Simulazione di riempimento dello stampo e produzione intelligente nell'ambito del programma Industry 4.0: sviluppo prodotto e sviluppo di processi tecnologici attraverso gli strumenti di simulazione CAE
Si vuole introdurre i concetti di sviluppo prodotto e processo nell'industria dello stampaggio a iniezione ed il percorso verso l'industria 4.0 attraverso una serie di articoli.
Questo articolo introduttivo, presenta l’evolversi della tecnologia di simulazione CAE, che è tra le più importanti per il miglioramento dei processi nel loro complesso.
Proseguiremo poi con l'automazione della gestione della produzione in altri articoli successivi.
L’ "Informazione", contenuto / forma / dinamica/ trasmissione / controllo/ evoluzione, è il punto chiave nel viaggio verso Industria 4.0.
Per il processo di stampaggio a iniezione, le informazioni contengono condizioni di processo, componenti e attrezzature, materiali e qualità del prodotto. Le informazioni derivano dai "dati" e le informazioni possono essere analizzate in "conoscenza", che è il principale motore/potere del progresso tecnologico.
Quindi, possiamo dire che Industry 4.0 è il processo di integrazione e applicazione di informazioni, dati e conoscenze, in un’ottica di miglioramento continuo. Nel tradizionale settore dell'ingegneria della plastica, le condizioni di processo, il design del prodotto e dello stampo si basano sulla trasmissione e sulla codifica dell'esperienza.
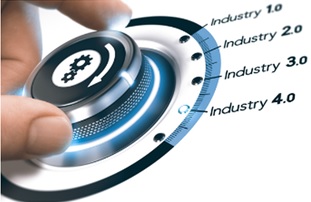
La maggior parte delle informazioni raccolte in azienda non ha una base dati completa e strutturata e non “può” essere trasformata in conoscenza, ovvero realizzare il passaggio da “capitale intellettuale” a “proprietà intellettuale”..
Nell'era dell'Industria 4.0, gli obiettivi principali dell'industria delle materie plastiche sono la raccolta di dati completi, l'automazione della distribuzione delle informazioni e la produzione di conoscenze con l'ausilio di calcoli computerizzati.
Quindi, come vengono trasferiti i dati dall'ambiente fisico reale (ad esempio i dati raccolti dai sensori) in concetti calcolabili, “matematici”, utilizzabili dai simulatori?
Secondo il Dr. Jay Lee, direttore del Intelligent Maintenance System Center, National Science Foundation e consulente per l'innovazione di produzione e servizi di Moldex3D, il concetto di Cyber-Physical System è "catturare, salvare, costruire modelli d’analizzare, estrarre, valutare, prevedere, ottimizzare e collaborare con i big data presenti, o recuperabili, con gli oggetti, tenendo conto dell’ambiente in cui i dati evolvono e si completano, delle attività.
Tutto questo va a completarsi con il design, con i test, lo sviluppo dei prototipi, il rispetto delle specifiche, le funzionalità e le prestazioni degli strumenti disponibili, per una profonda integrazione con l’ ambiente reale fisico.
Il completo patrimonio industriale (combinazione di asset tangibili e asset intangibili) è ulteriormente promosso dalla percezione delle proprie capacità, dall'auto- apprendimento e dell’auto-memorizzazione, dall'auto-coscienza e dall'auto-decisione ".
Il prefisso “auto” vuole incoraggiare ogni decisione verso un percorso di affidabilità e di ripetitibilità, a garanzia della continuità di prodotto e di processo nell’ottenimento del risultato finale.
Il modo per illustrare gli ambienti di elaborazione reali attraverso i modelli virtuali applicati nel processo di stampaggio a iniezione è, ad esempio, per noi di Moldex3D, l’ "analisi del riempimento dello stampo".
Può trasferire lo spazio reale in un ambiente virtuale in cui possiamo risolvere i problemi con la conoscenza, garantendo capacità veloce di correzione d’errore, tempi di reazione strettissimi, basso costo.
Nel processo di costruzione di un’ambiente di analisi ad elementi finiti, gli oggetti considerati includono stampo, cavità di stampo, il sistema di alimentazione, il sistema di raffreddamento, ecc.. L'analisi del campo fisico è interpretata dalle equazioni della meccanica dei fluidi (CFD).
Il modo di analizzare i componenti, i materiali plastici ed il processo (comprese le caratteristiche della macchina di stampaggio), consiste nel trasferire le loro proprietà termiche e fluide in equazioni di materiali che operano in un mondo virtuale, ma con stretta relazione a quello fisico reale.
Il movimento della macchina virtuale viene trasferito alla pressione, alla temperatura e alla velocità percorrendo le curve descrittive del materiale (Viscosità, PVT, Capacità termica, conducibilità termica, viscoelasticità, proprietà meccaniche ecc.).
Tutti gli elementi/componenti presenti nello stampaggio a iniezione menzionati sopra sono stati trasferiti in sistemi virtuali, in cui la qualità del prodotto e l'efficienza produttiva possono essere calcolati per garantire una corretta interpretazione dei risultati della simulazione ed un processo decisionale di produzione nel mondo reale.
L'evoluzione della tecnologia di integrazione del mondo virtuale e reale è data da due aspetti: la veridicità della costruzione di modelli e la tecnologia di analisi dei dati nel mondo virtuale.
Questi sono gli obiettivi che gli sviluppatori di software di simulazione continuano a perseguire.
Per quanto riguarda lo sviluppo di Moldex3D, il miglioramento e la completezza delle equazioni dei materiali è, da sempre, la missione principale del Centro di Ricerca sui Materiali Moldex3D, diretto da Dr. Tober Sun.
Ad esempio, la caratterizzazione e il corrispondente codice solutore di accoppiamento viscoelasticità nel software Moldex3D sono le nuove tecnologie che migliorano l'equazione tradizionale della viscosità per prevedere i corretti comportamenti del flusso.
Quindi, ora siamo in grado di prevedere in modo efficiente una varietà di difetti superficiali in comportamenti di flusso sbilanciati nelle fasi precedenti. Se espandiamo la capacità di previsione viscoelasticità all'analisi della deformazione, saremo in grado di osservare in che modo lo stress causato dal ritiro cambia insieme alla variazione della lunghezza del tempo di raffreddamento. Pertanto, l'analisi della deformazione del prodotto, alcune volte in presenza anche di deformazione dello stampo, sarà più vicina ai risultati del mondo reale in diverse condizioni di elaborazione.
Un altro importante progresso negli ultimi anni è l’utilizzo del modello virtuale e del movimento della pressa a iniezione. Nella simulazione convenzionale, il movimento della vite viene trasferito in termini di velocità e di pressione imposte al materiale fuso iniettato.
In questo modo, il comportamento del flusso fuso è “semplificato”. Prendiamo ad esempio una pressa idraulica con circuito ad anello chiuso, nella fase di iniezione vera e propria, la macchina confronta la velocità misurata e con l’input della velocità di iniezione per decidere il movimento della vite. La velocità di movimento della vite sarà aumentata o diminuita dal controller che agisce proporzionalmente sulla che viene regolata. La velocità di reazione di questo circuito chiuso, accompagnata all’inerzia del sistema nel suo complesso, è il fattore chiave della stabilità di produzione della macchina. Con un design del prodotto non corretto o grandi variazioni della pressione di iniezione, ci vorrà più tempo per stabilizzare il controllo della reazione del circuito ad anello chiuso.
Nell'ambiente Industry 4.0, la stabilità e ripetitibilità in fase di produzione è la condizione necessaria per un processo automatico. Pertanto, la costruzione del modello virtuale del movimento della macchina nella simulazione è particolarmente importante.
La prossima volta introdurremo le diverse soluzioni dei fornitori di macchine a iniezione per aiutare i clienti a sviluppare competitività nel loro viaggio verso Industry 4.0.
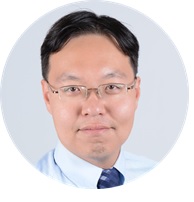
Dr. Tober Sun.
Direttore, Centro di ricerca materiale del sistema CoreTech (Moldex3D)
Con un dottorato in Polymer Science presso l'Università del Connecticut, l'esperienza del Dr. Sun è nella ricerca di materiali compositi, biomedicali, polimeri degradabili, applicazioni di materiali plastici in progetti industriali, reologia dei polimeri, trattamento dei polimeri e proprietà fisiche dei polimeri.
È stato responsabile della divisione supporto tecnico Moldex3D e del progetto automobilistico ed è docente a lungo termine dei seminari e dei corsi professionali globali di Moldex3D.
Un grazie particolare da parte nostra di Moldex3D Italia per la competenza, disponibilità e precisione nella attività di supporto ai nostri Clienti.
Articolo liberamente tradotto ed ampliato - Moldex3D ITALIA – Giorgio Nava prt_2018_044