Principi di base in ambiente CAE di analisi e simulazione dei processi di stampaggio ad iniezione termoplastica
Di seguito diamo alcune indicazione di base sul come settare i parametri di controllo in un sistema CAE dedicato all’analisi ed alla simulazione, sia di prodotto sia di processo, per lo stampaggio ad iniezione in ambiente plastica
Impostare correttamente le condizioni di processo, oltre a considerare le differenze note tra i parametri di simulazione e le reali impostazioni dello stampaggio a iniezione, sono di grande importanza, perché aiutano a spiegare correttamente l’influenza dei dati di simulazione e la previsione dei difetti o l'analisi delle cause di scarto.
Vediamo assieme come impostare i parametri di processo per la simulazione 3D dello stampaggio a iniezione termoplastica con Moldex3D.
Procedura guidata per il processo Moldex3D
È possibile definire le impostazioni del processo di stampaggio a iniezione in Process Wizard (Figura 1) di Moldex3D utilizzando diversi metodi.
Fig. 1. Procedura guidata per il processo Moldex3D.
Impostazioni di processo per un ciclo di stampaggio completoI parametri chiave più importanti in una condizione di processo per la simulazione possono essere riassunti in 7 elementi che verranno interpretati rispettivamente di seguito, quindi essenzialmente 7 passi da seguire:
1. Velocità e profilo di iniezione
La portata volumetrica è uno dei parametri più importanti nel processo di stampaggio a iniezione termoplastico. La portata influisce sull'aspetto e sulla struttura della parte stampata, sulle sollecitazioni termiche sullo stress residuo nel pezzo stampato, sul restringimento e sulle deformazioni indotte, sulle caratteristiche meccaniche oltre ad altre caratteristiche qualitative, non secondarie, delle parti stampate a iniezione.
Una portata troppo alta o troppo bassa può causare vari tipi di riempimento non corretto e altri problemi.
La procedura guidata del processo imposta la portata allo stesso modo delle macchine di stampaggio a iniezione effettive (Machine Mode Analysis), con un gradino (Fig. 2) o un profilo di portata lineare. Moldex3D tiene automaticamente conto della compressione del fuso nel cilindro (barile) di riscaldamento durante l'iniezione.
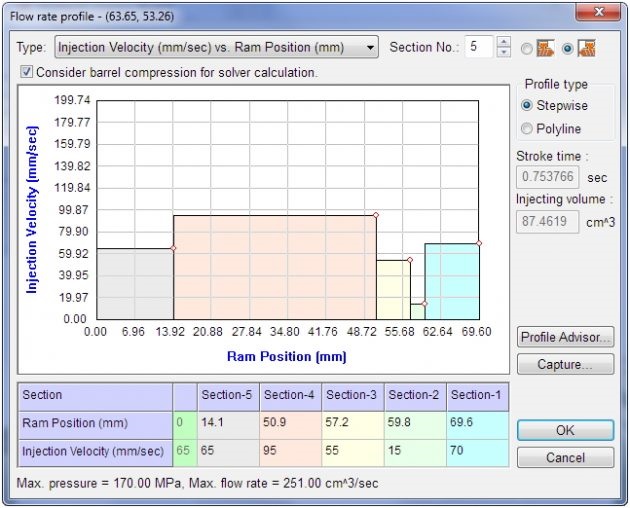
Fig. 2. Impostazione di un profilo di portata graduale
2. Pressione di iniezione
La pressione di iniezione viene impostata come profilo sia nello stampaggio a iniezione effettivo sia in ambiente di simulazione. Come nella fase di iniezione in condizioni di processo normali (senza instabilità del flusso e senza aria catturata nella cavità dello stampo), la pressione del fuso, al fronte del flusso, equivale alla pressione atmosferica, la pressione di iniezione massima è uguale alla caduta di pressione lungo il percorso del flusso. La dipendenza della massima pressione di iniezione sulla portata (per un'ampia gamma di portate) ha un minimo (Fig. 3).
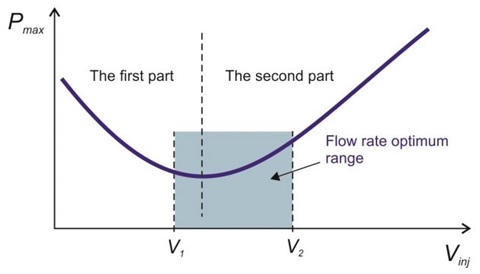
Fig. 3. Pressione di iniezione massima (Pmax) rispetto alla velocità di iniezione volumetrica (V-inj) con caduta di pressione (1a parte) e aumento (2a parte) degli intervalli; portata ottimale della portata (da V1 a V2).
3. Temperatura di fusione
Di default, corrisponde alla temperatura di fusione raccomandata dal produttore di materiale termoplastico e normalmente corrisponde al punto medio dell'intervallo di temperatura del fuso.
La figura 4 mostra alcune problematiche di stampaggio a iniezione relative alla temperatura del fuso all'ingresso della cavità dello stampo e alla pressione massima durante l'iniezione.
La pressione di iniezione ridotta o la temperatura del fuso conducono al tiro corto, mentre elevate pressioni di iniezione portano a creare bruciature a causa dell'elevata pressione media nella cavità dello stampo.
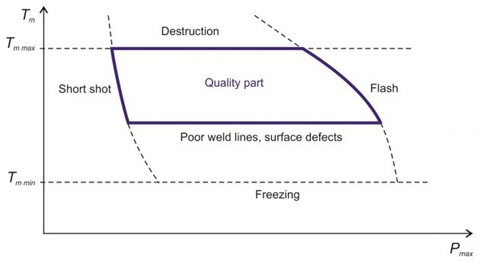
Fig. 4. Temperatura di fusione (?m) rispetto alla massima pressione di iniezione (Pmax) e tipici problemi di iniezione; Tm min è la temperatura minima del fuso, Tm max è la temperatura massima del fuso.
4. Pressione e profilo durante la fase di impaccamento (post-compressione)
Sia per un effettivo processo di stampaggio a iniezione, sia per la simulazione della fase di impaccamento, il profilo di pressione viene impostato in modo graduale o lineare nel tempo (Fig. 5), seguendo un profilo caratteristico. La pressione di riempimento ad ogni passaggio può essere impostata come valore assoluto o relativo (pressione massima di compressione ? forza di chiusura dello stampo).
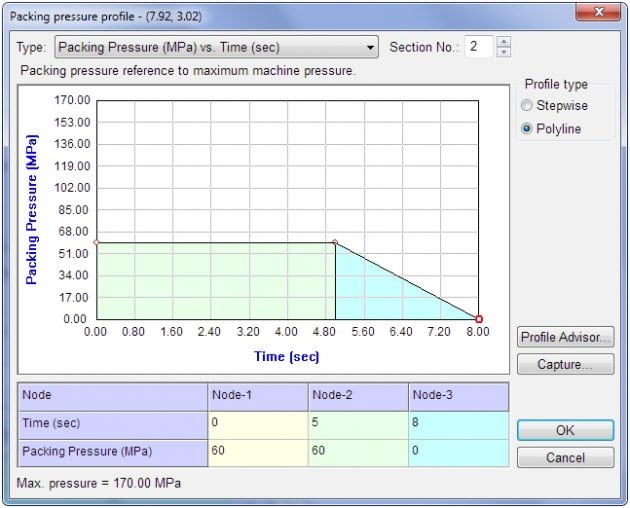
Fig. 5. Impostazione di un profilo di pressione con diminuzione della pressione lineare.
La pressione di riempimento iniziale determina la portata del fuso nella cavità dello stampo in fase di riempimento dopo il passaggio alla modalità di controllo della pressione (momento di switch volume/pressione).
Una bassa pressione iniziale del premistoppa durante lo stampaggio a iniezione in presenza pareti grandi e/o spessori sottili può portare al raffreddamento del fronte del fuso e, quindi, causare difetti superficiali (flowmarks e risucchi), elevate tensioni residue, ecc.
Una pressione di confezionamento troppo elevata provoca una velocità elevata del flusso che può anche causare un elevato stress residuo e altri problemi.
La figura 6 fornisce il tempo di impaccamento rispetto al diagramma della pressione di impaccamento e indica i problemi tipici della fase di post-compressione.
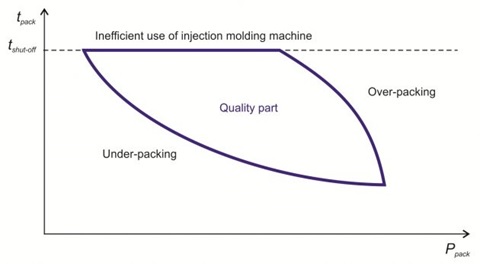
Fig. 6. Tempo di impaccamento (t-pack) rispetto al diagramma della pressione di impaccamento (P-pack) e problemi di imballaggio.
5. Tempo di impaccamento
Normalmente il tempo di impaccamento è abbastanza ampio Si può determinare questo tempo automaticamente o manualmente con diversi metodi: stabilizzando il peso del pezzo nel tempo, riducendo drasticamente il flusso di fuso attraverso un gate, ecc.
6. Temperatura dello stampo
L'opzione più semplice quando si simula il processo di raffreddamento dello stampaggio in Moldex3D è impostare una temperatura dello stampo uniforme (utilizzo del monoblocco stampo).
Se si simula il processo di raffreddamento dello stampo tenendo conto della progettazione dei canali di raffreddamento, le distribuzioni della temperatura dello stampo saranno determinate dalle impostazioni del processo, tra cui temperatura e portata del fluido refrigerante (Fig. 7).
La portata del liquido refrigerante è impostata per garantire una corretta turbolenza del flusso del refrigerante nei canali di raffreddamento (normalmente i valori di Reynolds consigliati sono da 5.000 a 10.000).
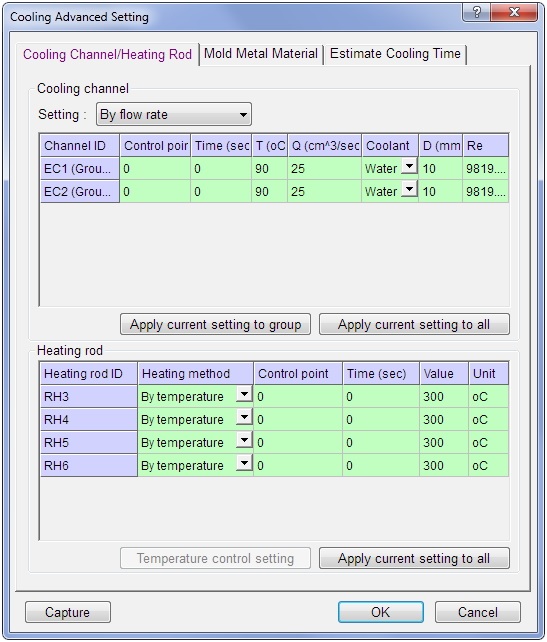
Fig. 7. Impostazioni di processo per canali di raffreddamento stampo e riscaldatori di un sistema di canali caldi.
7. Tempo di raffreddamento
Di norma, si imposta il tempo di raffreddamento per garantire che la parte stampata venga raffreddata fino alla temperatura di espulsione richiesta. Una rimozione troppo anticipata della parte dello stampo comporta un’ulteriore contributo di deformazione della parte. Tuttavia, si può normalmente rimuovere dallo stampo gli elementi con pareti spesse con una rigidità sufficientemente elevata (prodotta da un materiale termoplastico con un alto modulo di elasticità) senza per forza dover attendere la piena solidificazione interna. Un'eccezione degna di nota sono le parti con requisiti di precisione dimensionali molto stretti.
L'aumento del tempo di raffreddamento riduce la deformazione delle parti (rilassamento e riduzione dello stress nel pezzo), ma riduce le prestazioni delle attrezzature di stampaggio a iniezione, allungando il ciclo totale.
Ottimizzazione delle impostazioni di processo
Moldex3D include diversi metodi volti a ottimizzare le impostazioni del processo di stampaggio a iniezione.
Per valutazioni rapide, è possibile utilizzare algoritmi di determinazione automatica della velocità di flusso e profili di pressione dell'imballaggio semplicemente premendo il pulsante Profile Advisor in Process Wizard (Fig. 2 e 5).
Questi algoritmi utilizzano i dati di simulazioni precedentemente eseguite per lo stesso grado di materiale e materiale termoplastico.
Il modulo Moldex3D Expert (DOE Design-Of-Experiment) fornisce una valutazione delle impostazioni del processo che influiscono sulle caratteristiche del processo di uscita e aiuta a trovare una modalità di stampaggio a iniezione ottimale utilizzando tecniche di progettazione e simulazione avanzate esperimento.
(MDXITA. prt 2018006_Giorgio Nava)