Ottimizzazione del design del canale di raffreddamento conforme della lente LED stampata a iniezione per ridurre lo stress residuo
A cura di Cindy Teng, Ingegnere presso la Divisione Supporto Tecnico
•Cliente: Dongguan University of Technology - Cina
Come prima università cinese a Dongguan, Dongguan University of Technology (DGUT) è stata inizialmente fondata nel 1990 e istituita nell'aprile 1992. Sotto l'autorizzazione del Ministero della Pubblica Istruzione, DGUT ha accolto i suoi primi studenti universitari nel marzo 2002 e ha assegnato i suoi primi diplomi di laurea quattro anni dopo, nel maggio 2006. Inoltre, i nuovi programmi di master di DGUT sono stati autorizzati nell'ambito del Progetto Guangdong nell'agosto 2010. DGUT è stato anche approvato come "Guangdong International Science and Technology Cooperation Base" nel 2012 (Fonte).
Sommario
Nella lente di Fresnel, un lato della lente è una superficie liscia mentre l'altro lato è inciso con cerchi concentrici da piccoli a grandi. Attraverso questi modelli di seghettatura, il passaggio di banda dello spettro (riflessione o rifrazione) può essere raggiunto in un intervallo specificato dello spettro. Realizzare filtri ottici passa-banda in un dispositivo ottico lucido convenzionale è un processo molto costoso.
Le lenti di Fresnel possono ridurre significativamente i costi di produzione del manufatto.
La Dongguan University of Technology ha utilizzato Moldex3D per ottimizzare il design del canale di raffreddamento di una lente di Fresnel per ridurre al minimo lda deformazione e ha progettato con successo un canale di raffreddamento conforme per distribuire uniformemente la temperatura dopo che il prodotto si è raffreddato. L'esperimento è stato adottato per ottenere il miglior processo di produzione di stampaggio e ottimizzare il ciclo totale di stampaggio del prodotto e ridurre lo stress nel componente.
Sfide
•Evitare evidenti difetti di aspetto come linee di saldatura e segni di flusso
•Mantenere una rugosità superficiale inferiore a 20 nm
•Distribuire uniformemente la temperatura dopo il raffreddamento e ridurre il ciclo di stampaggio
•Ridurre lo stress residuo all'interno del prodotto che crea possibili distorsioni.
Soluzioni
Il Dr. Lei Chen ha utilizzato i moduli di raffreddamento conformati Moldex3D per verificare la progettazione di un canale di raffreddamento comune e di un canale di raffreddamento conformato per più istanze.
Con l'ottimizzazione continua della topologia, la temperatura è stata distribuita uniformemente dopo che il prodotto è stato raffreddato e quindi Moldex3D è stato utilizzato per prevedere una corretta azione ottica e lo stress residuo per ottimizzare ulteriormente il processo di produzione.
Il miglior processo di produzione di stampaggio e il canale di raffreddamento possono essere rapidamente ottenuti per abbreviare significativamente il ciclo di sviluppo del prodotto e raggiungere l'obiettivo della collaborazione industria-università-istituto di ricerca.
Benefici
•Risolvere il problema della distribuzione irregolare della temperatura
•Riduzione del tempo di raffreddamento del prodotto da 15 secondi a 13 secondi
•Controllare la temperatura della linea di saldatura e ridurre l'influenza sull'aspetto del prodotto
•Soddisfare i requisiti di precisione delle dimensioni per il prodotto (minima deformazione)
•Ridurre e bilanciare lo stress residuo del prodotto
Caso di studio
Una “lente LED” che si collega con il LED è stata utilizzata per migliorare l’utilizzo della fonte luminosa e l'efficienza della lente.
Con un elevato requisito di qualità superficiale, la lente LED dovrebbe non avere linee di saldatura, segni di flusso o altri difetti superficiali e la sua rugosità superficiale dovrebbe essere inferiore a 20 nm.
In questo studio, il progetto di raffreddamento originale (Fig. 1) porterebbe a temperature irregolari dopo la sezione di raffreddamento, causando una maggiore deformazione, uno stress termico residuo più elevato e un tempo di raffreddamento più lungo.
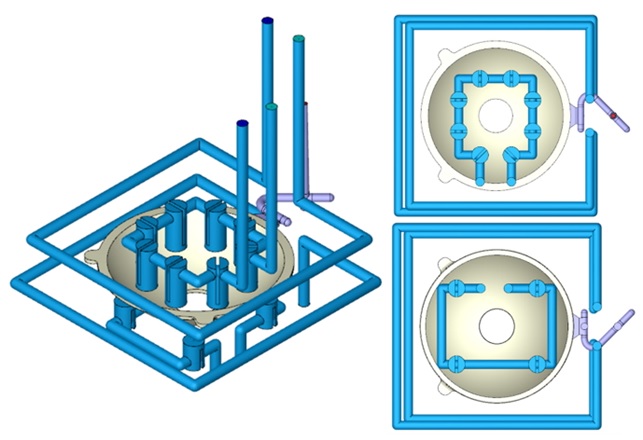
Fig. 1 Design originale del sistema di raffreddamento
La temperatura e la distribuzione dello stress residuo utilizzando il sistema di raffreddamento originale sono mostrate in Fig. 2 e Fig. 3.
Il calore si è stato accumulato al centro della sfera e ci sono state ampie variazioni di temperatura e stress residuo, che si considerano difetti nei componenti ottici.
Fig. 2 Distribuzione della temperatura del sistema di raffreddamento originale
Fig. 3 Stress residuo del sistema di raffreddamento originale
Adottando la stampa 3D (sistemi di raffreddamento sinterizzati), è stato utilizzato un canale di raffreddamento conformato per ottimizzare l'effetto di raffreddamento.
In questo studio si sono sviluppati due diversi tipi di canali di raffreddamento conformati (Fig. 4a e Fig. 4b). Il progetto in Fig. 4a ha sostituito le lame con un canale di raffreddamento conforme, mentre il design in Fig. 4b ha ottimizzato il sistema aumentando un canale di raffreddamento aggiuntivo vicino alla linea di saldatura.
Fig. 4 Design conforme del canale di raffreddamento
Rispetto al progetto originale, la temperatura era più bassa e la distribuzione della temperatura era uniforme dopo la sezione di raffreddamento
(Fig. 5).
Il tempo di raffreddamento stimato è stato ridotto da 15 secondi a 13 secondi (ridotto del 13%). Anche lo stress residuo del prodotto è stato ottimizzato con un canale di raffreddamento conformato (Fig. 6) che ha portato a migliori prestazioni ottiche.
Fig. 5 Distribuzione della temperatura mediante un progetto di canale di raffreddamento conformato
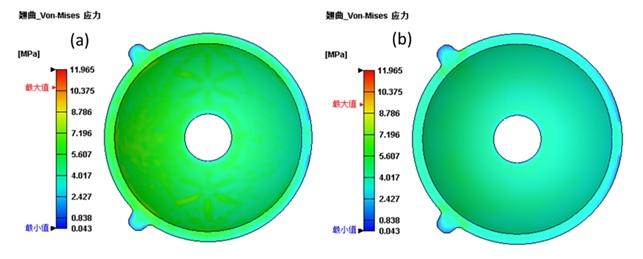
Fig. 6 Stress residuo mediante il progetto di canale di raffreddamento conformato
I prodotti realizzati dall'esperimento pratico di stampaggio utilizzando il polariscopio per determinare la caratteristica ottica sono mostrati in Fig. 7.
Il motivo sfrangiato si è verificato solo nel runner e nel gate, fornendo una buona qualità ottica della lente di Fresnel. L'esperimento pratico di stampaggio ha verificato la fattibilità dei risultati di Moldex3D.
Fig. 7 Lente di Fresnel con polariscopio per determinare la caratteristica ottica
Risultati
Con i risultati dell'analisi Moldex3D, la Dongguan University of Technology ha ottimizzato il progetto del raffreddamento con un canale di raffreddamento conforme, risolvendo il problema dell'accumulo di calore e riducendo il tempo di raffreddamento da 15 secondi a 13 secondi. Anche lo stress residuo e l'indice di rifrazione del prodotto sono stati ottimizzati portando ad una migliore qualità ottica.