Si considerano due parti di illuminazione,fatte dello stesso materiale, sono stati entrambe realizzate nello stesso stampo per ridurne i costi.
Tuttavia, le loro dimensioni erano molto diverse, portavano ad una situazione di sbilanciamento nel il riempimento delle due cavità.
Utilizzando Moldex3D si sono potute prevedere difficoltà in fase di riempimento (esitazioni e short-shots), improvvisi picchi di pressione, oltre a valutare al meglio le fasi di impaccamento successive al riempimento (congelamento dei gates).
Con Moldex3D è stato possibile dimensionare correttamente i canali della matarozza e le dimensioni degli ugelli per ottenere il miglior bilanciamento, evitando stress non voluti nel materiale e differenze di densità, che potessero indurre contributi aggiuntivi alla deformazione.
Così facendo si è potuto garantire un livello di planarità nel rispetto delle tolleranze richieste dal progetto e corretti valori per l’accoppiamento.
Inoltre, si è ottenuto un alto livello di efficienza nel ciclo di produzione, riducendo notevolmente il tempo di ciclo, aumentando produttività e riducendo i costi.
Gli obiettivi dell’analisi
• Bilanciare e completare il processo di riempimento al tempo stesso per entrambe le cavità
• Garantire le prestazioni del sistema stampo (la configurazione ed il dimensionamento sia della matarozza sia degli ugelli
• Miglioramento dell’efficienza del circuito di raffreddamento (forma e dimensione).
• Massimo contenimento della deformazione risultante
• Rispetto delle tolleranze di progetto (in particolare la planarità)
Moldex3D fornisce le analisi differenziate per le varie fasi di riempimento, impaccamento, raffreddamento, e deformazione, in diversi scenari di progetto (modifica della forma e dimensione del sistema di alimentazione e raffreddamento per migliorare tempo di riempimento, tempo di ciclo, efficienza del circuito di raffreddamento, nonché ridurre al minimo le deformazioni)
Benefici ottenuti
• Riduzione del tonnellaggio richiesto (forza di chiusura dello stampo) alla fine dell’impaccamento (post-compressione) da 225 tonnellate a 175 tonnellate.
• Riduzione del costo intrinseco di produzione (utilizzo di una macchina di stampaggio più piccola)
Perfetto riempimento delle due cavità con un tempo accettabile (1,28 s) - Rapporto di 1.07 s e 1.28 s per la cavità più piccola e più grande
• Ottimizzazione del progetto relativo al sistema di raffreddamento che ha ridotto il tempo di ciclo di circa il 12% con miglioramento globale del sistema stampo
• Planarità della parte più piccola migliorato del 2,56% e della parte più grande del 6,18%, in rispetto della tolleranza di progetto richiesta
• Risparmio totale di $ 11.500 sia sull’approntamento dello stampo sia sulle campionature.
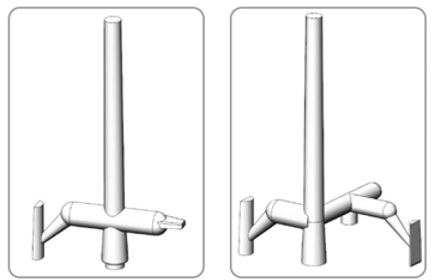
Fig.1
Argomento dello studio
Si sono raggiunti gli obiettivi di ridurre il costo delle parti, sia riducendo la dimensione dello stampo richiesto attraverso l’ottimizzazione del sistema di alimentazione (runners+gates) e di ridurre il tempo di ciclo, per mantenere la planarità entro limiti di qualità accettabile (tolleranza di progetto), e raggiungere tutti questi obiettivi prima della realizzazione fisica dello stampo in modo che i costi di lavorazione e di campionamento potessero essere ridotti al minimo.
Moldex3D eDesign è stato utilizzato per la meshatura del modello che contiene due cavità differenti dello stampo; la parte più piccola era il supporto scheda LED, mentre quella più grande era il riflettore della luce.
Moldex3D è diventato per il Gruppo Mercer un potente strumento per rilevare e identificare i problemi dovuti ad uno sbilanciamento in fase di riempimento , prima di produrre lo stampo, dimensionando correttamente improvviso la forza di chiusura in fase di impaccamento per indirizzare al meglio la macchina di stampaggio disponibile, definire il tempo minimo di raffreddamento per una corretta estrazione del pezzo, e minimizzare le deformazioni secondo gli assi principali , con particolare riguardo all’asse Y.
Le modifiche includono il layout del sistema di alimentazione e del sistema di raffreddamento come illustrato e spiegato in Fig. 1 e Fig. 2.
Fig 2. A differenza del disegno originale (a sinistra), il disegno revisionato (destra) divide il circuito dei canali di raffreddamento, differenziando la parte superiore ed inferiore (analisi dei transitori termici e differenziazione sui cicli) e aggiunge un canale di raffreddamento per il lato inferiore della parte “più grossa”.
Come dimostrato da risultati della simulazione di Moldex3D, la parte più piccola si riempiva troppo presto rispetto alla parte superiore. Il design rivisto, con modifica sia del runner sia dei gates, rende il percorso di flusso più corretto, quindi il suo tempo di riempimento si confronta in modo accettabile con quello della parte superiore (Fig. 3).
Figura. 3 con Moldex3D si possono definire vari frames a tempi diversi del ciclo di raffreddamento, per verificare correttamente la situazione; al 74% di riempimento (in alto) e, con rivisitazione del progetto, al 96% di riempimento (in basso) mostra che il riempimento sbilanciato per entrambe le cavità è stato risolto.
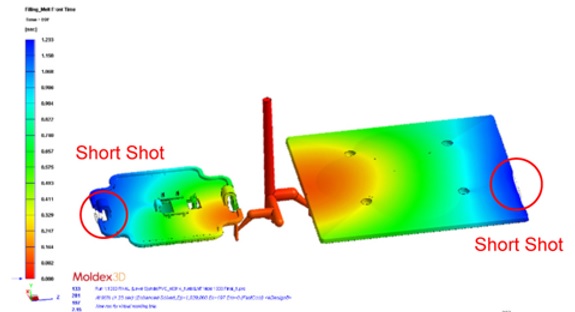
Ci si è poi concentrati sulla problematica legata ad un corretto raffreddamento delle due parti, prima dell’estrazione.
Le modifiche apportate hanno permesso di ridurre il tempo massimo raffreddamento da 21 sec a 18 s tramite ri-progettazione del sistema di raffreddamento in modo ottimizzato. In altre parole, il tempo di ciclo totale poteva essere ridotto.
Per ultimo la deformazione secondo l’asse Y di spostamento che rappresentava la planarità della parte (condizione critica di progetto).
I risultati del progetto originale davano spostamenti massimi di 0,19 millimetri e 0,69 millimetri per le parti più piccole e più grandi, rispettivamente.
Il progetto rivisitato e modificato ha permesso di ridurre gli spostamenti massimi per entrambe le parti più piccole e più grandi di 0,18 millimetri e 0,65 millimetri, in successione.
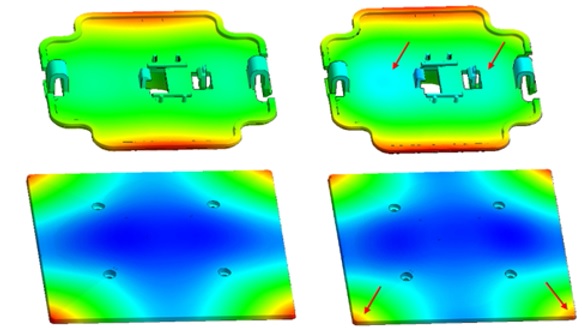
Figura. 4 Le distribuzioni della deformazione secondo l’asse Y
La revisione di progettazione e la successiva verifica del risultato fisico ottenuto in fase di stampaggio ha confermato la capacità di predizione dell’analisi effettuata.
Durante il campionamento stampo iniziale, le condizioni di processo fornite da Moldex3D sono diventati gli input per l'operatore di processo nel settaggio della macchina di stampaggio.
L'operatore di processo ha potuto anche verificare i difetti di riempimento del progetto originale (short-shots) e la bontà del progetto rivisitato. I pezzi stampati in condizione di difettosità, hanno mostrato l’ottimo livello di predizione del difetto da parte di Moldex3D eDesign come mostrato in fig. 5.
Figura. 5 L'iniezione definitiva dei pezzi stampati, come da progetto modificato, per una parte più grande (a sinistra) e una parte più piccola (a destra) hanno identiche posizioni short di colpo con il risultato della simulazione in Fig. 3.