Laboratorio Sw Moldex3D al Politecnico di Torino.
Una esercitazione
Moldex3D ha installato un laboratorio SW presso il Dipartimento di Scienze applicate e Tecnologia del Politecnico di Torino. Con l’aiuto del Prof. Alberto Frache, Professore Associato al Dipartimento, quest’anno è stato avviato il primo percorso didattico all’utilizzo di Moldex3D che entra nel piano di studi.
L’attività di formazione è stata sviluppata con l’aiuto dell’Ing. Andrea Romeo di Proplast, ed ha occupato un’attività che ha coperto un periodo di 150 ore, quindi abbastanza esaustiva come “introduzione base”.
A luglio di quest’anno è uscito il primo ingegnere con una tesi che utilizzava Moldex3D, dopo aver effettuato uno stage presso il nostro Cliente MISTA spa di Asti.
Detto questo di seguito viene illustrato uno degli esercizi completati durante questa attività formativa dal Gruppo 4 costituito dagli studenti: Antonacci Carlo, Beanato Chiara, Busso Silvio, Cafiso Diana, Pallaro Roberto, Raverta Ulisse.
Premessa
Sono stati investigate e scelte due possibili soluzioni: con due gate (stampo a tre piastre) e con un solo gate (stampo a due piastre).
Due gates
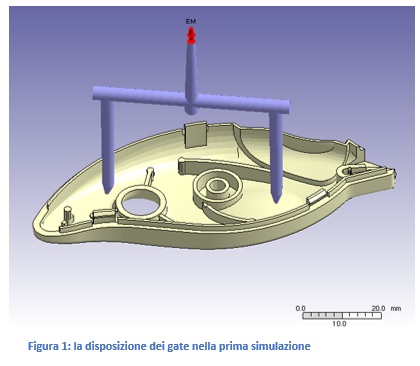
Vista la complessità del pezzo, i gate sono stati posizionati al centro del pezzo, come è illustrato nella figura 1, in modo che ognuno riempisse circa metà del componente.
I gates posizionati all’interno permettono di avere la superficie esterna priva di difetti (no segni del punto di iniezione).
È stata lanciata la simulazione con i parametri di processo di default:
filling 0.37s
packing 3.15s
cooling 10.3s
Il pezzo inevitabilmente presenta una linea di giunzione, che si congiunge a T>300°C (temperatura alla quale la plastica è ancora perfettamente fusa), pertanto non problematica.
Il raffreddamento non è ottimale: la parte centrale dello stampo è 15°C più calda del bordo, perciò sono stati avvicinati i canali di raffreddamento inferiori.
Per velocizzare il raffreddamento è stata abbassata la temperatura dello stampo a 80°C ed è stata rilanciata l’analisi con gli stessi tempi della precedente.
Analizzando il tempo di congelamento dei gate e il tempo necessario per raggiungere la temperatura di estrazione sono stati fissati i nuovi tempi ciclo:
• filling 0.37s
• packing 3.00s
• cooling 7.00s
L’analisi con i nuovi tempi ciclo si è dimostrata soddisfacente, accorciando il tempo totale ciclo di 4.45s.
Un gate
Per evitare di avere una linea di giunzione sul pezzo si è usato un solo gate, posizionato sul bordo inferiore del pezzo, come si vede nella figura 2.
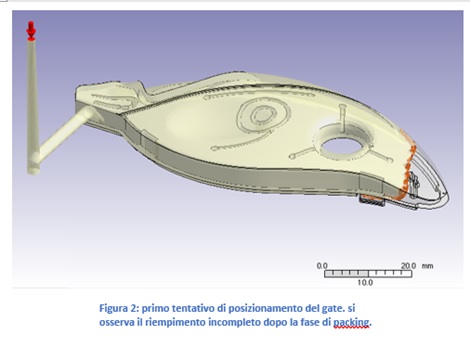
La simulazione con il gate ad una estremità mostra che non si riesce a riempire completamente lo stampo, pertanto il gate è stato spostato in una posizione più centrale, come mostra la figura 3.
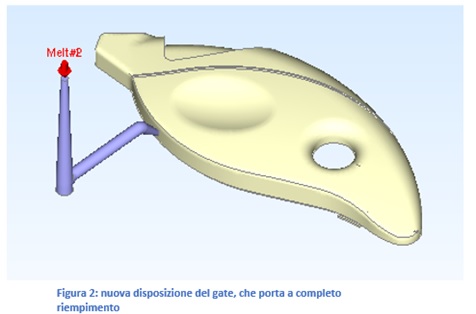
La nuova simulazione utilizza i tempi ciclo di default:
• filling 0.33s
• packing 3.31s
• cooling 10.70s
Da essa osserva il congelamento del gate prima della fine del packing.
Per questo sono stati fissati nuovi tempi ciclo:
• filling 0.33s
• packing 2.80s
• cooling 7.00s
Al termine della fase di cooling in corrispondenza degli snap-fit c’è ancora una piccola quantità di materiale sopra la temperatura di estrazione (a circa 170°C).
Questo non è stato ritenuto problematico in quanto la temperatura media di quegli spessori è sufficientemente bassa per essere estratta.
Si prevede inevitabilmente un risucchio che segnerà la superficie in quel punto.
Conclusioni
Sia la soluzione con due gate che quella con un solo gate (previa le necessarie correzioni dei vari parametri di processo) hanno condotto a buoni risultati.
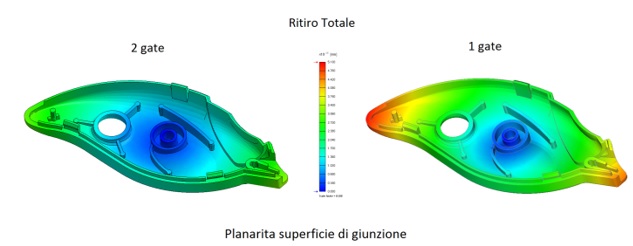
Tuttavia sono state riscontrate alcune differenze.
La soluzione con due gate presenta un minor ritiro, ma rimangono stress residui di maggiore intensità in zone potenzialmente critiche.
Con un solo gate, invece, si garantisce una migliore planarità del pezzo e minori stress residui (vedi figura 4).
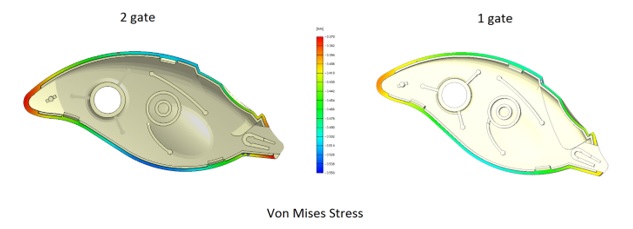
Ragionando sulla problematica dell’accoppiamento delle due metà del componente, si ipotizza che un maggior ritiro non sia problematico purché entrambe le parti siano realizzate con la stessa tipologia di stampo, da cui deriva un ritiro molto simile.
Invece la planarità risulta un parametro più vincolante.
Pertanto si è scelto di proporre la soluzione con un solo gate, anche tenendo in conto che uno stampo a due piastre risulta più economico.
(MDXITA . prt 2018059_ Giorgio Nava )