Usare l'analisi 3D CFD per ottenere un progetto ottimizzato per un sistema di raffreddamento di tipo conformato
Oggi ci sono ancora persone che giudicano con scetticismo l’utilizzo di sistemi di raffreddamento conformati (CCS Conformal Cooling Systems), questo a cause delle difficoltà ad analizzare e simulare correttamente il circuito e le sue prestazioni.
La simulazione è un ottimo strumento di validazione, ma questo non è tutto.
È uno strumento potente, ma i risultati si basano ancora sull'input proveniente dagli utenti.
Naturalmente, ci sono strumenti e moduli di ottimizzazione all'interno del software, ma se applicati male quello che si ottinere non è valido: "garbage in garbage out".
Due analisti che eseguono una simulazione di iniezione plastica possono arrivare risultati totalmente diversi se gli input sono diversi o incompleti.
Per un raffreddamento conformato, in particolare, ipotesi errate e la mancanza o incompletezza di fattori importanti, come la capacità di raggiungere la portata necessaria per garantire un flusso turbolento, può comportare un risultato negativo.
Simulazione e Analisi
Un sistema di raffreddamento conformato può aiutare a ridurre al minimo il tempo di ciclo e raggiungere le tolleranze dimensionali richieste dal progetto. Tuttavia, funzionerà come pure la simulazione, se il progettista è in grado di mantenere la portata necessaria attraverso il circuito di raffreddamento conformato.
Un designer che esegue una simulazione del dissipatore di calore (canale di raffreddamento definito solo come fonte di dissipazione di calore), su progetti complessi, non sarà in grado di raccontare la storia completa di ciò che può accadere nello stampo.
Diamo un'occhiata ad alcuni risultati in Fig. 1, che provengono da un'analisi computazionale della fluidodinamica (CFD) che mostra il numero di Reynolds a una portata di circa 2,0 gpm.
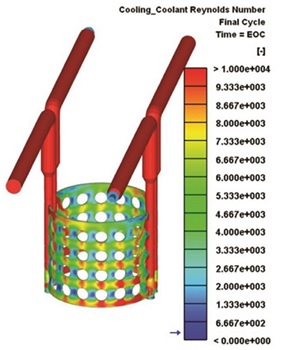
Fig. 1 Risultati di un'analisi computazionale della fluidodinamica (CFD) che mostra il numero di Reynolds a una portata di circa 2,0 gpm.
Alcune regioni mostrano un numero di Reynolds superiore a 4200, che indica un flusso turbolento mentre altre regioni mostrano un numero di Reynolds inferiore a 4200, che indica che il flusso in determinate regioni potrebbe non essere necessariamente turbolento, ovvero lavorare in regime laminato.
Questa variazione condizionerà l'efficienza di raffreddamento in tutto il circuito. La velocità ha una correlazione diretta con il numero di Reynolds, quindi se un progettista identifica le regioni a flusso basso / assente può ottimizzare il design del canale di raffreddamento.
La simulazione può anche visualizzare risultati di velocità che indicano regioni a flusso basso / assente (regime laminare) che svolgono meno lavoro e aree potenzialmente stagnanti (turbolenza eccessiva). Si deve tener presente che i fluidi seguono il percorso di minor resistenza, quindi invece di percorrere percorsi casuali e fluire attorno a tutti i fori, il liquido di raffreddamento tenderà a fluire direttamente dal lato di ingresso al lato di uscita.
I progettisti possono utilizzare tali dati per ottimizzare il design in modo da ridurre al minimo le regioni a flusso basso / assente (mostrate in blu scuro tra i fori Fig. 1).
Ad esempio, i progettisti possono provare a compensare i fori per deviare l'acqua attraverso le regioni con un numero di Reynolds basso, che indica regioni a flusso basso / assente.
Nonostante un designer abbia compensato i fori, può rimanere un percorso di minor resistenza.
Tuttavia, la compensazione dei fori può comunque aiutare a ridurre al minimo le regioni a flusso basso / basso, massimizzando il flusso turbolento con una portata valida e raggiungibile.
La domanda ora è "Quanto differiranno i risultati di un'analisi del dissipatore di calore da questi?" Non molto dal punto di vista del calcolo del raffreddamento e in base all'input della portata.
Tuttavia, l'analisi del dissipatore di calore insieme all'analisi dei CFD possono determinare l'efficacia e l'entità del cambiamento.
Anche considerare il dissipatore di calore da solo non funziona bene per l'analisi del canale di raffreddamento conformato, poiché il raffreddamento conformato consiste tipicamente in circuiti di piccolo diametro con lunghezze di flusso lunghe che seguono la geometria delle parti (vedere Fig. 2 e 3). Il diametro, o lo spessore ridotto del design, e i circuiti di lunghezza del flusso maggiore richiedono pressioni più elevate per realizzare una portata sufficiente attraverso il circuito.
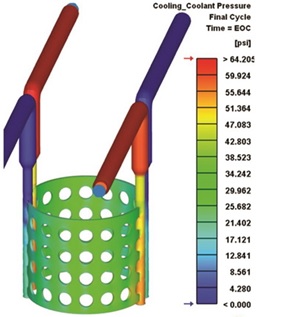
Fig. 2 La pressione del refrigerante deriva dallo stesso modello alla stessa portata di 2,0 gpm.
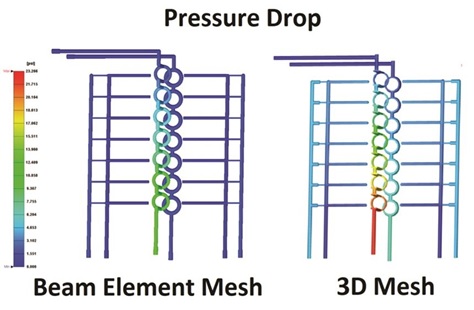
Fig. 3 Un confronto tra i risultati della caduta di pressione tra i metodi di simulazione dell'elemento Beam e 3D mesh.
I risultati della caduta di pressione indicano la pressione di testa necessaria per spingere la portata indicata attraverso i circuiti di raffreddamento.
Requisiti di pressione
Se il numero di Reynolds e la velocità dipendono dalla portata, identificare la pressione richiesta per raggiungere una determinata portata è essenziale per il raggiungimento della portata richiesta, sempre che il tutto sia realistico.
La Fig. 2 mostra i risultati della pressione del refrigerante stesso modello e stessa portata di 2,0 gpm.
Un progettista deve comprendere i requisiti di pressione e la portata minima per ottenere un flusso di corretta turbolenza nel progetto in cui intende avere un buon trasferimento di calore, poiché i fluidi seguono il percorso di minor resistenza.
La Fig. 1 indica che i flussi d'acqua nelle aree in cui il numero di Reynolds è compreso tra 4.000 e 10.000+ e che il flusso turbolento (Re #> 4200) è probabilmente presente nella maggior parte delle regioni.
Tuttavia, per raggiungere questi valori è necessaria una pressione elevata per ottenere un flusso di 2,0 gpm attraverso i circuiti.
I termoregolatori oggi sul mercato possono generare fino a circa 100 PSI, ma 65 PSI potrebbero non essere realizzabili se i fluidi “preferiscono” il percorso di minor resistenza o aree con circuiti meno resistenti come piastre del collettore e piastre del nucleo e della cavità.
Se la portata scende al di sotto di 2,0 gpm, il numero di Reynolds diminuirà, producendo potenzialmente un flusso laminare attraverso il circuito, in altre parole il circuito non è efficiente.
Inoltre, un progettista che semplicemente aumenta la portata al collettore non comporterà una distribuzione lineare del fluido attraverso tutti i circuiti.
I risultati simulati e i risultati effettivi possono differire se un progettista non collega i circuiti di raffreddamento conformati al proprio termoregolatore o se non usano i limitatori di flusso per deviare l'acqua su linee e percorsi specifici.
Se il progettista non riesce a raggiungere la portata necessaria per mantenere il flusso turbolento attraverso un circuito di raffreddamento conformato, può perforare i circuiti convenzionali e ottenere risultati equivalenti o migliori.
E’ una questione di mesh?
Il progettista può ottenere analisi più accurate e affidabili dei progetti di raffreddamento conformi con un'analisi CFD di livello.
Tuttavia, non tutti i sistemi CFD sono uguali.
In un software di simulazione dei processi di iniezione della plastica, i due principali metodi di meshatura per i canali di raffreddamento sono: elementi trave (Beam) ed elementi True 3D .
Gli elementi beam possono determinare il numero di Reynolds, l'aumento / la diminuzione della temperatura in tutto lo stampo e la distribuzione del flusso, ma non sono così accurati come gli elementi mesh True 3D quando prevedono la caduta di pressione. Gli elementi beam hanno anche difficoltà a catturare le geometrie complesse e richiedono la modellazione come volume relativo.
Tuttavia, gli elementi beam producono tempi di simulazione più rapidi rispetto a ad un sistema di meshatura True 3D.
La Fig. 3 confronta i risultati della caduta di pressione tra i metodi di simulazione con elementi beam e il caso di una mesh True 3D.
I risultati della caduta di pressione indicano la pressione di testa necessaria per spingere alla portata indicata attraverso i circuiti di raffreddamento.
Sebbene il rapporto tra i requisiti di pressione da un circuito all'altro sia simile, la simulazione con elementi beam indica una pressione del 25-50% in meno richiesta per i circuiti complessi e la tendenza ad esacerbare la pressione con un complesso design di raffreddamento conforme.
I risultati della caduta di pressione da soli possono portare a considerazioni sbagliate e a dimensionare in modo non corretto il sistema di termoregolazione, con il risultato di ottenere un flusso insufficiente attraverso circuiti più stretti.
Ad esempio, circuiti di raffreddamento conformati che creano un progetto bello ma inefficace.
Come dimostrarlo
Per determinare se gli elementi mesh True 3D catturano una previsione di caduta di pressione più precisa rispetto agli elementi beam, Kevin Klotz di MGS Mfg. Group ha condotto un test per convalidare le previsioni di pressione (vedere Fig. 4).
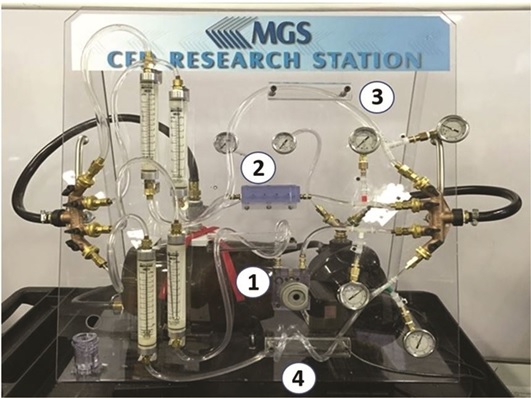
Fig. 4 MGS Mfg. Group ha utilizzato questa apparecchiatura di prova per convalidare le indicazioni di pressione: (1) un inserto conformato raffreddato DMLS, (2) un insieme di gorgogliatori stampati in 3D, (3-4) tubi trasparenti con lunghezza e diametri diversi, manometri e flussometri collegati a una pompa di trasferimento dell'acqua e il serbatoio dell'acqua.
L'apparato è stato modellato in CREO e tarato per confrontarsi con la simulazione.
Lo stesso modello è stato inviato al Dr. Jeet Sengupta della Hoerbiger Corporation of America per eseguire un'analisi CFD tramite ANSYS CFX e Moldex3D per simulare utilizzando la mesh true 3D di strato limite (ambiente di meshatura BLM Boundary Layer Mesh). ”
Entrambi gli strumenti software utilizzano i valori di portata registrati in ciascun circuito e il valore di portata combinato di 6,5 gpm come input dalla pompa per registrare le pressioni nelle posizioni di ingresso, uscita e manometro.
La Fig. 5 mostra i risultati dell'analisi CFD e 3D BLM.
Usando quest'ultimo, il progettista ha modellato i tubi di entrata e di uscita direttamente invece che curvi, poiché il software richiede che gli ingressi e le uscite della sorgente di fluido siano perpendicolari alla faccia dello stampo.
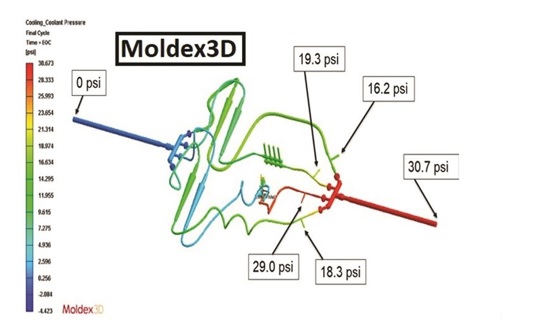
Fig. 5 Risultati di un'analisi CFD e 3D BLM per la mesh del modello.
Usando quest'ultimo, il progettista ha modellato i tubi di ingresso e uscita in modo dritto anziché curvo, poiché il software richiede che gli ingressi e le uscite della fonte di fluido siano perpendicolari alla faccia dello stampo.
I risultati di pressione di entrambi gli strumenti software sono molto vicini ai valori registrati dall'apparato fisico.
La tabella 1 confronta i valori registrati con le pressioni simulate.
Ad esempio, la differenza più grande dall'analisi CFD ai valori registrati è di circa 5,0 psi e 2,5 psi utilizzando la mesh BLM.
Entrambi i risultati hanno una precisione accettabile per lo scopo previsto, considerando la tolleranza nella lettura del manometro e le misurazioni della portata da un misuratore di portata in linea.
Lezioni imparate
Il raffreddamento conforme può funzionare come previsto se è progettato correttamente, il che richiede una simulazione approfondita utilizzando l'analisi CFD per comprendere le caratteristiche del flusso del fluido. Ad esempio, se un inserto stampato in 3D si dirama in due o più canali, la determinazione del ramo preferito può avere un grande impatto sull'efficacia del design di raffreddamento conforme.
Se un progettista esegue solo un'analisi del dissipatore di calore, non acquisirà la differenza né predirà la pressione richiesta per ottenere una portata per flusso turbolento per progetti di raffreddamento complessi come il raffreddamento conforme. Tuttavia, un designer può acquisire con precisione le caratteristiche del flusso di fluido utilizzando elementi mesh 3D. Gli elementi mesh 3D catturano le caratteristiche del flusso di fluido, come il cambiamento di momento, per previsioni accurate della pressione.
(*) Copyright MoldMaking Technology 2019. Reprinted with permission from Gardner Business Media.
Jay Vang
Customer Success Engineer presso Moldex3d Northern America, Inc.
Con una laurea in ingegneria meccanica presso l'Università del Wisconsin-Milwaukee, Jay Vang ha maturato una grande esperienza nella progettazione, sviluppo, produzione e utilizzo di strumenti CAE tra cui Moldex3D, ProE / Creo, Solidworks e Sigmasoft. In qualità Customer Success Engineer presso Moldex3D, Jay aiuta i clienti a utilizzare software di simulazione per garantire risultati realistici e affidabili.
Per ulteriori informazioni info@moldex3d.it
(GN – Ottobre 2019 , prt. 20190080)