particolare nel settore automobilistico, aerospaziale e sportivo per applicazioni leggere.
Fig. 1 Schema del sistema FOAMAT di qualificazione della schiuma
Abbiamo effettuato indagini sperimentali sui parametri fisici durante la formazione della schiuma utilizzando FOAMAT 285 e materiale PU con il nome in codice BE.
La materia prima PU ha le seguenti caratteristiche specificate a 23 °C: rapporto di miscelazione poli-isocianato 100:63 p/p, contenuto di acqua 0,60 wt%, tempo crema 9s, tempo di lievitazione 32 e densità di lievitazione libera 172g/L. Dato il tempo di attivazione di 9s, questo materiale PU è estremamente veloce. Il materiale inizia a reagire e schiuma non appena i due reagenti vengono miscelati, aumentando la difficoltà di misurazione.
I reagenti sono stati miscelati in base alla quantità specificata utilizzando la bilancia di ponderazione e la perdita di peso dovuta al trasferimento dal contenitore al contenitore a temperatura avanzata (ATC) è stata accuratamente documentata, in modo da ottenere i parametri del materiale sempre più accurati.
L'ATC fornisce un ambiente a temperatura controllata in modo da poter determinare l'effetto della temperatura sulla velocità di reazione.
La dipendenza di temperatura è fondamentale per la simulazione poiché durante la produzione effettiva viene utilizzata una temperatura relativamente elevata.
Gli esperimenti sono stati condotti a 30, 40, 50 e 70ºC. Abbiamo osservato che, a causa delle temperature costanti, i risultati delle misurazioni dell'ATC sono molto più riproducibili di quelli misurati in contenitori di prova non termostatati.
È stata misurata anche la temperatura di reazione.
La temperatura interna massima è stata misurata posizionando la termocoppia nel terzo inferiore della schiuma.
Il profilo di aumento è stato registrato con sensore a ventola a ultrasuoni brevettato internamente, appositamente progettato per misurare la distanza dall’elemento in schiuma con elevata precisione.
La polarizzazione dielettrica è un nuovo parametro di misura che fornisce informazioni sui processi elettrochimici che si verificano durante la formazione della schiuma.
La polarizzazione dielettrica è essenzialmente causata da molecole simili a catene con un grande momento di dipolo a causa delle loro estremità polari (OH, NCO).
La formazione di catene precede la reazione di reticolazione che alla fine sopprime tutta la mobilità del dipolo mediante polimerizzazione.
Quindi, il valore di polarizzazione dielettrica può rivelare il grado di polimerizzazione durante il corso della reazione e quindi la stabilizzazione della schiuma (Fig. 2).
La viscosità è stata misurata utilizzando un reometro a piastre parallele MCR502.
Il campione è stato prima trattato con setaccio molecolare per rimuovere l'acqua.
Il materiale schiumogeno non segue la regola di Cox-Merz; pertanto, testiamo la sua reologia usando il taglio costante nella geometria della piastra parallela.
È stato dimostrato che la viscosità di taglio era indipendente dalla velocità di taglio a 0,01 s-1 e inferiore.
Inoltre, è stato dimostrato che variando lo spazio tra le piastre (da 0,5 mm a 2 mm) è emerso che c'era un piccolo effetto sulla viscosità misurata rispetto alla variazione di viscosità nel tempo, e quindi non abbiamo tentato di correggere i dati per lo slittamento.
Le misurazioni sono state effettuate (a 0,01 s-1 e con uno spazio di 1 mm) a cinque temperature da 30 ~ 50 ° C con incrementi di 10 ° C.
Fig. 2 I dati sperimentali tipici della serie ELASTOFOAM CI 4510/136/LD per altezza di salita, tasso di aumento, pressione di aumento e polarizzazione dielettrica sono registrati simultaneamente e vengono visualizzati in un grafico.
La seguente reazione chimica si verifica quando si mescolano le materie prime (isocianato, poliolo e acqua):
Reazione di gelificazione: La reazione chimica tra isocianato e poliolo produce legame uretanico. La reazione di polimerizzazione del legame uretano procede alla produzione del polimero poliuretanico
Reazione di soffiaggio: Allo stesso tempo, la reazione chimica tra isocianato e acqua produce gas di anidride carbonica
Qui, abbiamo usato due equazioni di velocità separate per descrivere le velocità di reazione di schiumatura e reticolazione concorrenti.

Al fine di ottenere l'influenza della temperatura sulle proprietà schiumogene, gli esperimenti sono stati condotti a diverse temperature.
L'altezza di schiumatura e i risultati della costante dielettrica sono mostrati in Fig. 3 e 4, così come le immagini dei campioni effettivi delle misurazioni sono mostrate in Fig. 5.
In tutti i casi, c'è una forte dipendenza dalla temperatura relativamente alle proprietà schiumogene.
L'altezza di schiumatura è proporzionale alla temperatura.
La densità della schiuma ascendente in qualsiasi momento è ottenuta dal rapporto di espansione e dalla conversione schiumogeno della schiuma PU.
Fig. 3 Altezze di schiumatura a diverse temperature
Fig. 4 Costanti dielettriche a diverse temperature
Fig. 5 Immagini di esperimenti di schiumatura condotti a temperature diverse.
La schiumatura e la polimerizzazione del poliuretano sono state studiate da numerosi ricercatori.
L'importanza di avere equazioni di velocità separate che descrivano queste due reazioni concorrenti è evidenziata in Fig. 6.
Dalla Figura 6 è chiaro che la reazione di schiumatura ha una velocità di reazione più veloce rispetto alla reazione di polimerizzazione.
I risultati sono certamente coerenti con i risultati riportati dal laboratorio nazionale Sandia.
In generale, la reazione di schiumatura è progettata per avere una velocità di reazione più veloce rispetto alla reazione di polimerizzazione per l'ovvia ragione che se la reazione di polimerizzazione è troppo veloce, la viscosità è troppo alta per la formazione di bolle.
Fig. 6 Confronto tra cinetica schiumogeno e cinetica polimerizzante.
La Fig. 7-9 mostra la validazione sperimentale dell'altezza e della temperatura della schiuma di poliuretano in ATC.
La temperatura dello stampo e la temperatura di fusione sono impostate su 30 oC.
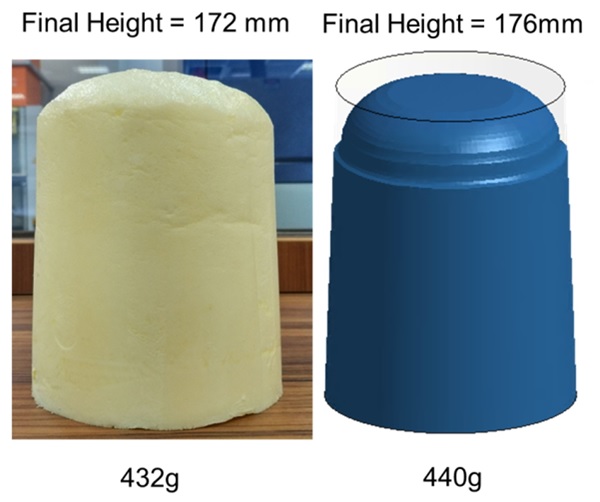
Fig. 7 Confronto dei risultati sperimentali (a sinistra) e numerici (a destra) dell'altezza finale della schiuma nell'ATC.
La Figura 7 mostra il confronto tra i risultati numerici e sperimentali dell'altezza finale della schiuma in ATC.
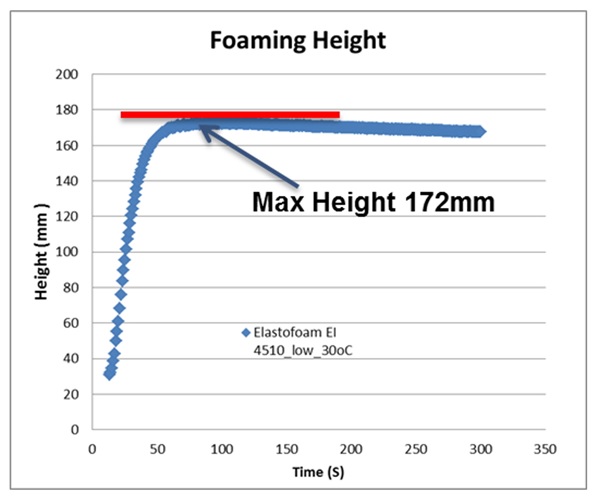
Fig. 8 Confronto dell'altezza simulata della schiuma in funzione del tempo e dell'altezza massima della schiuma negli esperimenti.
La Figura 8 mostra la curva di storia dell'altezza della schiuma dalla simulazione e i risultati sperimentali dell'altezza finale della schiuma come confronto.
In entrambi i casi i risultati della simulazione si adattano agli esperimenti.
Fig. 9 Confronto dei risultati sperimentali (linea blu) e numerici (linea rossa) per la temperatura in funzione del tempo.
La Fig. 9 mostra il confronto dei risultati sperimentali e numerici per la curva della storia della temperatura.
Poiché le reazioni PU sono reazioni esotermiche, la temperatura del sistema aumenta nel tempo. I risultati della simulazione della temperatura sono vicini a quelli sperimentali.
Infine, inseriamo i parametri del materiale PU misurati nel modulo di simulazione Moldex3D, ottimizzando i relativi parametri di progettazione e processo, come la progettazione delle barre riscaldanti, l'impostazione della temperatura dello stampo, il volume di iniezione PU, il design e l'impostazione dello sfiato e così via.
La parte di interessante è componente di un volante.
Il volume della parte è di circa 933 cc.
Nelle condizioni di processo, la percentuale di volume di riempimento parziale è del 35% in 3,5 secondi.
La temperatura dello stampo è di 50°C, flusso di ingresso a 25°C.
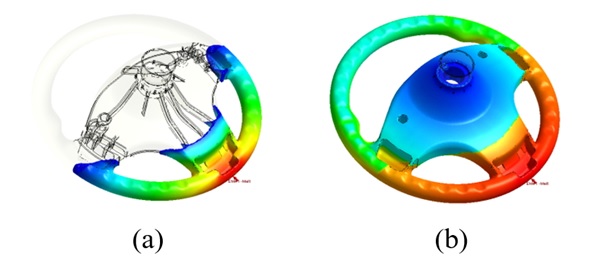
Fig. 10 Fusione frontale a (a) 35% parziale e (b) al termine della schiumatura.
La Fig. 10 mostra il fronte fuso del poliuretano espanso.
In primo luogo, il fuso di poliuretano inizierà a riempirsi lungo il fondo della cavità a causa della gravità. Quando il riempimento raggiunge il 35% della cavità, il gas CO2 verrà rilasciato dalla reazione del poliuretano e la viscosità del polimero aumenterà a causa della reazione di gelificazione. Nel frattempo, il calore di reazione della reazione esotermica verrà rilasciato per aumentare la temperatura della cavità. Di conseguenza, sempre più gas CO2 vengono rilasciati nella fusione polimerica in condizioni di temperatura relativamente elevata. Alla fine, la schiuma di poliuretano riempirà completamente la cavità.
Fig. 11 Distribuzione della densità a (a) 35% riempito parzialmente e (b) al termine della formazione di schiuma.
La Fig. 11 mostra la distribuzione della densità del poliuretano espanso.
La distribuzione della densità rivela l'effetto di espansione durante il processo di schiumatura.
Quando la conversione della schiuma è più alta, più gas CO2 viene prodotto. Provoca il maggiore volume di schiuma di poliuretano e la densità più leggera.
Conclusioni
In questo articolo, abbiamo condotto indagini sperimentali sulle proprietà del materiale PU necessarie per un'accurata simulazione PU.
Abbiamo utilizzato FOAMAT 285, un sistema universale di qualificazione della schiuma per misurare i parametri fisici durante la formazione della schiuma come l'altezza di aumento della schiuma, la temperatura di reazione, la pressione di aumento, l'indurimento e la viscosità.
I parametri fisici della schiuma misurati vengono quindi adattati utilizzando modelli di materiali adatti e utilizzati nella simulazione della schiuma chimica PU in condizioni di processo ottimali durante la formazione di schiuma.
Infine, con il nuovo modulo avanzato di simulazione della schiumatura del poliuretano di Moldex3D, possiamo comprendere appieno il comportamento dinamico del materiale in poliuretano espanso sia nella fase di riempimento che di schiumatura.
Ancora più importante, l'analisi approfondita della schiuma di poliuretano consente agli utenti di evitare tentativi ed errori che successivamente portano a sostanziali riduzioni dei tempi e dei costi di produzione.