Yuuki ha superato i problemi nello stampaggio nel progetto di un’aspirapolvere (componente del serbatoio ad acqua)
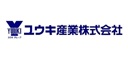
Profilo del cliente
Yuuki è un’azienda giapponese leader mondiale nei prodotti di consumo, fornendo componentistica sia per il settore automobilistico sia elettronico. Possiede vari impianti sia in Giappone, Cina, Vietnam ecc. (Fonte: http://yuuki-g.co.jp/
Premessa
Il gruppo di sviluppo prodotto ed industrializzazione ha rilevato problemi di temperatura nell'ugello del canale caldo nello stampo del serbatoio dell'acqua di un’aspirapolvere a iniezione d'acqua, pertanto il materiale all'esterno non è stato solidificato correttamente. Moldex3D è stato utilizzato per indagare la causa ed esplorare possibili soluzioni al problema. Sfruttando la tecnologia di simulazione del raffreddamento 3D CFD di Moldex3D, Yuuki è stata in grado di convalidare il progetto del sistema di raffreddamento conformato e superare il problema di stampaggio, migliorando la percentuale di successo del 99,7%.
Sfide
•Esitazioni nel flusso di riempimento
•Qualità al di sotto delle aspettative
•Tempo di ciclo lungo
Soluzioni
Moldex3D è stato utilizzato per convalidare l'efficacia di un nuovo sistema di raffreddamento conformato, ridurre i tempi di ciclo dello stampaggio e aumentare la percentuale di successo del 99,7%.
Benefici
•Ottenuto il livello di qualità richiesto in sede di progetto
•Tempo di raffreddamento ridotto del 75%
•Percentuale di successo del 99,7%
•Costi di produzione ridotti
Argomento di studio
Il prodotto, in questo caso, è una parte del serbatoio delle acque reflue dovute all’aspirazione con un diametro di 140 mm, un'altezza di 180 mm e un peso di 270 grammi (Fig. 1).
La Fig. 2 mostra il serbatoio delle acque reflue e il layout della matarozza (canale caldo).
A causa della temperatura elevata, fino a 230 ℃, all'ugello del canale caldo, sono stati necessari 120 secondi perché la plastica fusa si solidificasse.
Per ridurre il tempo di ciclo e migliorare la qualità del prodotto, vengono proposti tre progetti diversi di gate con diametri diversi, 2,5 mm, 3,0 mm e 4,0 mm (Fig. 3).
Il design del sistema di raffreddamento utilizzato in questo prodotto è mostrato in Fig.4.
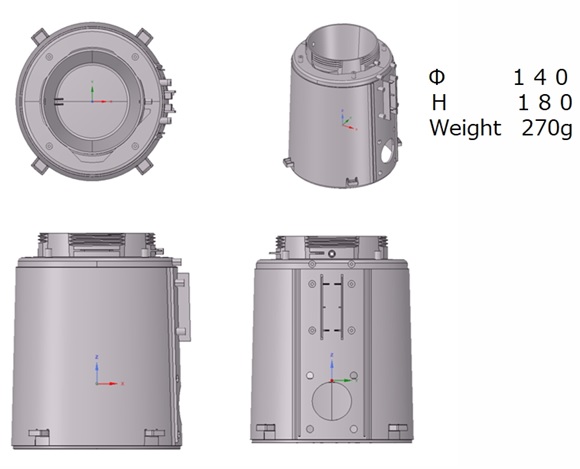
Fig. 1 La parte del serbatoio delle acque reflue
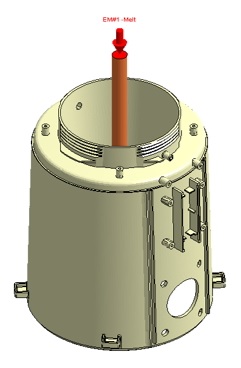
Fig. 2 Il design del layout del canale caldo di questa parte
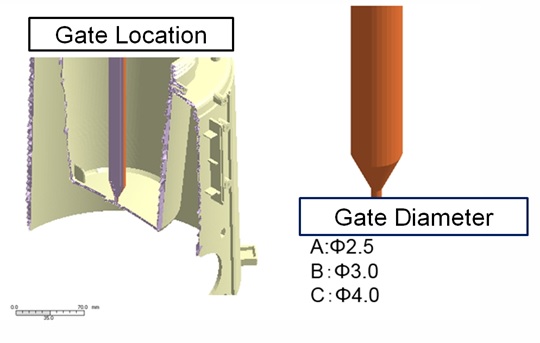
Fig. 3 Posizione e layout dell’Hot Runner
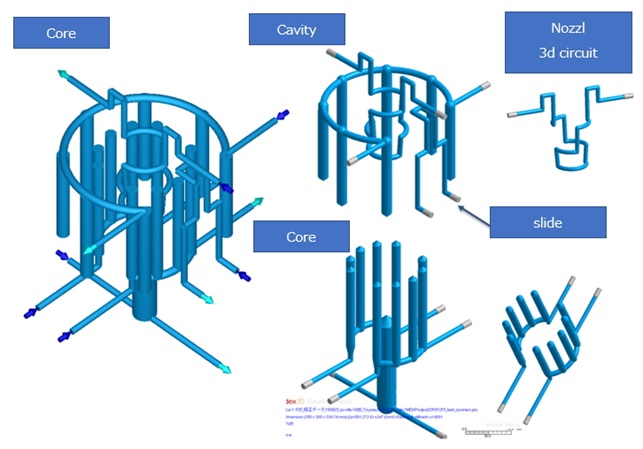
Fig.4 il progetto del sistema di raffreddamento
I risultati dell'analisi Moldex3D hanno identificato le zone di criticità e indirizzato verso la miglior soluzione. La temperatura massima del fronte di fusione dei diametri di 2,5 mm, 3,0 mm e 4,0 mm può raggiungere rispettivamente 241, 239 e 236 ℃ (Fig. 5). Le pressioni nella materozza raggiungono tutte il valore massimo di 200 MPa e questa potrebbe essere la causa del mancato riempimento. I risultati sono riassunti nella Fig.6.
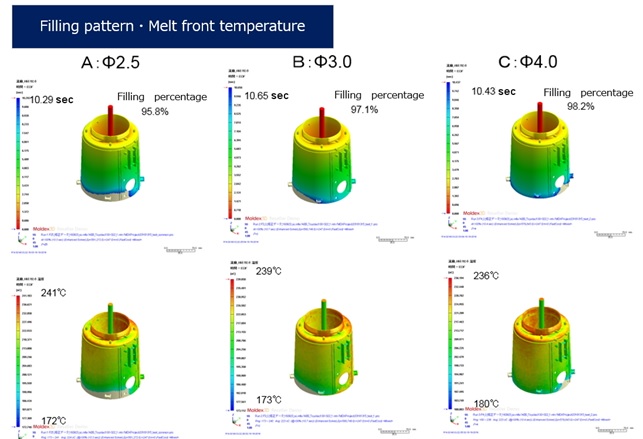
Fig. 5 Schema di riempimento e risultati della temperatura del fuso
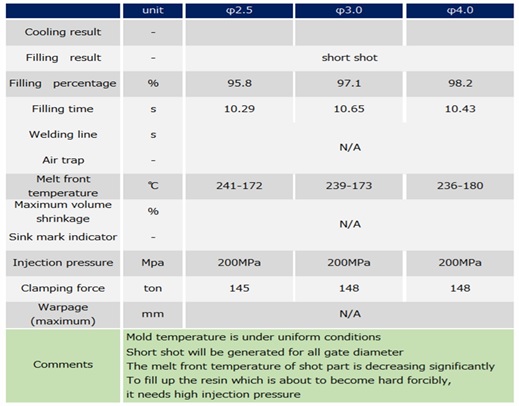
Fig. 6 Riepilogo dei risultati dell'analisi Moldex3D di tre progetti di diametro del cancello.
Sulla base dei risultati dell'analisi di Moldex3D, la bassa temperatura alla fine del riempimento era la precedente causa di scatti brevi. Pertanto, si è reso necessario ottimizzare il progetto del canale di raffreddamento. (Fig.7).
L'obiettivo era ridurre il tempo di riempimento da 8 secondi a 4 secondi e ottenere un raffreddamento più uniforme (Fig. 8).
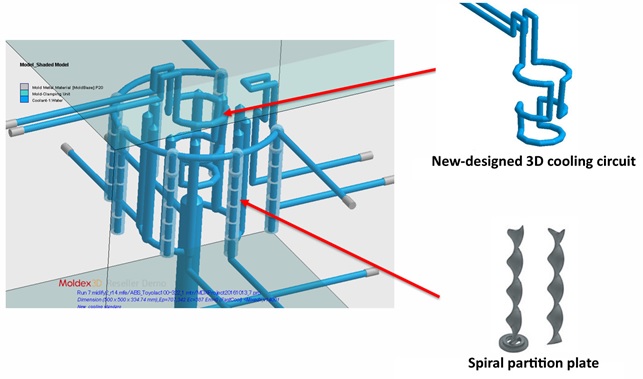
Fig.7 Circuiti di raffreddamento 3D migliorati
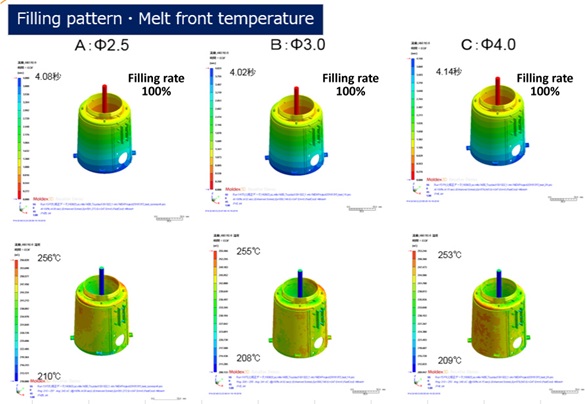
Fig. 8 Il piano di miglioramento
I risultati della simulazione dei canali di raffreddamento modificati hanno mostrato che il problema del mancato riempimento è stato eliminato (Fig. 9), ma la pressione del canale di colata è ancora troppo alta. La pressione del canale di colata è 200 MPa, 198 MPa e 197 MPa con il diametro del punto di iniezione rispettivamente di 2,5 mm, 3,0 mm e 4,0 mm (Fig. 10).
I risultati della distribuzione della temperatura della base dello stampo hanno mostrato che i canali di raffreddamento modificati hanno prodotto una migliore efficienza di raffreddamento e una distribuzione della temperatura più uniforme (Fig. 11).
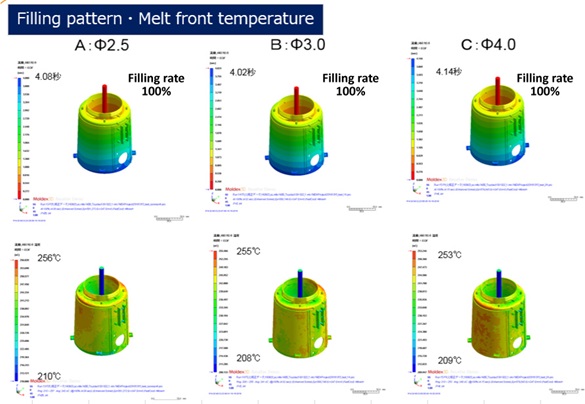
Fig. 9 Schema di riempimento e risultati della temperatura del fuso con i canali di raffreddamento ottimizzati.
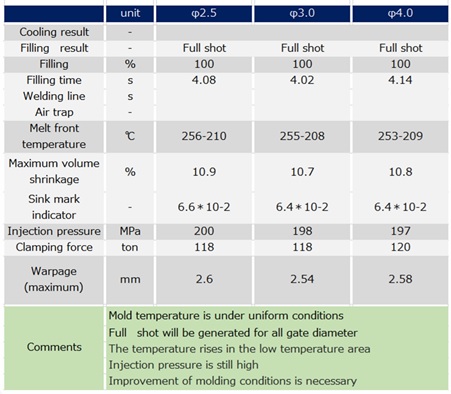
Fig. 10 Panoramica dei risultati dell'analisi dei canali di raffreddamento modificati.
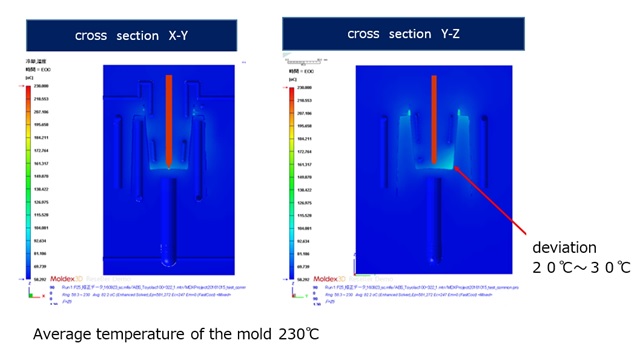
Fig. 11 Confronto dei circuiti di raffreddamento 3D originali (sopra) e modificati (in basso).
Per diminuire la pressione del canale di colata, sia la temperatura del materiale sia la temperatura dello stampo sono state aumentate rispettivamente a 250 ℃ e 80 ℃. In questo modo, la pressione del canale di colata è stata ridotta a 170,27 MPa (Fig. 12).
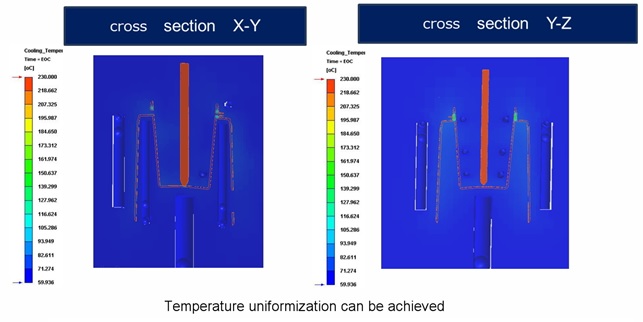
Fig. 12 La temperatura del materiale e dello stampo sono state aumentate per ridurre la pressione del canale di colata.
Risultati
L’utilizzo di Moldex3D ha permesso a Yuuki di prevedere e correggere potenziali difetti (es.: possibili bruciature), accorciare il tempo di ciclo da 120 sec a 40 sec e ridurre il livello di difettosità a meno dello 0,2%. Con Moldex3D, Yuuki è riuscita a bilanciare la qualità, i tempi e i costi globali
MDXITA_prt_2020109