Il successo della simulazione del flusso viscoelastico richiede dati reologici affidabili
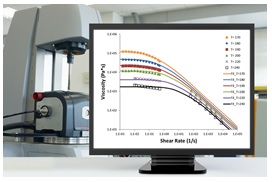
Il comportamento reologico è una delle proprietà più complesse e importanti nella lavorazione dei polimeri.
Per completare una simulazione di processo di successo, sono necessari dati e modelli affidabili sui materiali.
Il flusso del polimero può essere previsto ragionevolmente bene con l'ipotesi di fluidi anelastici (newtoniani generalizzati) e con i dati del reometro capillare.
Tuttavia, l'analisi anelastica potrebbe non riuscire a descrivere i fenomeni viscoelastici, perché i polimeri sono di natura viscoelastica.
La curva tipica di modulo e viscosità di un polimero amorfo è mostrata in Fig. 1 [1].
Fondamentalmente, il comportamento elastico diventa sempre più significativo rispetto al comportamento viscoso al diminuire della temperatura.
Secondo la fisica del polimero, lo stato di un polimero può essere suddiviso in cinque regioni.
(1) regione vetrosa;
(2) transizione vetrosa;
(3) regione gommosa;
(4) flusso viscoelastico;
(5) flusso viscoso.
Nella regione viscosa (5) il modello anelastico (o newtoniano generalizzato) è il modello appropriato per simulare il flusso del fluido.
La componente elastica inizia a diventare sempre più importante dalla regione di flusso viscoelastico (4) alla regione “gommosa” (3).
Il materiale si comporta sempre più in modo solido (elastico) dalla transizione vetrosa (2) alla regione vetrosa (1).
Nella fase di riempimento, la temperatura del fuso è solitamente superiore alla temperatura dell'ugello a causa del riscaldamento viscoso; la temperatura scende nella regione del flusso viscoso indicando che possono essere utilizzati modelli anelastici (newtoniani generalizzati).
Nella fase di impaccamento, la temperatura del fuso inizia a raffreddarsi e passa da viscoelastica (4) a gommosa (3), il che indica che il comportamento elastico inizia a svolgere un ruolo cruciale. Dopo la fase di impaccamento, il polimero attraversa la transizione vetrosa nella fase di raffreddamento e raggiunge la regione vetrosa nella fase di espulsione.
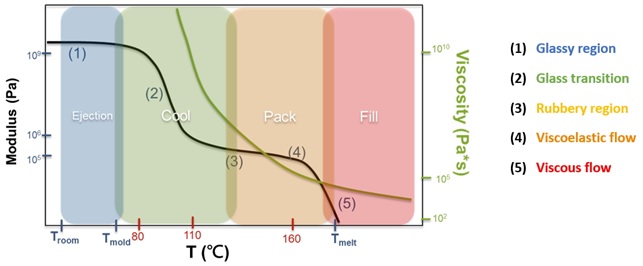
Fig.1 Modulo e viscosità del polimero amorfo (sono indicate le zone di transizione)
Oltre a un risolutore viscoelastico stabile ed affidabile, sono necessari dati consistenti sui materiali e parametri del modello matematico per completare una simulazione di flusso viscoelastico che abbia validità. In laboratorio sono disponibili diversi tipi di reometro, come un reometro capillare, un reometro rotazionale e un DMA nel laboratorio materiali di CoreTech System Co. (Moldex3D).
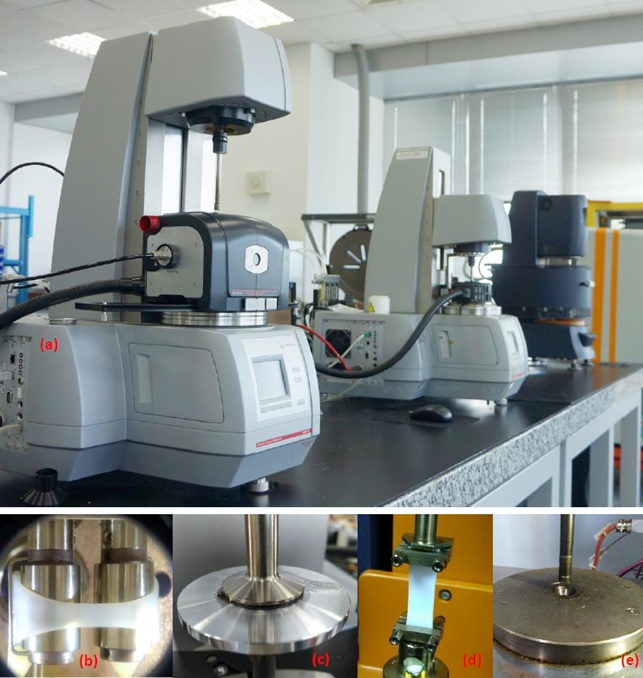
Fig. 2 (a) Reometri rotazionali inclusi Anton Paar MCR-502 e TA DHR-3; (b) Sentmanat Extensional Rheometer (SER); (c) fissaggio della piastra parallela; (d) fissaggio torsionale della modalità DMA; (e) reometro capillare.
In generale, si ritiene che il riempimento nello stampaggio a iniezione abbia un'elevata velocità di taglio e un flusso ad alta temperatura.
Pertanto, il reometro capillare è generalmente lo strumento ideale per caratterizzare il comportamento del flusso.
Tuttavia, ci sono alcune regioni nella cavità, come lo strato centrale o l'area spessa, dove il flusso è inferiore con una velocità di taglio bassa.
Inoltre, la bassa temperatura sarebbe osservata negli strati superficiali esterni, soprattutto nella fase di confezionamento.
Di conseguenza, i dati di viscosità solo dal reometro capillare potrebbero non essere sufficienti per descrivere con precisione l'intero processo.
Per estendere l'intervallo tra velocità di taglio e temperatura, vengono utilizzati entrambi il reometro a piastra parallela e capillare.
Inoltre, polimeri fusi con comportamento al taglio simile possono mostrare un comportamento estensionale molto diverso, specialmente per polimeri altamente “ramificati” [2].
Pertanto, il SER è stato utilizzato per ottenere le proprietà reologiche nel campo di flusso estensionale.
L'intervallo misurabile del reometro capillare ha una temperatura elevata (intorno alla temperatura di processo) e un'elevata velocità di taglio (10 - 10.000 s-1).
Tuttavia, quando si passa alla fase di impaccamento, la sua velocità di taglio diminuirebbe improvvisamente a meno di 10 s-1 e la temperatura sarebbe inferiore di quella nella fase di riempimento.
Nella fase di raffreddamento, la temperatura risulterebbe inferiore a Tg.
Le finestre di temperatura e velocità di taglio degli stadi sono mostrate in Fig. 3 (a).
Ovviamente, la temperatura e la velocità di taglio delle fasi di impaccamento o raffreddamento sono al di fuori del normale intervallo misurabile del reometro capillare.
Potremmo sfruttare vari strumenti (inclusi reometro rotazionale e DMA) per ottenere dati reologici con velocità di taglio e temperatura inferiori. Gli intervalli misurabili di questi strumenti sono mostrati nella Fig. 3 (b).
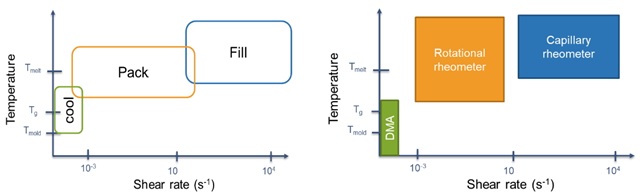
Fig 3. Finestre di temperatura e velocità di taglio di (a) vari stadi nello stampaggio a iniezione; (b) vari strumenti reologici.
Per modellare accuratamente il flusso del polimero sia per le fasi di riempimento che per quelle di impaccamento le cui velocità di taglio sono comprese tra 104 e 10-3 s-1, potremmo integrare i dati del reometro capillare e rotazionale.
Un esempio (polistirolo) è mostrato in Fig.4.
La temperatura del polimero nello stampaggio a iniezione può variare dalla temperatura del fuso alla temperatura dello stampo (es. Tmelt ≈ 200 ℃ e Tmold ≈ 60 ℃ per PS).
Per ottenere dati reologici affidabili, potremmo combinare il reometro rotazionale e il DMA.
La Fig. 5 mostra i moduli dinamici di PS dalla temperatura di fusione (200 ℃) allo stato vetroso (30 ℃).
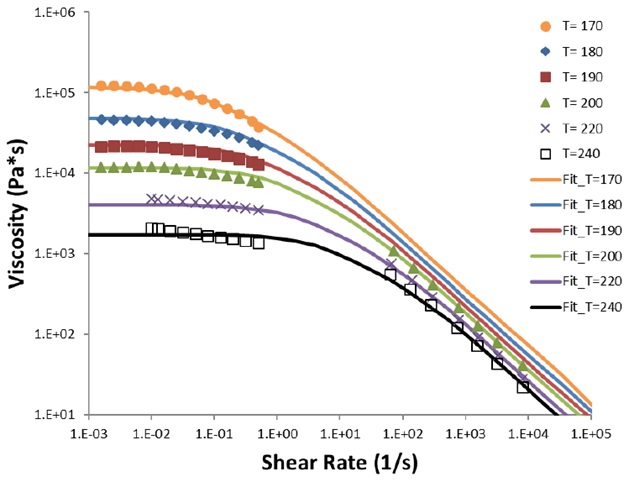
Fig. 4 Viscosità di taglio da reometro capillare e rotazionale.
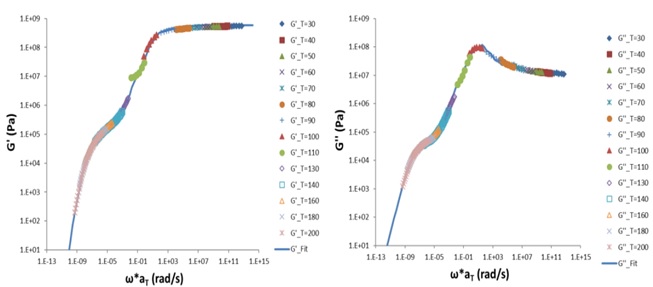
Fig. 5 Moduli dinamici della curva master sia dal reometro rotazionale che dal DMA
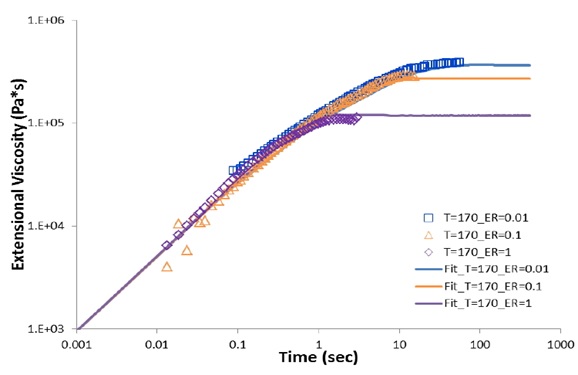
Fig.6 viscosità estensionale da SER
Il modello viscoelastico potrebbe essere utilizzato per adattare i dati reologici di vari strumenti. L'esempio EPTT è mostrato in Fig. 4-6 come linea continua).
Il modello viene applicato nel risolutore di flusso viscoelastico Moldex3D.
La figura 7 (a) mostra una geometria dello stampo che include la guida e ed il dispositivo di iniezione.
Lo spessore della parte è di 2 mm e la larghezza e la lunghezza sono entrambe di 60 mm.
Per la convalida vengono condotti vari esperimenti di stampaggio a iniezione del polistirolo. Il confronto tra sperimentale e simulazione per varie pressioni di impaccamento è mostrato in Fig. 7 (b).
Si è riscontrato che le simulazioni sono coerenti con le curve sperimentali durante l'intera fase di riempimento e impaccamento tranne il momento immediatamente successivo al cambio V / P, che è fortemente influenzato dalla risposta della macchina. La pressione di picco degli esperimenti situati su V / P è 53,7 ± 0,3 (MPa), che è molto vicina al risultato della simulazione 54,6 (MPa).
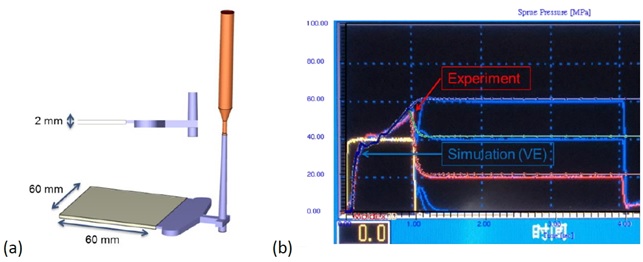
Fig. 7 (a) geometria dello stampo ad iniezione; (b) curve di pressione nel canale di colata (valori sperimentali e di simulazione).
Se esaminiamo i dettagli nel processo di iniezione di Moldex3D, possiamo scoprire che la distribuzione della velocità di taglio durante il riempimento è da circa 2.000 a 7.000 s-1 nel corridore e da 600 a 1.000 s-1 nella cavità, come mostrato in Fig. 8.
Queste velocità di taglio rientrano nell'intervallo del reometro capillare.
La Fig. 9 mostra la distribuzione della velocità di taglio nella fase di imballaggio.
La velocità di taglio è inferiore a 20 s-1 nel corridore e inferiore a 1 s-1 nella cavità, che non rientra nell'intervallo misurabile del reometro capillare.
In altre parole, non solo la temperatura ma anche gli intervalli misurabili della velocità di taglio del reometro capillare non sono sufficientemente ampi da coprire la simulazione di impaccamento.
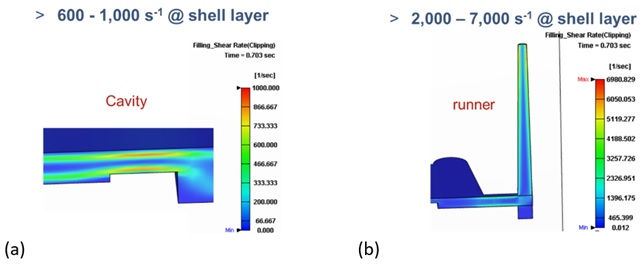
Fig. 8 Distribuzione della velocità di taglio alla fine del riempimento in (a) cavità (b) runner
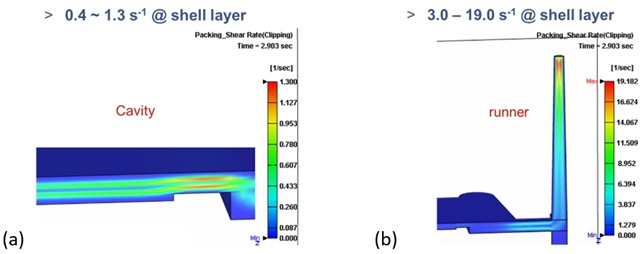
Fig. 9 Distribuzione della velocità di taglio nella fase di riempimento nella guida (a) della cavità (b).
La Fig. 10 mostra la temperatura nella fase di impaccamento.
È inferiore a 180 ℃ nello strato del guscio del sistema di alimentazione ed è inferiore a 140 ℃ nella cavità.
Ovviamente le temperature sono nuovamente al di fuori del range del reometro capillare.
Inoltre, si trovano nell'intervallo di temperatura dalla regione viscoelastica a quella gommosa, in cui il comportamento elastico gioca un ruolo importante.
Di conseguenza, il reometro rotazionale contribuisce a ottenere una velocità di taglio bassa e dati a bassa temperatura per completare una simulazione di successo, specialmente nella fase di imballaggio.
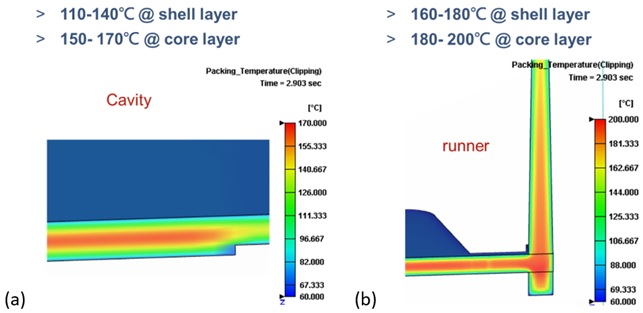
Fig. 10 Distribuzione della temperatura nella fase di riempimento nella guida (a) cavità (b).
In sintesi, per simulare l'intero processo di stampaggio a iniezione in modo più realistico e accurato, potremmo combinare i vari strumenti per ottenere un'ampia gamma di dati reologici coerenti e consistenti.
Tuttavia, ci vorrà un forte sostegno da parte dei fornitori di materiali per aumentare la disponibilità generale di dati viscoelastici.
Riferimenti
1. Shaw, M.T.; MacKnight, W. J. Introduzione alla viscoelasticità dei polimeri; Wiley, 2005.
2. Macosko, C. W. Reologia: principi, misurazioni e applicazioni; Wiley, 1994.