L’analisi accoppiata porta ad un livello ottimale di accuratezza nei risultati
La tecnologia di calcolo ad alta precisione ed accuratezza sviluppata con Moldex3D nella simulazione di riempimento di stampi può aiutare gli utenti a prevedere i possibili difetti del prodotto prima della produzione effettiva di stampi.
L’utilizzo di Moldex3D facilita un efficiente processo produttivo e aiuta a creare prodotti di alta qualità riducendo ulteriormente i costi presenti in un percorso tradizionale try&error (prova, sbaglia e correggi).
Al fine di fornire risultati di simulazione più precisi e dati di analisi affidabili, nella progettazione per sia del prodotto sia degli stampi, è ora disponibile la capacità di simulazione di processo completamente accoppiata in Moldex3D.
Con un’analisi di questo tipo, i dati di simulazione possono essere confrontati, portando l'accuratezza dell'analisi ad un livello ottimale. Vedremo di seguito il significato di cosa vuol dire muoversi in modo convenzionale o in modo accoppiato.
Il Processo di analisi convenzionale
Riempimento, raffreddamento, impaccamento/postcompressione e deformazione sono calcolati con risolutori separati e eseguiranno analisi in sequenza anziché “contemporaneamente”.
I dati vengono trasmessi tra diversi codici di programma attraverso la comunicazione di files, ovvero un processo a senso unico.
Ad esempio, quando l'analisi di riempimento sta procedendo, l'analisi del raffreddamento è già terminata, significa che l'analisi di riempimento e raffreddamento non può interagire immediatamente in modo accoppiato.
Inoltre, lo spazio richiesto in memoria e su disco rigido aumenta all’aumentare delle comunicazioni tra fase e fase.
Il Processo di analisi accoppiato.
Nel processo di analisi completamente accoppiato, i calcoli di riempimento, raffreddamento, impaccamento e deformazione sono integrati tra loro, interagiscono e possono essere eseguiti contemporaneamente, quindi le entità fisiche che costituiscono stampo possono influenzarsi tra loro.
I risultati dell'analisi completamente accoppiati possono essere più affidabili e coerenti con lo stampaggio del mondo reale. Questo può anche essere utilizzato per prevedere aree di accumulo di calore di prodotti geometrici complessi.
Il caso della Figura 1 mostra la differenza tra la simulazione di processo convenzionale e pienamente accoppiata.
Il riscaldamento in fase di riempimento interagisce frequentemente con la temperatura dello stampo in fase di raffreddamento. Le interazioni possono essere considerate in “analisi completamente accoppiate”, in modo da poter calcolare i risultati di accumuli termici in modo corretto ed evidente.
Ciò è dimostrato dalla differenza dei risultati dell'analisi della pressione tra due tipi di simulazione.
La temperatura è più alta in analisi accoppiata è 97.5 ° C. Questa è 11,4 ℃ superiore a quello in analisi convenzionale (86,1 ℃).
Poiché i dati di pressione possono essere forniti più facilmente, la pressione interna media del prodotto in analisi completamente accoppiata è 1,75MPa, che è 0,29MPa inferiore rispetto all'analisi convenzionale (2,04MPa).
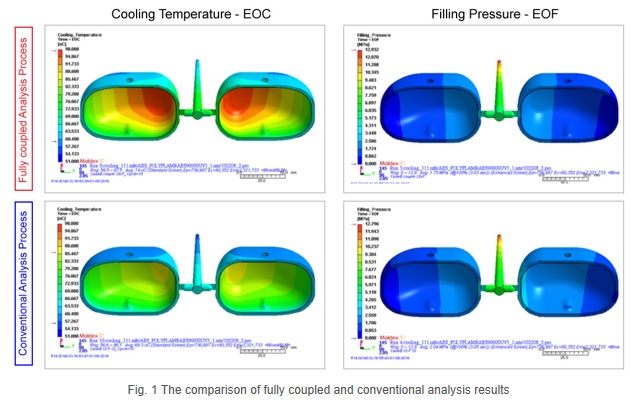
Fig. 1 Il confronto di risultati di analisi completamente accoppiati e convenzionali
Come mostrato nel caso precedente, l'analisi completamente accoppiata di Moldex3D porta ad un aumento considerevole del livello di accuratezza dei risultati, per una migliore valutazione da parte dell’operatore.
Ciò è particolarmente ideale per applicazioni complesse (lenti ottiche, massima precisione di μm) o su particolari di una certa grandezza come le parti automobilistiche (esempio un paraurti in PUR) dove le tolleranze sono molto strette e/o le deformazioni sono di difficile controllo.
L'analisi completamente accoppiata di Moldex3D consente agli ingegneri del prodotto un corretto orientamento in fase di progetto ed una maggiore sensibilità alle problematiche di stampaggio, riducendo notevolmente i costi di sviluppo prodotto e di processo.
(MDXITA . prt 20171020_a Giorgio Nava)