Nuova metodologia per ottimizzare il progetto di una sedia stampata ad iniezione assistita da gas
(GAIM Gas Assisted Injection Molding)
I circa 122.000 dipendenti del gruppo BASF lavorano per contribuire al successo dei loro clienti in quasi tutti i settori e in quasi tutti i paesi del mondo.
Il loro portafoglio è organizzato in sei segmenti: prodotti chimici, materiali, soluzioni industriali, tecnologie di superficie, nutrizione e cura e soluzioni agricole. (Fonte: https://www.basf.com/global/en/who-we-are.html)
Sommario
Una sedia in plastica rinforzata con fibre (FRP) di BASF è stata prodotta utilizzando GAIM (stampaggio a iniezione assistita da gas).
Tuttavia, il problema di difetti dovuti all’impiego del gas per alleggerire la struttura e ridurre le deformazioni, si è verificato durante la produzione e ha portato a una resistenza meccanica non accettabile.
Poiché le modifiche alla progettazione non erano consentite, gli ingegneri BASF avevano il compito di ottimizzare le condizioni di processo GAIM per ridurre il peso dei pezzi senza sacrificarne la resistenza meccanica.
Le sfide
• Difetti dovuti all’utilizzo di gas
• Cattive proprietà meccaniche
• Non è consentito apportare modifiche al design
Le soluzioni
Con l'uso di Moldex3D, gli ingegneri BASF sono stati in grado di ridurre al minimo i difetti introdotti dall’utilizzo della tecnica di svuotamento con gas ottimizzando le condizioni di processo.
Di conseguenza, la sedia ha soddisfatto i requisiti di peso e ha acquisito una migliore integrità strutturale allo stesso tempo.
Benefici
• Contenimento dei difetti
• Aumento della resistenza del 60%
• Soddisfazione dei requisiti di peso e carico
Argomento di studio
In questo progetto, BASF ha utilizzato Moldex3D per eseguire la simulazione dello stampaggio a iniezione assistita da gas (GAIM) per analizzare nel dettaglio il progetto della sedia.
I tecnici BASF hanno affrontato un grave problema di diteggiatura del gas all'interno della superficie di seduta e dello schienale della sedia.
L'integrità strutturale stessa della sedia induceva una certa fragilità meccanica.
Poiché la sedia è una sedia di design, lo stampo è già prodotto e non c’era spazio per lo sviluppo della modifica dello stampo.
Pertanto, per fare in modo che la sedia rispettasse i carichi imposti, il compito era di ottimizzare solo i parametri di elaborazione.
Nel design originale dei risultati, la temperatura centrale alla commutazione GAIM ha una differenza inferiore a 2 ° C tra la regione spessa e la regione sottile (mostrato in Fig. 1).
In altre parole, il gas entra facilmente nella regione sottile (causando l'effetto diteggiatura del gas) a causa della resistenza simile al flusso delle regioni spesse.
La simulazione indica che il gas non entrerà nella regione sottile quando la differenza di temperatura tra i due è significativamente maggiore.
Pertanto, si è aumentato il ritardo del gas, il tempo di riempimento e di confezionamento nell’obiettivo di ottimizzare il processo
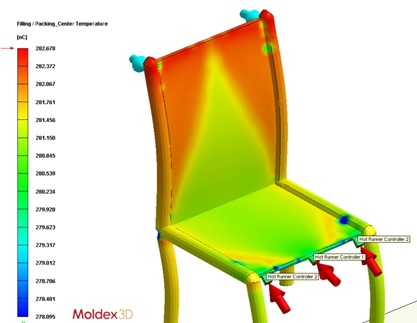
.
Fig. 1 I risultati della simulazione della temperatura centrale
I tecnici BASF hanno ottimizzato il processo con varie combinazioni per migliorare i risultati, aumentando il tempo di riempimento a 6 secondi, il tempo di confezionamento a 10 secondi e il tempo di ritardo del gas a 15 secondi.
La Fig. 2 mostra il risultato ottimizzato in cui il nucleo del gas confina solo nell'area richiesta.
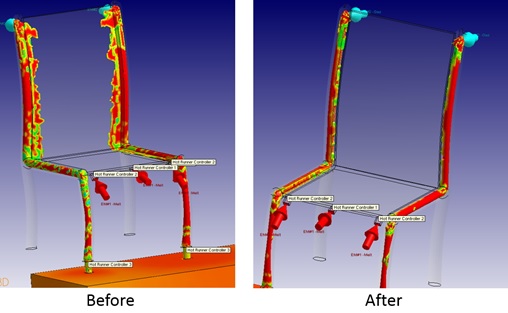
Fig. 2 La tendenza del nucleo di gas prima e dopo l'ottimizzazione
Con l'impostazione ottimizzata, la differenza della temperatura centrale tra la regione spessa e la regione sottile è compresa tra 7 e 10 ° C (Fig. 3), il che significa che il gas non può entrare nelle regioni sottili e che viaggia nella regione con temperatura più elevata (regione spessa ) a causa della minima resistenza al flusso.
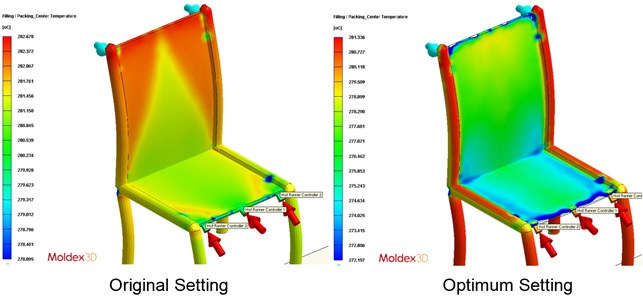
Fig. 3 Confronto della temperatura centrale tra le impostazioni originali e ottimizzate
Moldex3D supporta l'esportazione dei dati di simulazione verso altri software FEM con ulteriore simulazione strutturale.
In questo caso, BASF ha utilizzato i risultati della simulazione di Moldex3D per convalidare la soluzione del problema trasferendoli in Abaqus.
La Fig. 4 mostra la forza alla rottura della sedia con un'impostazione ottimale superiore del 60% rispetto all'impostazione originale.
Illustra anche che lo spostamento in caso di crisi meccanica della sedia con l'impostazione ottimale è superiore dell'11,5% rispetto all'impostazione originale.
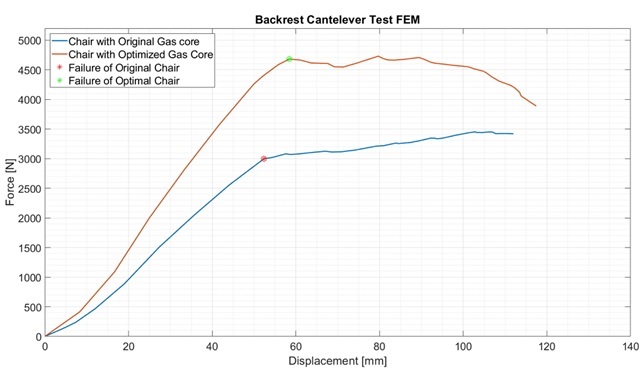
Fig. 4 Confronto di spostamento rispetto alla forza usando Abaqus
Risultati
Con Moldex3D è possibile simulare facilmente lo stampaggio a iniezione assistito da gas e condurre studi di ottimizzazione.
La funzione della simulazione della temperatura centrale è particolarmente utile per il processo GAIM.
Inoltre, l'interfaccia FEA nel Modex3D aiuta ad acquisire dati per ulteriori analisi strutturali meccaniche di resistenza ai carichi.
I complessi processi FEM utilizzati nel settore e i dati esportati potrebbero essere letti facilmente da altri programmi e rielaborati per raggiungere il miglior risultato
MDXITA Giorgio Nava – prt_20200055