EXTREME inc. - Utilizzo di Moldex3d per eliminare incertezze in fase di stampaggio
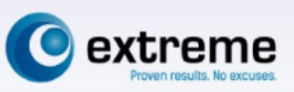
Profilo cliente
•Cliente: Extreme Tool and Engineering
•Paese: STATI UNITI
•Industria: progettazione e realizzazione stampi
•Soluzione: pacchetto avanzato Moldex3D; Flow, Pack, Cool, Warp, CFD refrigerante 3D
Fondata nel 1998, Extreme è un importante impianto di progettazione e produzione di stampi che è un fornitore leader di innovativi servizi di sviluppo di prodotti in plastica chiavi in mano. (Fonte:
www.extremetool.com )
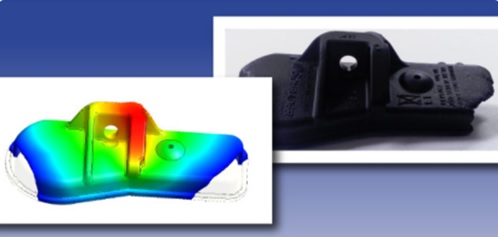
Premessa
C'erano molte incertezze che circondavano il processo di stampaggio di Extreme prima di utilizzare Moldex3D
•Quale sarà il tempo di riempimento?
•La nostra pressa può generare la pressione necessaria?
•Di quanta forza di chiusura dello stampo avremo bisogno?
•I profili macchina per il flusso e per il mantenimento son corretti?
Per ridurre queste incertezze, Extreme ha deciso di esaminare le soluzioni Moldex3D che possono contribuire a fornire maggiore fiducia prima della produzione effettiva.
Sfide
•Trovare le posizioni di ventilazione appropriate
•Trovare la temperatura del refrigerante appropriata
•Ottenere il tempo di impaccamento effettivo per soddisfare le specifiche di ritiro del pezzo
Soluzioni
Utilizzo del pacchetto Moldex3D BLM Advanced e del 3D CFD per l’analisi avanzata del comportamento del sistema di condizionamento, per trovare le condizioni ottimali nel processo di stampaggio.
Benefici
•Trova le aree che richiedono lo sfiato dei gas (venting)
•Ridurre al minimo il ritiro della parte
•Ottimizzare il tempo di raffreddamento e il tempo di ciclo
Caso di studio
Extreme ha scelto Moldex3D per aiutare il progettista ad eliminare le incertezze derivanti dal processo di stampaggio.
Si vorrebbe uti
lizzare Moldex3D per trovare l'area in cui è richiesto uno sfiato d'aria aggiuntivo, la pressa necessaria, la massima forza di chiusura, un tempo di riempimento ragionevole e prevedere la deformazione più accurata possibile, prima delle prove di stampo.
Dalla simulazione di riempimento /impaccamento, si sapeva che la pressione di riempimento era ben al di sotto del massimo, la forza massima di chusura dello stampo era accettabile e la velocità massima di taglio era inferiore al limite.
Si conclude pertanto che la fase doi stampaggio era in linea per soddisfare le esigenze richieste (fig. 1).

Fig. 1
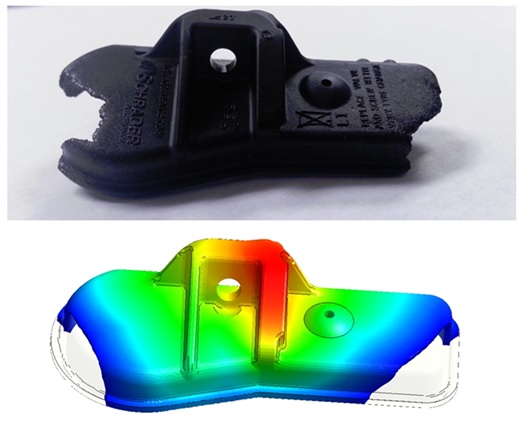
L'analisi di potenziale mancato riempimento di Fig. 2 Moldex3D è risultata coerente al risultato effettivo.
Extreme ha quindi cambiato la temperatura nei circuiti di condizionamento, il che ha portato a una temperatura superficiale media molto più bassa.
Sono state simulate 3 diverse condizioni di temperatura del refrigerante e osservato la loro influenza sulla temperatura superficiale della parte e sul ritiro. (Fig. 3).
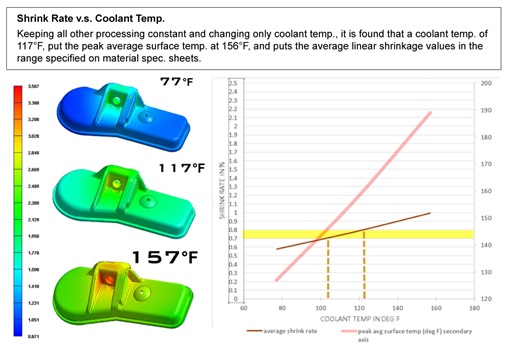
Fig. 3
Successivamente, Extreme ha aumentato il tempo di impaccamento ed ha simulato 4 diversi tempi di impaccamento e osservato i risultati relativi al ritiro. Si è quindi ritenuto accettabile il compromesso proposto (Fig. 4).
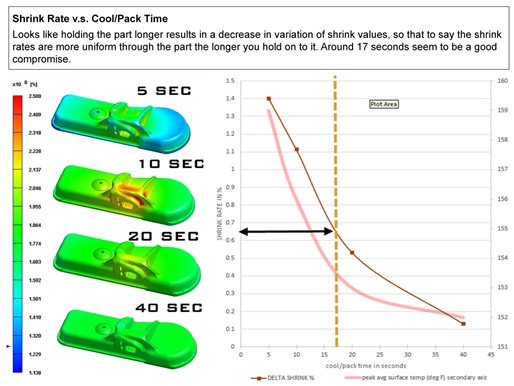
Fig. 4 Il tempo di imballaggio di 17 sec:.
Risultati
Il software di simulazione Moldex3D fornisce strumenti per esaminare potenziali aree problematiche nelle parti e aiuta Extreme a prendere decisioni ben informate.
Extreme ha utilizzato le informazioni ottenute dalla simulazione per ottimizzare il raffreddamento e determinare il tempo di ciclo.
Questo li ha anche aiutati a evitare costose riparazioni e rielaborazioni di stampi e la simulazione può guidare ulteriormente i progetti futuri con fiducia nella precisione.