Simulazione MCM (2K e 3K)
Jing Wei, Senior Architecture Manager presso la divisione ricerca e sviluppo del prodotto, Moldex3D
La tecnologia di stampaggio multicomponente (MCM) può integrare in modo efficiente più di due parti in plastica separate ed è ampiamente applicata nel settore (sovrastampaggio 2K e 3K).
Attraverso l'analisi CAE,gli sviluppatori di prodotto e i progettisti dello stampo per realizzare il prodotto, possono simulare la qualità del prodotto in anticipo.
Tuttavia, se consideriamo solo l'elaborazione dela seconda stampata, la qualità del prodotto e l'ottimizzazione del progetto non possono essere garantite.
A causa degli effetti di iniezioni multiple e dei differenti materiali, lo stato dell'inserto della parte alla fine della prima stampata influenzerà i comportamenti di deformazione dell’asieme dovuta alla seconda stampata.
Pertanto, si devono controllare meglio gli effetti della parte precedente sulla seconda stampata (differenti coefficienti di scorrimento del fonte quando a contatto con le superfici delle stampo e la superficie della prima stampata e le deformazioni conseguenti).
In che modo le proprietà del materiale della prima stampata influiscono sul seconda stampata
Le proprietà di espansione meccanica e termica dei materiali sono fattori importanti che influenzano i comportamenti, sia per lo scorrimento del flusso sia per le deformazioni risultanti.
Nel processo MCM, il prodotto finale potrebbe essere assemblato anche con più di due materiali.
Se l'inserto della parte della seconda stampata è realizzato in plastica rinforzata con fibre, le sue proprietà anisotropiche influenzeranno la deformazione del prodotto finale.
Inoltre, l'inserto della parte proviene dallo scatto precedente, quindi l'orientamento della fibra causato dalla stampata precedente sarà molto rilevante per il secondo colpo (Fig. 1).
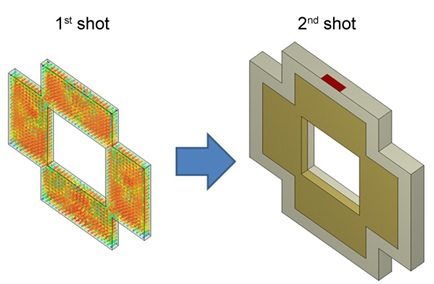
Fig. 1 La prima stampata con plastiche rinforzate da fibre viene utilizzata come inserto nello stampo per la seconda stampata
In che modo l'elaborazione della stampata influisce sulla seconda stampata
Le condizioni di progettazione e lavorazione dello stampo del colpo precedente derivano dagli stati di pressione e temperatura interni nell'inserto della parte del colpo precedente.
Pertanto, sotto le interazioni tra i diversi componenti, lo stato iniziale dell'inserto della parte porterà cambiamenti alla conduzione del calore e all'equilibrio di sollecitazione dei prodotti.
Ovvero, per garantire la qualità del prodotto finale, dobbiamo anche considerare il processo di produzione della prima stampata (Fig. 2)
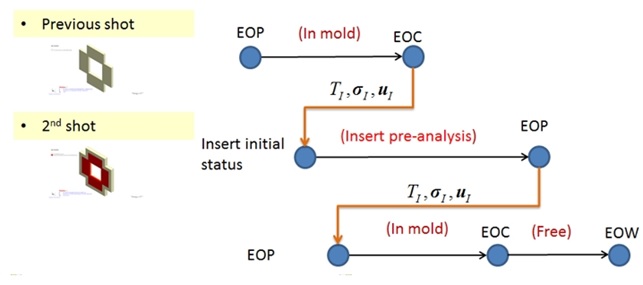
.
Fig. 2 Lo stato dell'inserto della parte del secondo colpo dopo il colpo precedente
Per considerare in modo completo gli effetti dela prima stampata, Moldex3D può integrare i risultati dell'analisi della prima fase nella simulazione della seconda stampata (Fig. 3).
I risultati di riempimento/impaccamento/raffreddamento e orientamento della fibra del colpo precedente possono essere tutti utilizzati nella simulazione della seconda stampata.
Pertanto, gli utenti possono ottenere risultati di analisi delle deformazioni e dei ritiri in modo più accurato ed affidabile.
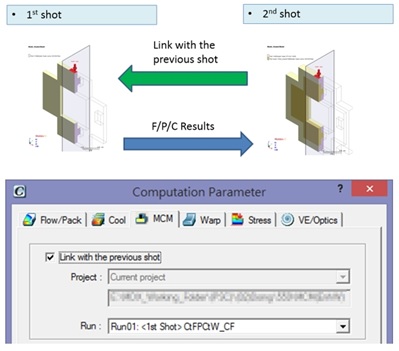
Fig. 3 Integrare i risultati dell'analisi dello scatto precedente nella simulazione del secondo colpo
Attraverso l'analisi Moldex3D (warpage), gli utenti possono considerare vari effetti e situazioni tra cui l'orientamento della fibra, la temperatura e la pressione della stampata precedente nella simulazione dell'inserto parte 1 per la seconda stampata.
Quindi, i risultati dell'analisi delle deformazioni possono essere più coerenti con la realtà e il progettista può ottimizzare ulteriormente la qualità del prodotto valutando al meglio le criticità e i risultati della simulazione.